An asphalt mixing plant, also known as an asphalt mixture plant, is a facility specifically designed to mix aggregates, asphalt, and other components to produce asphalt mixtures of various grades. These mixtures are widely used in the construction and maintenance of roads, parking lots, airport runways, and other paved surfaces. Through precise batching and mixing processes, asphalt mixing plants ensure the production of high-quality asphalt mixtures that meet the durability and performance requirements of various engineering projects. Whether for new infrastructure construction or the repair of existing road surfaces, asphalt mixing plants play an indispensable role in modern construction.
Asphalt mixing plants are core equipment for a wide range of paved surface construction projects, from small-scale repair projects to large-scale infrastructure development. The following is a detailed description of their applicable projects:
Road construction: Asphalt mixing plants are essential equipment for both new construction and maintenance of roads, including highways, urban main roads, rural roads, and residential area roads. Highways require high-strength asphalt mixtures to withstand the frequent passage of heavy vehicles, while urban roads may require more flexible mixture formulations to adapt to varying climatic and traffic conditions. Asphalt mixing plants ensure roads have excellent durability and smoothness by providing mixtures that meet specifications.
Airport runways and taxiways: Airport construction imposes extremely high quality requirements on asphalt mixtures, as runways and taxiways must withstand the immense pressure and friction from aircraft takeoffs and landings. Asphalt mixing plants can produce high-performance mixtures that meet stringent smoothness and strength standards, ensuring aviation safety.
Parking lot construction: Whether it’s a multi-story parking lot in a commercial center or a small parking lot in a residential area, asphalt mixing plants can provide suitable mixes. Parking lots typically require wear-resistant and easy-to-maintain surfaces, and asphalt mixes can meet these needs while providing good drainage performance.
Industrial Zone Paving: Roads and sites in industrial zones must withstand the pressure of heavy machinery and frequent transportation. The mix produced by asphalt mixing plants offers high strength and durability, making it suitable for paving needs in areas such as factories, warehouses, and logistics centers.
Infrastructure projects: Large-scale infrastructure projects, such as port terminals, railway track subgrades, and large public facilities, rely on asphalt mixing plants for a stable supply of mix. These projects typically require large volumes of high-quality mix, making continuous drum or continuous mixing plants the ideal choice.
Road repair and maintenance: Asphalt mixing plants are not only used for new construction projects but are also widely applied in the repair and maintenance of existing roads. For example, filling road cracks, repairing potholes, or renovating aged road surfaces, mixing plants can quickly produce the appropriate amount of mix to extend the service life of the road surface.
Special Paving Projects: Some special application scenarios, such as bicycle paths, sidewalks, or sports field surfaces, can also utilize asphalt mixing plants to produce customized mixes. These projects may require specific colors, textures, or environmental performance, and the flexibility of mobile mixing plants makes them particularly suitable.
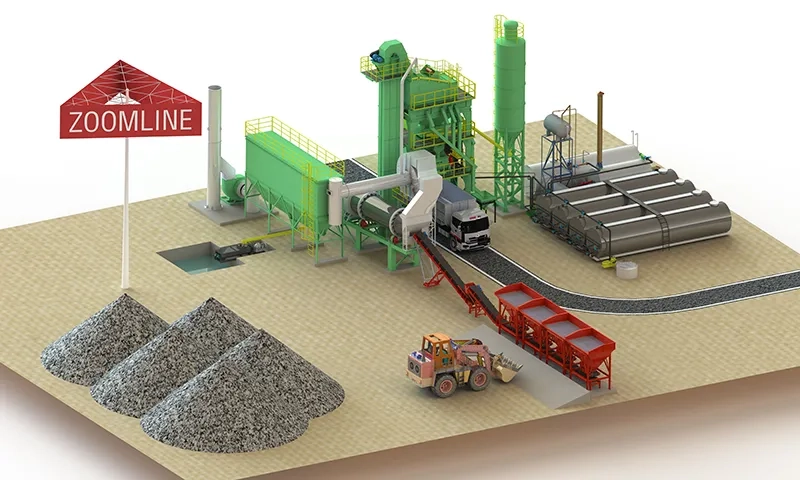
Asphalt mixing plants are primarily categorized into stationary asphalt mixing plants, mobile asphalt mixing plants, continuous asphalt mixing plants, and drum asphalt mixing plants based on production methods and mobility. Each type has distinct characteristics in terms of production processes, applicable projects, and advantages.
