In the entire production process of an asphalt mixing plant, the drying drum serves as the “heart” of the operation, with its performance directly impacting the quality of the asphalt, production efficiency, and environmental compliance. It is the core equipment ensuring that asphalt mixtures achieve high strength and stability, playing a crucial role in the entire asphalt production process. This article will delve into the functions, key components, working principles, and indispensable role of the drying drum in asphalt production, providing you with a comprehensive understanding of this core equipment.
What is a Drying Drum in an Asphalt Mixing Plant
A drying drum is a cylindrical rotating device primarily used to heat and dry aggregates, bringing them to the required temperature and moisture content for production. Its core function is to remove 5%-6% or more moisture from the aggregates through efficient heat exchange, ultimately controlling residual moisture content below 0.5%, and heating the aggregates to the optimal mixing temperature. This process directly impacts the strength and stability of the asphalt mixture.
In the construction industry, the drying drum holds an irreplaceable position. Unlike dryers used in other industries, such as mining, it has higher requirements for performance and precision due to the special nature of asphalt production, making it an indispensable key piece of equipment in asphalt mixing plants.
Components of the Drying Drum
The various components of the drying drum work together to determine its performance and function. The following provides a detailed analysis of each component and its contribution to the drying drum’s functionality:
Rotating Drum Shell
The rotating drum housing is the cylindrical steel core of the drying drum, driven by heavy-duty motors and gear systems to rotate continuously during operation. It is typically installed with a precise 3.5° incline angle (this angle is pre-set at the factory, and only the foundation level needs to be ensured on-site). This angle design ensures that aggregates move smoothly along the drum’s axial direction toward the discharge end under the influence of gravity, while providing sufficient time for heat exchange.
Lifting Blades (Flights)
The lifting blades inside the drum are critical for enhancing thermal efficiency. These blades are designed in specific shapes (such as L-shaped, T-shaped, Z-shaped, etc.). As the drum rotates, the blades lift and scatter the aggregate, forming a uniform material curtain. This process significantly increases the contact surface area between the aggregate and high-temperature gases, thereby accelerating the drying process and reducing fuel consumption. Well-designed blades can significantly improve the thermal efficiency of drum-type asphalt mixing plants, resulting in more stable asphalt quality and lower production costs.
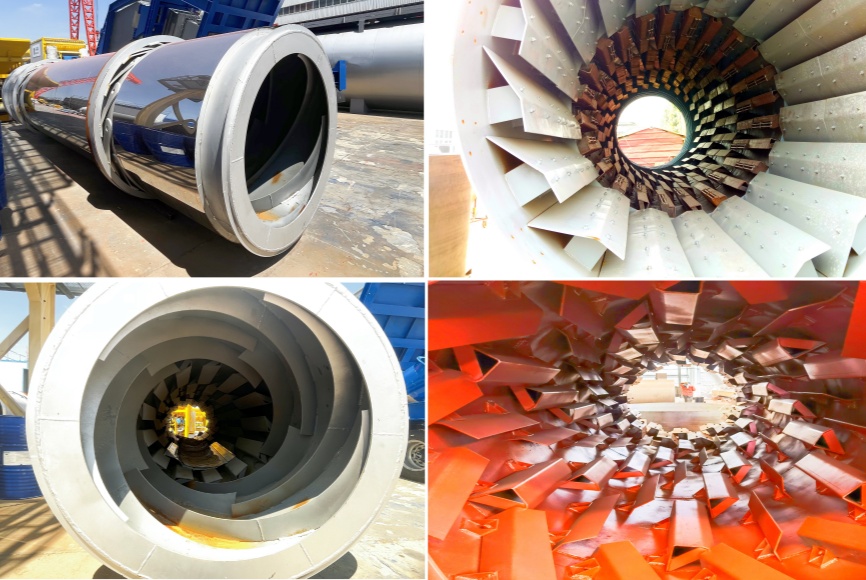
Burner System
A burner system is installed at one end of the drying drum, responsible for generating the flame and high-temperature gas required to heat the aggregate. The burner can use various fuels such as diesel, heavy oil, or natural gas, depending on the availability and cost of local fuel. The burner must provide a stable, adjustable flame to maintain a constant temperature inside the drum. Advanced burner systems also help reduce emissions and improve fuel efficiency.
