In modern asphalt production, the control system plays the role of the ‘brain’, directly influencing the quality of asphalt mixtures, production efficiency, and cost control. Whether it is highway construction, airport runways, or water conservancy projects, the stable operation of hot mix asphalt mixing plants cannot be separated from an efficient control system. This article will provide an in-depth analysis of the definition, core components, functional classification, and optimization methods of hot-mix asphalt batching plant control systems, helping industry professionals gain a comprehensive understanding of this critical equipment.
Introduction of Control System of Hot Mix Asphalt Plant
The hot-mix asphalt mixing plant control system is a core component of modern asphalt production facilities. By integrating advanced technologies, it achieves precise management of the entire process of automatically mixing aggregates, asphalt binder, and additives according to pre-set formulas.
Its core advantages include:
Optimizing the mixing process, shortening production cycles, and enhancing overall production capacity;
Ensuring consistent final product quality to meet engineering technical specifications;
Simplifying operational processes and reducing labour costs through an intuitive human-machine interface.
Functionally, the system offers production data management, real-time parameter monitoring, and equipment operational status display capabilities. It is user-friendly and highly stable, making it an indispensable technical support system for large-scale infrastructure projects.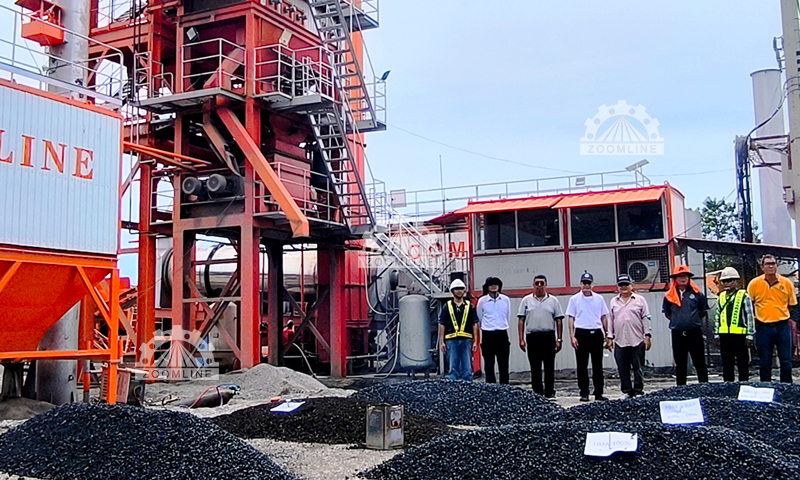
Key Components of control system of hot mix asphalt plant
A complete hot mix asphalt batching plant control system is composed of multiple key components that work together. Each component performs specific functions to ensure the smooth operation of the production process.
Computer Control Framework
As the core of human-machine interaction, the computer control system is responsible for:
Controlling the start and stop of equipment;
Real-time monitoring of equipment operating status and timely feedback of abnormalities;
Formula management, production data storage, and query;
Generating production reports and supporting print output.
Hardware configuration includes a computer host, monitor, UPS uninterruptible power supply, printer, and serial communication card, ensuring the stability of data processing and storage.
Robust Electrical Control Cabinet
Featuring a standard cabinet design with strong anti-interference capabilities, the interior integrates:
Electrical components such as air circuit breakers, contactors, and thermal relays;
Variable frequency drives, transformers, and terminal blocks;
Cabinet doors equipped with temperature controllers, switches, and other operational components.
Based on user requirements, imported, joint-venture, or domestic brand components can be configured. The circuit design complies with international electrical standards, with a neat layout for easy maintenance.
Operator Station
The operator station serves as the direct interface between the operator and the system, including:
Embedded computers, displays, and control panels;
Operator buttons protrude from the work surface, with etched markings on the panel surface for intuitive and durable use;
Integrated printers support on-site data printing.
Core Functions of the Hot Mix Asphalt Plant Control System
The control system achieves precise control over the entire asphalt production process through the coordination of hardware and software, primarily manifested in the following five key functions:
Material Proportioning Control
Based on pre-set formulas, the system uses load cells and flow meters to monitor the input quantities of aggregates, asphalt, and additives in real time, dynamically adjusting feed rates to ensure that material proportioning errors are kept within a minimal range, thereby providing a foundational guarantee for pavement strength and durability.