Stationary asphalt mixing plants: Suitable for long-term use in medium to large-scale projects such as highways, airport runways, and port terminals. They heat cold aggregates, add asphalt and fillers, and mix them in batch mixers to ensure high-precision quality control. They produce various types of mixes, including hot mix, warm mix, and cold mix, to meet the needs of urban roads, industrial zone paving, and other applications. Their advantages include high production capacity, strict quality control, and long-term stability.
Mobile asphalt mixing plants: Featuring a modular design for easy transportation and rapid installation, these are suitable for small to medium-sized projects or those requiring frequent relocation, such as rural road construction, road repairs, and temporary parking lot paving. Their mobile process supports flexible formula adjustments, and their rapid deployment capability meets emergency repair or remote construction needs, making them suitable for special paving projects like bike paths and sidewalks.
Continuous asphalt mixing plants: These plants use the parallel flow principle to continuously heat and mix aggregates and asphalt, making them suitable for high-volume projects such as highways and airport runways. The parallel flow design optimizes temperature control, and bag filters reduce emissions. These plants operate stably and efficiently, reducing energy consumption and operating costs.
Drum mix asphalt mixing plant: This plant uses a single drum to continuously heat, dry, and mix aggregates, making it suitable for large-scale projects such as highway and airport construction. Its simple design requires minimal labor for operation and maintenance, has low energy consumption, and is suitable for construction in remote areas, with stable production capacity to reduce costs.
Asphalt mixing plant components vary by type, but stationary and continuous plants share some common components.
Stationary/Mobile asphalt mixing plant components
The components of a stationary asphalt mixing plant are designed for precise batching and high-quality production, including a cold aggregate feed hopper for storing aggregates of different particle sizes and conveying them via a conveyor belt to ensure a stable material supply; a vibrating screen to remove oversized aggregates, prevent equipment blockages, and ensure uniform mix quality; a drying drum equipped with a burner to heat and dry aggregates to remove moisture and optimize asphalt adhesion; a bucket elevator to transport hot aggregate to the tower unit, with a covered design to minimize heat and dust loss; the tower unit includes a vibrating screen (to classify hot aggregate by particle size), a hot aggregate silo (to store classified aggregate), and a mixing unit (using a double-shaft jacket-type mixer with mixing arms and blades to ensure uniform mixing of aggregate, asphalt, and filler); The asphalt tank heats and stores asphalt, with precise metering via a weighing hopper; the filler silo stores fillers such as lime powder or cement, which are added to the mixing unit in proportion to enhance the performance of the mixture; bag filters capture dust generated during production, reducing emissions to meet environmental standards; the control panel centrally monitors and adjusts aggregate ratios, asphalt temperature, and mixing time to ensure the precision and stability of the production process.
Components of Continuous/Drum-Type Asphalt Mixing Plants
The component design of continuous and drum-type asphalt mixing plants emphasizes efficient continuous production, including a cold aggregate feed hopper for分类 storage of aggregates and conveying them via a conveyor belt to the primary vibrating screen; The primary vibrating screen removes oversized aggregates to ensure uniform aggregate quality entering the drum; Conveyors transport aggregates to the drying and mixing drum, featuring anti-slip design to ensure stable transportation; The drying and mixing drum is the core component, with the front section heated and dried by high-efficiency burners, and the rear section mixing hot aggregates with asphalt and fillers, optimized for heat transfer and mixing efficiency; The pollution control unit uses bag filters or wet dust collectors to capture dust and particulates, ensuring the production process complies with environmental protection requirements; The asphalt tank heats the asphalt and injects it into the drum via pipelines for mixing with aggregate and filler; the filler silo delivers filler into the drum via pneumatic or mechanical systems; the control panel monitors and adjusts burner temperature, aggregate flow rate, and asphalt ratio in real-time to ensure production continuity and mix quality.