Dust and Emission Control
During aggregate drying and heating, fine particles and emissions are generated. The drying drum is typically connected to a primary dust collector (such as a cyclone separator) and a secondary baghouse dust collector or wet scrubber. These systems ensure compliance with environmental regulations, which is particularly important at urban construction sites. Proper dust control also protects the mechanical components of the asphalt mixing plant from wear and tear, extending the equipment’s service life.
Working Principle of the Drying Drum in an Asphalt Mixing Plant
The drying drum operates in a clear and orderly manner within the asphalt mixing plant, with each step laying the foundation for the production of high-quality asphalt mixture.
Aggregate Feeding
Cold aggregate is conveyed via a feed conveyor belt to the feed hopper of the drying drum and then enters the drum through the feed opening. The drum inlet is equipped with a tight sealing device to minimize cold air infiltration and prevent heat efficiency loss.
Heating and Drying
The burner is located near the discharge end of the drying drum, with mainstream equipment burners capable of providing 24 MW of power. Through medium-pressure mechanical and air-assisted mixing atomization technology, fuel oil and compressed air are uniformly mixed within the valve body before being sprayed and ignited, forming a stable high-temperature heat source. The flame and flue gas temperatures can reach hundreds of degrees Celsius, flowing along the inclined direction of the drum toward the feed end, where they undergo efficient counter-current heat exchange with the counter-moving aggregate.
The carefully designed multi-row curved scraper blades inside the drum are key to improving thermal efficiency: as the drum rotates at a set speed, the blades continuously lift and disperse the aggregate, forming a uniform material curtain to ensure that every grain of aggregate comes into full contact with the high-temperature flue gas. After preliminary heating in the material curtain zone, the aggregate enters a specially designed radiation zone, where it is surrounded by an insulated box and adheres to the inner wall of the drum, rotating along with the drum body. This prevents turbulence in material flow from affecting flame shape while further stabilizing aggregate temperature through radiant heat exchange.
The drum body is welded from heat-resistant and wear-resistant boiler steel plates into a cylindrical shape, ensuring stable thermal expansion performance even in high-temperature environments. Its drive system is powered by 4×22kW direct-drive motors, which rotate the idler rollers to provide the drum with uniform and stable rotational force.
Moisture Removal
Moisture in the aggregate rapidly evaporates into steam at high temperatures, mixing with flue gas from combustion to form a dust-laden gas stream. The drum is connected to the dust collector via a short pipeline, utilizing the negative pressure generated by the exhaust fan (typically maintained at 4-8 mm water column) to draw the mixed gas stream into the dust collection system. This compact pipeline design reduces heat loss by 10-15°C, indirectly lowering burner energy consumption by approximately 2%.
Discharge
After drying and heating, the aggregate that meets the specified temperature and moisture content requirements is discharged from the discharge end of the drying drum and enters the subsequent vibrating screen screening process. To ensure the longitudinal stability of the drum, thrust wheels are installed on both sides of the support ring at the feed opening. During normal operation, the support ring remains between the two wheels or lightly contacts one of them, preventing axial movement of the drum body from affecting discharge stability.
The Role of the Drying Drum in Asphalt Mixing Plant
As the core equipment of an asphalt mixing plant, drying drums play a pivotal role throughout the entire asphalt production process, exerting a decisive influence on the quality of the final product and production efficiency.
Ensuring Asphalt Quality
The drying drum employs a precise temperature and humidity control system, utilizing counterflow heating principles. It uses high-temperature flue gas generated by the burner to flow countercurrently with the aggregate, precisely removing excess moisture from the aggregate and strictly controlling residual moisture content below 0.5%. This process effectively prevents water-related damage to asphalt mixtures after paving, such as peeling or potholes. Additionally, the unique blade structure design inside the drum ensures uniform heating of the aggregate during rotation, rapidly raising the temperature to the optimal mixing temperature range of 160°C to 180°C. Only when the moisture content and temperature of the aggregate meet the standards can the asphalt fully penetrate the aggregate surface, forming a high-strength asphalt film, thereby ensuring the strength and stability of the asphalt mixture and laying a solid foundation for the long-term durability and rutting resistance of the asphalt pavement.
Improved Production Efficiency
The drying drum features an efficient heat exchange design, equipped with high-temperature-resistant double-layer spiral blades and an optimized airflow structure, enabling the aggregate to form a uniform material curtain inside the drum. This significantly increases the contact area with high-temperature flue gas, achieving rapid and uniform drying and heating. Compared to traditional equipment, the new drying drum reduces aggregate heating time by 20%-30%, significantly shortening the production cycle. Additionally, its advanced combustion system, combined with intelligent temperature control devices, automatically adjusts fuel supply based on aggregate feed rate and initial temperature, improving heat transfer efficiency by over 15% and effectively reducing fuel consumption. This efficient and energy-saving operation mode not only increases the asphalt mixing plant’s output per unit time but also reduces overall operational costs, enhancing the company’s market competitiveness.
