Know About An Asphalt Drum Mix Plant
An asphalt drum mix plant is a continuous mixing facility that produces hot mix asphalt for road construction and maintenance. In the field of road construction and maintenance, asphalt drum mix plants are indispensable key equipment. Compared to traditional batch mix asphalt plants, their continuous production mode eliminates batch limitations. By continuously conveying materials and dynamically mixing them, they achieve a production capacity of 120-320tons per hour, providing efficient support for large-scale road projects such as highways and urban expressways. This equipment is particularly suitable for infrastructure projects with tight schedules, as its 24/7 uninterrupted operation capability significantly accelerates project progress and effectively reduces overall construction costs. These plants are noted for their dependability, ease of operation, and little maintenance, making them a popular choice among contractors and construction business.
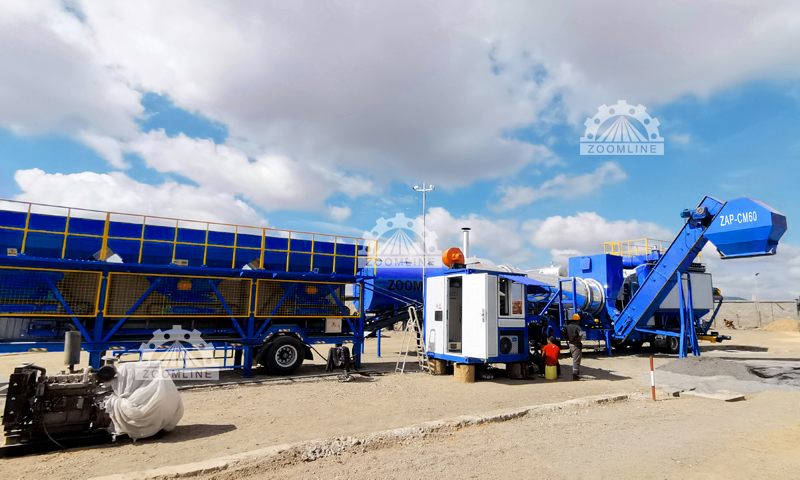
How Does an Asphalt Drum Mix Plant Operate
Step 1: Loading aggregate into the cold aggregate bin
The cold aggregate bin is the starting point for the operation of an asphalt drum mixer plant. Bins of different specifications are responsible for storing various types of aggregate. The adjustable gates on the bin body enable precise control of the flow of aggregate into the next stage, ensuring a stable supply of aggregate and laying the foundation for subsequent production processes. Proper loading of aggregate is critical for the smooth operation of the mixer plant. Improper loading may lead to production interruptions or quality issues.
Step 2: Single-layer vibrating screen screening
After entering the cold aggregate silo, the aggregate passes through a single-layer vibrating screen. This equipment uses high-frequency vibration to separate oversized aggregate, preventing it from entering the drying drum. The screened aggregate has a more uniform particle size, which helps improve the quality of the final asphalt mixture and ensures the effectiveness of road paving.
Step 3: Weighing Conveyor Transmission
The weighing conveyor transports the screened aggregate to the drying drum. Equipped with weighing sensors, it accurately measures the aggregate weight in real-time and transmits the data to the control panel. Precise aggregate weighing is critical for ensuring accurate asphalt mixture proportions, directly impacting the strength and durability of the pavement.
Step 4: Drying Mixing Drum Operation
The drying and mixing drum is the core component of the asphalt drum mixing plant. The drum is inclined at a certain angle and rotates continuously. The blades inside lift and scatter the aggregate, allowing it to fully contact hot air in the front half of the drum to complete drying. When the aggregate moves to the rear half of the drum, it is thoroughly mixed with the injected asphalt and filler to form a uniform asphalt mixture.
Step 5: Burner Fuel Tank Power Supply
The burner fuel tank stores various fuels such as diesel, heavy oil, and natural gas, providing the heat source for the drying and mixing drum. The efficient burner, in conjunction with the fuel tank, enables precise control of heating temperature, ensuring thorough drying of the aggregate while reducing fuel consumption and improving production efficiency.
Step 6: Asphalt storage tank preparation
The asphalt storage tank is used to store and heat asphalt. Depending on production requirements, storage tanks are available in various specifications and capacities. Heated asphalt becomes more fluid, facilitating uniform mixing with hot aggregate and ensuring stable asphalt mixture quality.
Step 7: Filling the Filler Hopper
The filler hopper primarily stores fillers such as lime and limestone powder. These fillers are added to the mixing drum according to the design formula of the asphalt mixture. Fillers enhance the adhesion and durability of the asphalt mixture, improving the performance of the pavement.
Step 8: Pollution control equipment purification
To meet environmental protection requirements, the asphalt drum mixing plant is equipped with dry dust collectors and wet dust collectors. Dry dust collectors capture large particles of dust emitted from the drum, while wet dust collectors further filter out fine dust particles, effectively reducing dust emissions during production and minimizing environmental pollution.