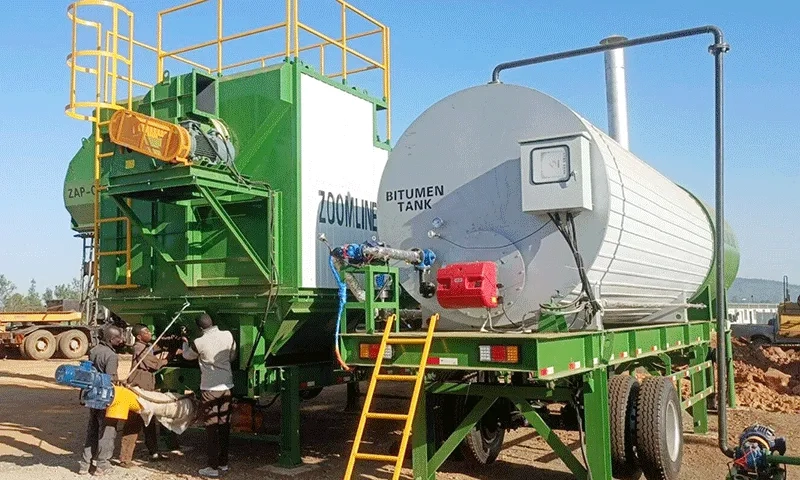
Asphalt plants boost construction efficiency
Modern asphalt mixing plants have achieved a significant leap in construction efficiency through technological upgrades. The new generation of mixing plants has broken through traditional capacity limitations in design, enabling larger batch sizes — for example, mobile mixing plants have a single-batch production capacity over 30% higher than traditional equipment, while continuous mixing plants maintain a steady hourly throughput of hundreds of tons. This means they can quickly meet daily asphalt demands of thousands of tons in large-scale projects like highways, fundamentally shortening material supply cycles. Advanced control systems are the core support for efficiency improvements. Through intelligent sensors, they monitor key parameters such as aggregate moisture content and asphalt temperature in real time, and combine automated algorithms to dynamically adjust mixing time and heating intensity. This ensures the accuracy of mixture composition ratios (such as aggregate gradation and asphalt usage) and temperature (hot-mixed asphalt is typically controlled between 160-180°C), reducing rework delays caused by quality fluctuations. Additionally, modern mixing plants have significantly improved compatibility with sustainable materials. For example, the blending ratio of recycled asphalt pavement (RAP) can be flexibly adjusted according to project requirements (up to over 50%), which not only reduces the procurement and transportation frequency of virgin aggregates but also minimizes time spent on waste disposal through material recycling. Some high-end equipment is also equipped with remote monitoring systems, allowing operators to view real-time operational data for each component (such as dryer drum speed and burner power) from the control room. In the event of issues like hopper blockages or temperature anomalies, operators can immediately intervene remotely or dispatch personnel to address the issue, reducing downtime to less than one-third of traditional modes and significantly accelerating overall construction progress.
Asphalt plants reduce labor & material costs
Having an in-house asphalt mixing plant enables precise cost control from the source. In terms of material costs, the “on-demand production” model has completely transformed the traditional passive reliance on external suppliers — — Contractors can precisely set production plans based on daily construction volumes. For example, if a road repair project requires 50 tons of specific-grade asphalt mixture, the plant can produce exactly that amount, avoiding the redundant procurement of “ordering 20% extra to ensure supply” when purchasing externally, reducing material waste by 10%-15% annually. Additionally, the batching plant’s precise control capabilities enhance material efficiency: an automatic weighing system regulates the ratio of aggregates, asphalt, and fillers (with an error margin of ±1% or less), and adjusts the formula in real-time based on environmental temperature (e.g., reducing asphalt usage during summer heatwaves) and road load requirements (e.g., increasing coarse aggregate proportions for heavy-duty roads), ensuring quality while preventing “over-use of materials.” In terms of labor costs, the automation level of modern mixing plants significantly reduces manpower requirements: the traditional manual material loading and temperature measurement process requires 5-6 people to collaborate, while the current fully automated mixing plant only needs 2-3 people to monitor and assist with operations; continuous mixing plants further reduce manual intervention in material transfer processes through an integrated production workflow, saving over 30% in annual labor costs. Additionally, having an in-house mixing plant eliminates the risk of reliance on external suppliers — — when asphalt prices rise by 30% due to seasonal fluctuations or suppliers cannot deliver on time due to order saturation, construction companies can independently adjust production to avoid delays caused by material shortages (each day of delay may incur tens of thousands of dollars in machinery rental and idle labor costs). This flexibility translates into significant cost and competitive advantages in scenarios with strict schedule requirements, such as large-scale projects.