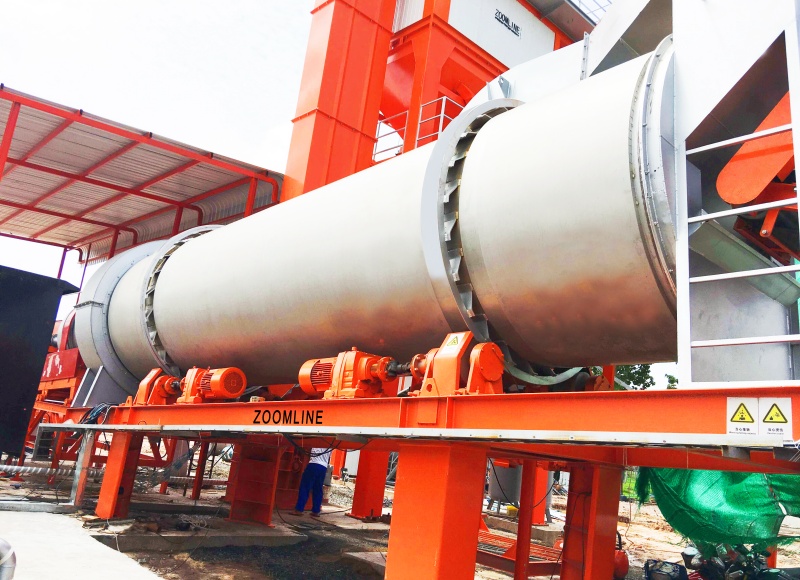
Achieving Environmental Compliance
The drying drum integrates an advanced dust and emissions control system, featuring a multi-stage dust collection system composed of an internal cyclone dust collector and a baghouse dust collector, which efficiently captures fine particulate dust generated during production, achieving a dust collection efficiency of over 99.5%. Additionally, by configuring a selective catalytic reduction (SCR) system and an oxidation catalytic converter (DOC), harmful gases such as nitrogen oxides and carbon monoxide generated during combustion can be effectively treated, ensuring emissions strictly comply with national and local environmental regulations. In environmentally sensitive areas like urban construction sites, this system significantly reduces dust pollution and harmful gas emissions, minimizing impacts on surrounding residents’ lives and the ecological environment, thereby supporting the company’s goal of achieving green construction.
Extending Equipment Lifespan
In addition to meeting environmental protection requirements, the dust control system of the drying drum also plays a crucial protective role for the equipment itself. The efficient dust removal system reduces dust accumulation on critical components such as the drum inner walls, bearings, and transmission parts, preventing mechanical failures caused by dust particle wear. Additionally, the drum interior is equipped with wear-resistant liners and special coatings, further enhancing the equipment’s resistance to erosion. Regular maintenance and cleaning of the dust collection system to remove accumulated dust ensures long-term stable operation of the equipment, effectively extending the service life of the drying drum and the entire asphalt mixing plant. This reduces maintenance frequency and replacement costs, saving businesses substantial equipment management expenses.
Types of Drying Drums in Asphalt Plants
In asphalt mixing plants, there are primarily two types of drying drums, with the main difference lying in the relationship between aggregate flow and airflow.
Parallel Flow Dryers
In a parallel flow dryer, the aggregate flow and airflow are in the same direction. Cold aggregate and flame enter the dryer through the same opening, and the material moves toward the outlet. This type of dryer is typically more suitable for continuous mixing plants, capable of meeting continuous production requirements, and demonstrates efficient and stable heating performance in high-throughput operations.
Counter-Current Dryers
In a counterflow dryer, flame and aggregate enter through different openings. Generally, counterflow dryers are used in batch-type mixing plants. Compared to parallel-flow dryers, counterflow dryers have better heat exchange efficiency, enabling more efficient utilization of thermal energy, and offer certain advantages when processing aggregates with higher moisture content.
The Advantages of the Drying Drum Compared To the Traditional Dryer
Drying drums demonstrate significant advantages over traditional dryers in multiple aspects, making them indispensable equipment in asphalt mixing plants.