Temperature Regulation Function
Asphalt production requires strict temperature control (typically 150–190°C). The system monitors burner performance, drying drum temperature, and asphalt heating units to automatically adjust fuel supply and air intake, preventing overheating that could cause binder degradation or insufficient temperature leading to uneven mixing.
Production Process Automation
Coordinate the operational rhythms of conveyors, vibrating screens, mixers, and other equipment to achieve:
Automatic weighing and conveying of aggregates;
Timed and metered asphalt injection;
Precise control of mixing time.
By pre-programming production plans, manual intervention can be reduced, and equipment utilization improved.
Data Recording and Report Generation
Real-time collection of production data (such as mix ratios, temperature, output, etc.), automatic storage, and generation of quality traceability reports to meet engineering acceptance and regulatory compliance requirements, while providing data support for production optimization.
Fault detection and alarms
Sensors throughout the equipment provide real-time feedback on operational status. When issues such as burner malfunctions, temperature anomalies, or material blockages occur, the system immediately triggers audio-visual alarms and displays the fault location and cause on the interface, assisting operators in quickly identifying and resolving issues to minimize downtime.
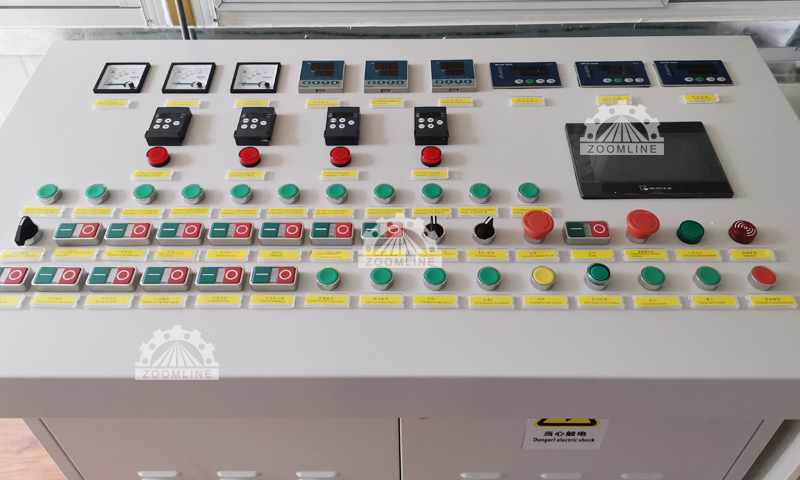
Types of Control Systems in HMA Plants
Based on the degree of automation, control systems can be divided into three categories, suitable for different production scale requirements:
Type | Features | Application Scenarios |
Manual Control System | Relies on operators to manually adjust valves and switches, and monitor parameters visually | Small-scale batching plants, projects with low output and low quality requirements |
Semi-automatic Control System | Automatically performs core processes such as weighing and temperature control, but requires manual start/stop of production | Medium-sized mixing plants balancing cost and production stability |
Fully Automatic Control System | Computer-controlled fully automatic operation based on pre-set formulas, supporting remote monitoring and adaptive adjustments | Large-scale mixing plants for high-standard projects such as highways and airports |
How Does a Control System Work in an HMA Plant?
From raw material input to finished product output, the control system manages the entire process according to the following steps:
System Initialisation and Calibration
After startup, the system automatically detects the status of the equipment and calibrates components such as weighing sensors and thermocouples to ensure measurement accuracy.
Raw Material Selection and Feeding Control
The operator selects the formula via the human-machine interface, and the system starts the cold aggregate feeder. Variable frequency speed control is used to regulate the proportion of different aggregate specifications being conveyed.
Drying and Heating
After the aggregate enters the drum dryer, the system adjusts the burner power based on real-time temperature feedback to heat the aggregate to the target temperature (150–180°C) and remove moisture.
Dust Removal and Airflow Monitoring
The control system regulates the induced draft fan of the baghouse dust collector, monitors pressure differential to ensure dust removal efficiency, and can reintroduce recovered dust into the mixture at a specified ratio.
Hot Aggregate Screening and Storage
After hot aggregates are screened by a vibrating screen, the control system uses level sensors to control the discharge gates, storing aggregates of different specifications in corresponding hot aggregate silos to prevent overfilling or emptying of silos.
Weighing and Mixing
Aggregates, fillers, and asphalt are weighed according to the formula, loaded into the mixer, and mixed for a set time to ensure uniformity of the mixture.