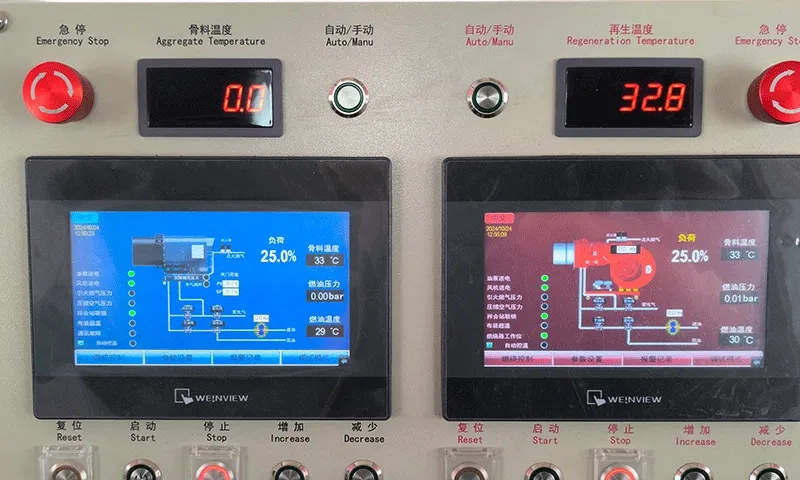
Asphalt plants make high-quality asphalt mixes
High-quality asphalt mixtures are the core of ensuring pavement durability, and the mixing plant is the key link in quality control. Its core advantage lies in precise control over the entire production process: During the raw material stage, vibrating screens can strictly remove oversized particles (such as stones larger than 31.5 mm) from the aggregate, ensuring the aggregate gradation meets design requirements; During the heating stage, the temperature control system of the drying drum maintains the aggregate heating temperature at the set value (with an error margin of no more than ±5°C), preventing asphalt aging caused by localized overheating or reduced bonding effectiveness due to insufficient temperature; during the mixing stage, the blade design of the twin-shaft mixer ensures that aggregates and asphalt are fully coated within 15–30 seconds, eliminating any uncoated aggregates. Different types of mixing plants can also optimize quality according to project requirements: mobile mixing plants can conduct sampling tests on each batch of mix (e.g., Marshall stability tests) to ensure batch quality compliance before shipment; continuous mixing plants use online monitoring systems (e.g., infrared temperature sensors, density sensors) to provide real-time feedback on mix status and adjust production parameters promptly. This stable quality control directly enhances pavement performance — pavements constructed using mix produced by mixing plants exhibit over 20% improved resistance to rutting and low-temperature cracking, with a service life extended by 3–5 years, thereby indirectly reducing post-construction maintenance costs.
Significant Environmental Advantages: Asphalt mixing plants offer significant environmental advantages over other engineering projects (such as cement production or mining) by significantly reducing pollution through advanced technology and strict environmental protection measures. During asphalt production, the primary emissions include volatile organic compounds (VOCs), particulate matter (PM), and polycyclic aromatic hydrocarbons (PAHs). However, by adopting warm mix asphalt (WMA) technology, the mixing temperature can be reduced by 20–40°C, resulting in approximately a 30% reduction in energy consumption and greenhouse gas emissions compared to traditional hot mix asphalt (HMA). According to research, the mixing stage accounts for 54% of greenhouse gas emissions in asphalt mixture production. Optimizing burner design and using biofuels (such as bio-based binders) can further reduce emissions, far below the approximately 0.9 tons of CO2 per ton emitted in cement production. Compared to the high-temperature calcination process in cement plants or large-scale land destruction in mining activities, asphalt mixing plants effectively capture PM and VOCs through efficient pollution control systems such as bag filters and wet dust collectors, resulting in emissions significantly lower than other industries. For example, bag filters can capture over 99% of fine particulate matter, ensuring emissions comply with strict environmental standards.