Higher Drying Efficiency
In the drying drum, hot airflow directly contacts the material, rapidly evaporating moisture from the material’s surface. Additionally, the drum’s design enhances thermal conductivity efficiency, accelerating the drying process. Furthermore, drying drums typically offer multiple drying programs, allowing selection of the appropriate program based on aggregate type to further improve drying efficiency. In contrast, traditional dryers use high-temperature hot air to remove moisture from the material, resulting in lower drying efficiency, slower speeds, and potential uneven drying.
Better Energy Efficiency and Environmental Friendliness
The heat source for drying drums can utilize multiple energy sources, such as burners, steam, and electric heaters, enabling diversified energy use. Additionally, the equipment itself can recover heat, reducing energy waste. Furthermore, the exhaust port of the drying drum can be equipped with a flue gas purifier to clean the flue gas before emission, meeting environmental requirements. Traditional dryers are relatively weak in terms of energy efficiency and environmental friendliness, with low energy utilization efficiency and potential environmental pollution.
Wider applicability
The drying drum is suitable for drying various materials, including powders, particles, blocks, and even sticky materials. Its processing capacity can be adjusted according to different material quantities, making it suitable for the production needs of various scales. Traditional dryers have a relatively narrow application range and are typically only suitable for drying specific types of materials.
More Convenient Operation and Maintenance
The drying drum is easy to operate; simply load the material into the drum, set the drying time and temperature, and you’re done. Maintenance is also relatively straightforward, requiring only regular cleaning and lubrication. Additionally, the drying drum typically comes equipped with various features, such as delayed start and drying sensors, further enhancing usability. While traditional dryers are also relatively easy to operate, they may lack advanced features like intelligent temperature control systems or drying sensors, and maintenance may be more complex.
Better Wrinkle Removal Effect (for material processing)
The design of the drying drum allows the material to continuously roll during the drying process, thereby reducing the formation of wrinkles. In contrast, traditional dryers may cause the material to remain in the same position for extended periods during the drying process, resulting in poorer wrinkle removal effects. However, in asphalt production, this advantage primarily manifests in the uniformity of aggregate processing, which indirectly impacts the quality of the asphalt mixture.
How to Choose the Right Drying Drum for Your Asphalt Plant
Selecting the appropriate drying drum is critical for the efficient operation of an asphalt mixing plant. The following are some key considerations.
Focus on Thermal Performance
Reducing the moisture content of cold aggregate is the most effective way to improve thermal performance and reduce energy consumption. However, it is difficult to significantly control the moisture content of raw materials before drum drying. To better remove moisture from cold aggregate, special attention should be paid to the drum’s structure. First, the drum body should be covered with an insulation layer. Second, a stainless steel structure has excellent insulation properties, reducing heat loss and improving thermal efficiency.
Consider Structural Design
A drum installed at an angle facilitates the discharge of dried material. Additionally, attention should be paid to the material and shape of the blades inside the drum. Currently, blades on the market come in geometric shapes such as L-shaped, T-shaped, and Z-shaped. Blades with geometric shapes can more effectively lift aggregates within the rotating drum, improving heat exchange efficiency.
Regarding the drive ring, for safety reasons, drive wheels and rollers made of stainless steel or alloy steel are the optimal choice. Additionally, idlers driven by motors and gear assemblies via polymer friction offer the advantages of high stability and low noise.