Step 9: Material Conveyor Transportation
The mixed asphalt mixture is transported by the material conveyor to a small hopper or storage silo, then loaded onto transport vehicles and transported to the road construction site. The material discharge process must ensure the temperature and uniformity of the mixture to avoid quality issues in road construction caused by improper transportation.
Types of Asphalt Drum Mix Plants
Downflow Drum Mix Asphalt Plant
In a downflow drum mixing plant, the aggregate and hot air flow in the same direction. After entering the drum, the aggregate quickly comes into contact with the hot air and begins drying and heating. This mode has a short production cycle and is suitable for projects that require a large amount of asphalt mixture in a short period of time, but the heating uniformity is relatively weak.
Counterflow Drum Mix Asphalt Plant
In a counterflow mixing plant, the aggregate and hot air flow in opposite directions. The aggregate enters from one end, while the hot air is injected from the other end, allowing the aggregate to come into contact with the gradually increasing temperature of the hot air inside the drum. This achieves more thorough drying and uniform mixing, resulting in higher-quality finished products. It is commonly used in projects with strict requirements for mix quality.
Double-drum Mix Asphalt Plant
A double-drum mixing plant features inner and outer drums. Aggregates are preheated or partially dried in the outer drum before entering the inner drum for thorough contact with hot air and asphalt mixing. This two-stage process enables precise control of heating and mixing, making it suitable for complex construction environments and high-standard engineering requirements.
Single-drum Mix Asphalt Plant
The single-drum mixing plant is the most basic type, with all processes—drying, heating, and mixing—completed within a single drum. It features a simple structure and lower costs, making it suitable for small-scale road projects or those with modest production volume requirements.
Key Components of an Asphalt Drum Mix Plant
Cold Aggregate Bin
The cold aggregate bin not only stores aggregate but also ensures a stable supply of aggregate in the correct proportions through precise flow control. A well-designed cold aggregate bin and precise control are essential for achieving continuous and stable production.
Single-Layer Vibrating Screen
The material of the screen mesh and the vibration frequency of the vibrating screen determine its screening efficiency. Regular inspection and maintenance of the vibrating screen ensure its normal operation, effectively preventing non-conforming aggregate from entering subsequent production processes.
Weighing Conveyor
The accuracy of the weighing conveyor directly affects the asphalt mixture ratio. Regular calibration of the weighing sensors is required during daily use to ensure accurate measurement data, thereby producing asphalt mixtures that meet standards.
Drum Drying
The inclination angle, rotation speed, and internal blade design of the drum significantly impact the drying and mixing efficiency of aggregates. Optimal drum parameter settings can enhance production efficiency and ensure the quality of the mixture.
Burner
The performance of the burner determines heating efficiency and fuel consumption. Selecting an efficient, energy-saving burner with automatic temperature control functionality can reduce production costs while ensuring a stable heating process.
Filler Hopper
The capacity and discharge control devices of the filler hopper must be reasonably configured according to project requirements. Accurate control of filler addition quantities can effectively enhance the performance of asphalt mixture.
Asphalt Storage Tank
The heating system and insulation performance of the asphalt storage tank are critical. Proper heating and insulation maintain asphalt flow-ability, ensuring smooth mixing with aggregates.
Pollution control unit
Different types of pollution control equipment are designed for dust particles of different sizes. Regular cleaning and maintenance of dust collectors ensure their efficient operation, enabling the mixing plant to meet environmental emission standards.
Control system
Control systems based on microprocessors or PLC are user-friendly and highly customization. Through this system, operators can monitor and adjust production parameters in real time, ensuring a stable and orderly production process.
Material Storage Silos
The capacity of material storage silos must be designed based on transportation vehicles and construction progress. A well-designed storage silo prevents asphalt mixture from being stockpiled or running out, thereby improving construction efficiency.
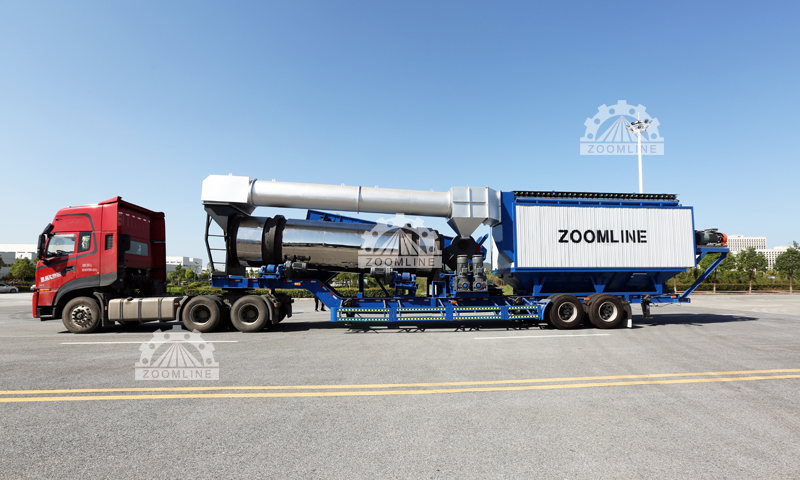
Features of Asphalt Drum Mix Plant
Compact Design
The compact structure of the drum-type mixing plant makes it easy to transport and install, making it particularly suitable for projects that require frequent relocation. Whether it’s mountain road construction or urban road renovation, it can be quickly deployed, saving time and costs.