Resource conservation and recycling: Asphalt mixing plants significantly reduce the demand for virgin resources by extensively using recycled asphalt pavement (RAP) and construction and demolition waste (C&DW), demonstrating a stronger circular economy advantage than other engineering projects. RAP is material recovered from old road surfaces, which can replace up to 50% of virgin aggregates and asphalt. Compared to mining new materials, this reduces land disturbance, energy consumption, and waste accumulation. EU research indicates that asphalt pavements using RAP and C&DW can reduce environmental costs by 32% while alleviating landfill pressure. In contrast, the use of recycled materials in cement production is relatively low, and the production process relies more heavily on non-renewable resources such as limestone. Additionally, asphalt pavement construction is faster, reducing mechanical operation time and dust emissions during construction, outperforming the high-pollution and lengthy construction process of concrete pavement laying. The recyclability of asphalt pavement also allows it to re-enter the production cycle at the end of its lifecycle, whereas concrete pavement, once demolished, often becomes difficult-to-handle construction waste.
Reducing urban environmental impact: Pavements produced by asphalt mixing plants have unique advantages over traditional concrete pavements in reducing urban environmental impact. Asphalt pavements can improve drainage performance through optimized design (e.g., porous asphalt), reducing the risk of urban flooding, while the impermeability of concrete pavements often leads to rainwater accumulation, exacerbating urban flooding. Additionally, the dark surface of asphalt pavements can reduce solar radiation absorption by adding light-colored coatings or using recycled materials, thereby mitigating the urban heat island effect (UHI), lowering urban temperatures, and reducing air conditioning energy consumption. In contrast, while the high reflectivity of concrete pavements helps reduce the heat island effect, the high energy consumption and emissions during their production and construction processes offset this advantage. Asphalt mixing plants further reduce VOCs and nitrogen oxides (NOx) emissions during production through warm-mix technology and low-emission equipment (such as low-NOx burners), protecting air quality and resident health in surrounding communities, outperforming the severe pollution issues commonly associated with quarries or cement plants.
Economic benefits combined with environmental protection: Asphalt mixing plants demonstrate significant advantages in terms of economic efficiency through efficient production and resource reuse, while maintaining low environmental impact. On-demand production reduces material waste and transportation emissions, and the use of RAP and C&DW significantly lowers raw material costs. EU research shows that the construction cost of asphalt pavements using these materials can be reduced by 32%. In contrast, cement production relies on energy-intensive clinker calcination, resulting in higher costs and greater vulnerability to raw material price fluctuations. Asphalt mixing plants support projects such as roads, airport runways, and parking lots, promoting employment and local economic development while reducing long-term operational costs through environmental technologies. In the US, environmental compliance costs for manufacturing average 0.4% of revenue, while the asphalt industry keeps costs at a lower level through clean technologies (such as warm mix and RAP), far below the cement industry’s 1%. The combination of these economic benefits and environmental measures makes asphalt mixing plants more sustainable and competitive than other engineering projects in infrastructure construction.