Product Unloading and Storage
After mixing is complete, the system coordinates the unloading rhythm, sending the hot-mixed asphalt into the finished product silo or directly into transport vehicles, while simultaneously recording the batch data.
Safety and Automation Assistance
Supports remote access, historical data queries, and fault diagnosis, equipped with emergency shutdown, over-temperature protection, and other safety mechanisms to ensure continuous production.
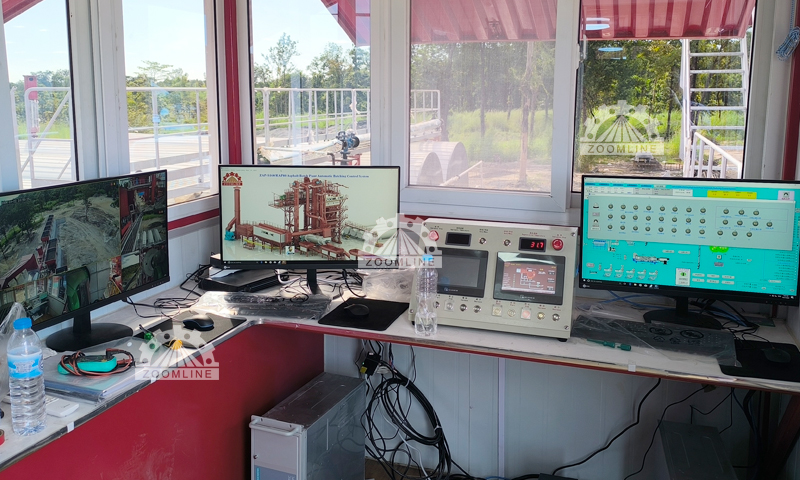
Benefits of Advanced Control Systems for HMA Plants
Compared to traditional manual operations, the advanced control system offers multi-dimensional improvements for the batching plant:
Enhanced Production Efficiency
Automated processes reduce manual operation time and optimise equipment coordination, increasing single-unit daily output by 10–20% and shortening project delivery cycles.
Ensuring Product Quality Stability
By precisely controlling mix ratios and temperature, fluctuations in mix material parameters are minimised, reducing defective product rates and minimising rework costs.
Real-Time Monitoring and Decision Support
Operators can monitor key data such as fuel consumption, equipment load, and raw material inventory in real time via a dashboard, enabling timely adjustments to production strategies.
Simplify compliance management
Automatically generated production reports include complete quality parameters, making it easy to handle owner inspections and industry regulations, and avoiding delays in acceptance due to incomplete documentation.
Reduce operational costs
Precise material mixing reduces raw material waste and lowers asphalt and aggregate loss;
Optimised combustion control saves approximately 5–8% in fuel consumption;
Remote diagnostic functions reduce on-site maintenance visits and extend equipment lifespan.
5 Ways to Improve Asphalt Plant Control
To maximize the efficiency of the control system, optimization can be achieved through the following measures:
Upgrade to Support New Technologies
Outdated systems may not be compatible with the addition of new materials such as recycled asphalt pavement (RAP) and anti-stripping agents. Timely upgrades can meet the needs of diverse formulations.
Improve the batching control algorithm
Optimise the batching adjustment logic using real-time feedback data to reduce initial production debugging time and ensure the first batch meets standards.
Reduce waste from frequent starts and stops
Plan production schedules reasonably and use the control system to precisely manage material silo inventory to reduce waste caused by frequent starts and stops (some mixing plants waste over 100 tonnes per week).
Regularly calibrate critical components
Establish a sensor calibration schedule (recommended quarterly), to prevent quality fluctuations caused by weighing errors, with automatic reminders via system settings.
Strengthen abnormal alarm mechanisms
Add alarm functions for critical points such as feeder blockages, low asphalt tank liquid levels, and excessive pressure differentials in baghouse dust collectors, to alleviate monitoring pressure on operators.
Conclusion
The control system of a hot-mix asphalt batching plant is the core equipment that balances production efficiency and product quality, and its technical level directly determines the market competitiveness of the batching plant. With the development of intelligent technology, future control systems will place greater emphasis on data analysis, energy optimization, and remote collaboration, providing stronger support for green transportation construction.
For batching plant operators, selecting a suitable control system and continuously optimizing its performance not only reduces operational costs but also enables them to gain a competitive edge in high-standard engineering markets.