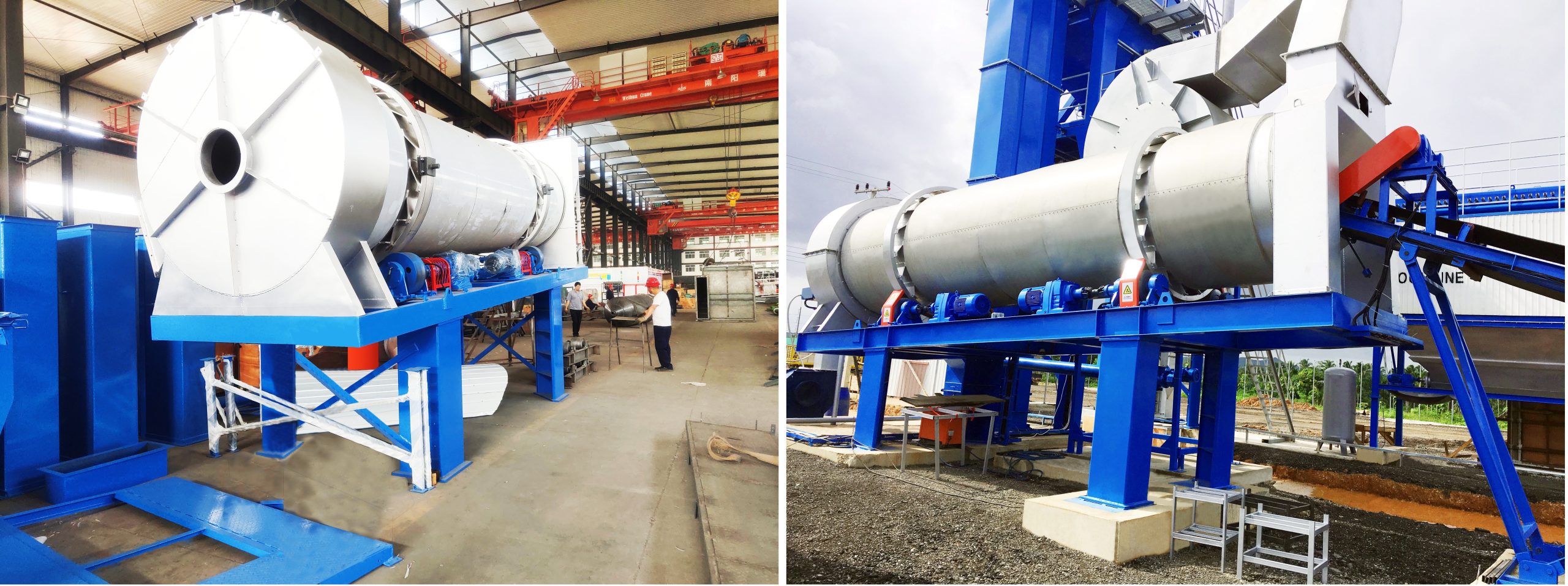
Evaluating the Burner System
The burner is the core component of the combustion system. A high-quality burner can significantly reduce fuel costs. To ensure low exhaust emissions, selecting burners from world-renowned brands is generally a reliable choice, such as Italian fuel burners, which are an excellent option.
Inspecting the Sealing System
Ensure that the drying drum you purchase has excellent sealing performance. Professional sealing devices can significantly reduce heat loss, maintain the stability of aggregate properties, and thereby improve the quality of asphalt mixtures.
Maintenance Tips for Drying Drums
Proper maintenance is crucial for the long-term efficient operation of drying drums. Below are some key maintenance tips.
Daily Inspections
Before the asphalt mixing plant begins formal operations, the drying drum must be tested and inspected to verify that all pipes are securely connected, the entire machine is properly lubricated, the motor can start normally, all pressure valves function stably, and all instruments operate normally. Timely identification and resolution of potential issues prevent failures during production.
Proper Operating Practices
When starting the asphalt mixing plant, manual operation should only be switched to automatic control after the specified production capacity and discharge temperature are reached. Aggregates must be kept dry and in standard condition to maintain a constant temperature as they pass through the drying drum. When all aggregates are fed into the drying process, moisture content may fluctuate, requiring frequent use of the burner to compensate for moisture changes. During aggregate processing, the direct water content remains largely unchanged, but the accumulated combustion water increases, and the water content in deposited aggregates may vary, necessitating timely adjustments.
Post-Operation Maintenance
When the asphalt mixing plant is not in operation, aggregate supply should be stopped. After daily operations, the equipment should be operated to discharge the aggregate into the dryer. After the material in the hopper leaves the combustion chamber, the combustion chamber should be closed and allowed to idle for approximately 30 minutes to cool down, reducing the impact on the machine and ensuring normal operation. Simultaneously, the drying drum fixed rings should be synchronously installed on all rollers to ensure drum stability.
Conclusion
As the core equipment of an asphalt mixing plant, the drying drum is the cornerstone of the asphalt production process, determining asphalt quality, production efficiency, and environmental responsibility. From removing moisture from aggregates, heating aggregates, to ensuring the stability of asphalt mixtures, every stage of the drying drum is critical.
When selecting a drying drum, factors such as thermal performance, structure, burner system, and sealing system must be comprehensively considered to ensure suitability for specific production requirements. Additionally, maintenance measures such as daily inspections, proper operation, and post-use care can extend the service life of the drying drum and ensure its long-term efficient operation.
Investing in a well-designed and properly maintained drying drum is key to ensuring that an asphalt mixing plant can produce asphalt for an extended period with high performance. Whether in urban construction or highway construction, drying drums provide a solid foundation for the construction of high-quality asphalt pavements.