U.S. Relevant Laws, Regulations, and Cases
In the United States, asphalt mixing plants are subject to strict environmental regulations to ensure their emissions are far below those of other engineering projects. The U.S. Environmental Protection Agency (EPA)’s National Emission Standards for Hazardous Air Pollutants (NESHAP) require asphalt mixing plants to control harmful air pollutants (HAPs) such as VOCs and PAHs. By installing high-efficiency bag filters and wet scrubbers, particulate matter emissions are significantly lower than those from cement plants or quarries. The New Source Performance Standards (NSPS) establish strict particulate matter and VOC emission limits for new or modified hot-mix asphalt facilities, encouraging companies to adopt low-emission technologies such as low-nitrogen burners to significantly reduce environmental impact. In 2024, the EPA fined All American Asphalt Company in California $53,115 for failing to accurately report polycyclic aromatic hydrocarbon (PAH) emissions between 2018 and 2021. The company subsequently upgraded its pollution control equipment, bringing emissions levels far below cement industry standards, highlighting the environmental advantages of asphalt mixing plants. The Emergency Planning and Community Right-to-Know Act (EPCRA) requires mixing plants to report releases of toxic chemicals, ensuring communities are informed about environmental risks. Compared to the high pollution emissions of the mining industry, the transparency and compliance of asphalt mixing plants further reduce their impact on the surrounding environment.
EU-related laws, regulations, and cases: The EU has enacted a series of regulations to drive asphalt mixing plants toward achieving lower environmental impacts than other engineering projects. The EU Emissions Trading System (EU ETS) incentivizes the asphalt industry to adopt warm-mix technology and RAP through carbon emission quotas, reducing material costs and emissions by approximately 5-8%. Compared to the cement industry’s high carbon footprint, asphalt mixing plants’ carbon emissions are easier to control. The Waste Framework Directive mandates the reuse of old pavement materials and prohibits the disposal of recyclable asphalt waste in landfills. Over 90% of asphalt pavements in the EU utilize RAP, with recycling rates far exceeding those of the concrete industry, thereby reducing resource consumption and environmental damage. The Environmental Impact Assessment Directive (EIA Directive) mandates environmental impact assessments for large asphalt mixing plant projects to minimize emissions and heat island effects on air, water, and soil. Public participation further ensures environmental transparency. The European Green Deal aims for climate neutrality by 2050, with its circular economy action plan promoting the use of bio-based binders and low-carbon technologies in the asphalt industry. The EU-funded APSE project demonstrates that using bio-based binders and RAP can reduce asphalt usage by 10% and VOC emissions by 15%, with environmental costs reduced by 3-4 euros per square meter, proving that asphalt mixing plants offer greater environmental and economic advantages compared to cement production and mining.
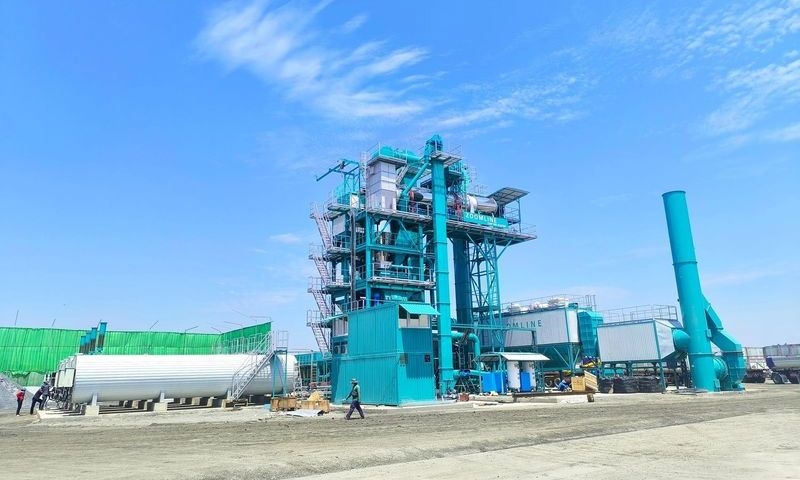
Conclusion
Asphalt mixing plants provide critical support for the construction of roads, airport runways, parking lots, and other paved surfaces by producing high-quality asphalt mixtures. Their diverse types, including stationary, mobile, drum, and continuous mixing plants, meet the needs of projects ranging from small to large-scale. Modern mixing plants enhance construction efficiency and product quality through efficient production, energy-saving designs, and environmental measures, while significantly reducing economic and environmental costs. As a core facility in modern infrastructure construction, asphalt mixing plants will continue to play a vital role in promoting sustainable development and high-performance pavement construction.