Continuous Operation
Unlike intermittent mixing plants, drum-type mixing plants can produce asphalt mixtures continuously, significantly improving production efficiency. In large-scale road construction projects, they can meet continuous material requirements and accelerate construction progress.
User-Friendly Operation
Its intuitive interface and high degree of automation allow operators to begin work after minimal training. This reduces reliance on specialized operators while minimizing the risk of human error.
Low Initial Cost
Compared to other types of mixing plants, drum-type mixing plants require lower initial investment. For construction companies with limited budgets, they offer an economical solution, and their operational costs are also relatively low.
Durable and Reliable
Constructed with durable materials and using proven manufacturing processes, drum-type mixing plants can withstand harsh construction environments. They operate reliably over the long term with minimal downtime, ensuring smooth project execution.
Flexible mobility
Some drum-type mixing plants are equipped with mobile chassis, enabling rapid relocation. For projects with scattered construction sites and multiple work areas, the equipment can be moved as needed to improve utilization rates.
Easy maintenance
With fewer moving parts and lower wear and tear, daily maintenance is relatively simple. Combined with automated monitoring systems, potential issues can be detected promptly, further reducing maintenance costs.
Environmentally Friendly
Advanced pollution control technology and energy-efficient burners enable drum-type mixing plants to meet production requirements while minimizing environmental impact. This aligns with current trends toward green construction and supports sustainable development.
Common Issues and Troubleshooting Tips of Asphalt Drum Mix Plant
Uneven asphalt mixing
Mismatched aggregate feed rates, blocked or damaged screw conveyors, abnormal drum temperatures, and other factors can all lead to uneven asphalt mixing. These issues can be resolved by adjusting the feed rate of the cold aggregate bin, cleaning and unblocking the conveyors, and calibrating the drum temperature.
Burner malfunction
Burner nozzle scaling, unstable fuel pressure, or imbalanced air-fuel ratio can cause burner malfunction. Regularly clean the nozzles, inspect the fuel system, and check the air supply system to restore normal burner operation.
Conveyor belt slippage
Insufficient belt tension, material buildup on the drum surface, and inadequate lubrication of idlers and bearings can all cause conveyor belt slippage. Timely adjustments to tension, cleaning of the drum, and lubrication of idlers and bearings can effectively resolve this issue.
Asphalt Drum Mix Plant vs. Batch Mix Plant: Which is Right for Your Project?
Production Efficiency
Drum-type mixing plants operate continuously, making them suitable for large-scale projects; batch-type mixing plants produce in batches and are more advantageous in projects requiring frequent adjustments to the mix ratio. Selection should be based on project scale and production requirements.
Mixing Quality
Batch-type mixing plants can precisely control batch quality, ensuring good uniformity of the mix; drum-type mixing plants, when operating continuously, may experience reduced mixing quality if the mix ratio changes frequently. For projects with extremely high quality requirements, batch-type mixing plants are more suitable.
Environmental Impact
Drum-type mixing plants have relatively higher emissions due to continuous operation; batch-type mixing plants, under batch control, are easier to achieve low emissions. In regions with strict environmental protection requirements, batch-type mixing plants better meet standards.
Cost Considerations
Drum-type mixing plants have lower initial investment and operational costs; batch-type mixing plants have more complex equipment, resulting in higher investment and maintenance costs. For projects with limited budgets and a focus on efficient production, drum-type mixing plants are a better choice.
Flexibility and Adaptability
Batch-type mixing plants can flexibly adjust mix ratios, making them suitable for complex and variable projects; drum-type mixing plants are suitable for projects with stable mix ratios. Selecting the appropriate mixing plant based on project characteristics can enhance construction efficiency and economic benefits.
Conclusion
Through the introduction of the operating principles, types, components, and characteristics of asphalt drum mix plant, we believe you now have a comprehensive understanding of this asphalt plant. Whether you are a construction company selecting equipment or an industry professional seeking in-depth knowledge, the content of this article is an important reference. If you have any further questions or needs regarding asphalt drum mixers, please contact us for more detailed information and professional solutions.