In today’s world, where the concept of sustainable development is gaining widespread acceptance, the road construction industry is actively exploring environmentally friendly development pathways. Asphalt pavements, a crucial component of highway construction, generate a significant amount of old pavement materials. If these materials are not utilized properly, they not only result in substantial resource waste but also impose a heavy environmental burden. The emergence of asphalt recycling equipment has provided an effective solution to this issue.
This article will comprehensively analyze the workflow of asphalt recycling equipment, covering its basic concepts, structural composition, specific operational steps, advantages, challenges, and future trends, to highlight the important role of asphalt recycling equipment in the sustainable development of road construction.
What Is Asphalt Recycling Equipment
Asphalt recycling equipment is an innovative piece of machinery in the modern road construction field. It can scientifically mix recycled asphalt pavement materials (RAP) with virgin aggregates and fillers to produce new asphalt mixtures that meet quality standards. This equipment offers significant technical and economic advantages, not only significantly reducing fuel and raw material consumption but also effectively minimizing pollutant emissions and solid waste generation during construction. It has become a key technological pillar for promoting the greening and sustainable development of asphalt pavements.
Structure of Asphalt Recycling Equipment
The various systems of asphalt recycling equipment operate in precise coordination to form an efficient integrated system:
• Crushing and Screening System
Utilizing multi-stage crushing and precise screening technology, this system processes old asphalt pavement materials (RAP) into particles of the required size for recycling, providing a high-quality raw material foundation for subsequent processes.
• Thermal Recycling System
Equipped with intelligent temperature control and dynamic mixing devices, this system precisely regulates heating curves and mixing durations to achieve deep softening and performance restoration of aged asphalt, ensuring stable recycling quality.
• Additive Supply System
Utilizing high-precision metering and closed-loop control systems, additives are automatically blended according to raw material characteristics, ensuring that the physical and mechanical properties of the recycled asphalt mixture meet standards from the source.
• Flue Gas Treatment System
Integrating multi-stage purification modules such as dust removal, desulfurization, and odor removal, it effectively removes pollutants such as PM2.5 and volatile organic compounds generated during the recycling process, adhering to green production principles and ensuring a safe working environment.
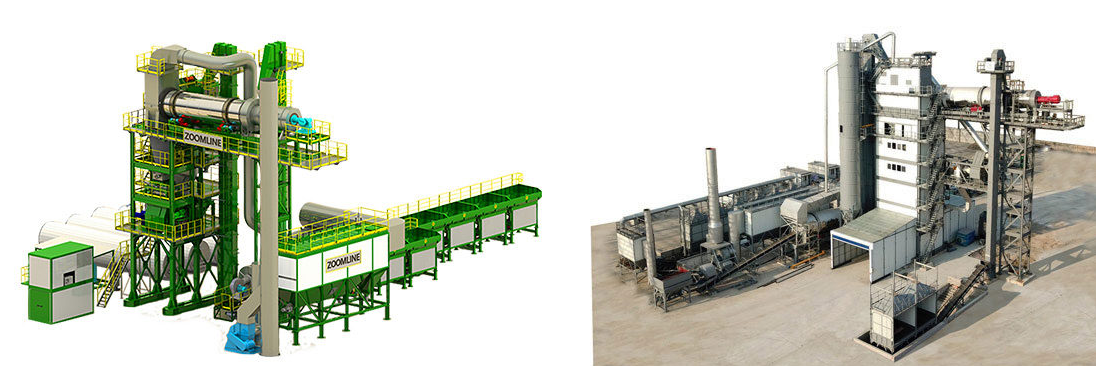
The Working Process of Asphalt Recycling Equipment
- Milling: Most recycled asphalt pavement (RAP) materials are obtained through the milling process of existing road surfaces. A milling machine is used to grind the old asphalt pavement to a specific depth. Most projects only remove a 2-inch-thick wearing course, while large-scale projects may mill 8–10 inches of material. The RAP materials are then transported to a recycling facility or plant.
- Crushing:The newly acquired materials are crushed into particles of different sizes, typically starting with the largest pieces collected from the site. Crushing equipment includes jaw crushers (for larger pieces) and impact crushers (for smaller aggregate particles), making the material easier to handle.
- Screening and Fractionating:RAP is screened to remove non-asphalt materials and other impurities while classifying different RAP particles by size (e.g., coarse and fine). This process is typically performed using a series of vibrating screens, which help to better organize RAP particles by size. Reducing dust in the RAP is also important during material grading.
- Homogenization:Homogenize and grade each RAP fraction to ensure consistent particle size throughout the pile. This aids in quality control during mix design to ensure compliance with specifications.
- Storage:When storing RAP for future use, it should be handled with the same care as virgin materials. Storing RAP in silos, sheds, or covered with waterproof tarps helps reduce moisture content, maintaining quality and minimizing the need for costly and time-consuming heating of the aggregate.
- Characterizing: Mix design engineers analyze RAP samples to determine characteristics such as gradation, asphalt content, and asphalt grade. At this stage, the asphalt content in RAP is estimated, and a decision is made on whether to add virgin aggregate or asphalt to the mixture.
- Rejuvenating:Since RAP binder contains aged asphalt, its chemical composition changes over time. Therefore, an effective asphalt regenerator should be added during mix design. Asphalt rejuvenators restore the functional properties of aged asphalt, contributing to the creation of durable pavements.
- Formulating:: Technicians determine the quantities of RAP, virgin materials, and rejuvenators based on established mix specifications to optimize mix performance. In many cases, balanced mix design helps meet the grade and quality requirements set by transportation authorities.
- Production: After determining specifications and mix design, managers can send RAP mixture to the mixing plant for production, with RAP dosage depending on the type of mixing plant. Although operations vary across different mixing plants, controlling RAP moisture content plays a crucial role in the overall quality and performance of the mixture. Advances in hot-mix plants and equipment have significantly facilitated the production of high-RAP-content, high-quality, and stable-performance mixtures.
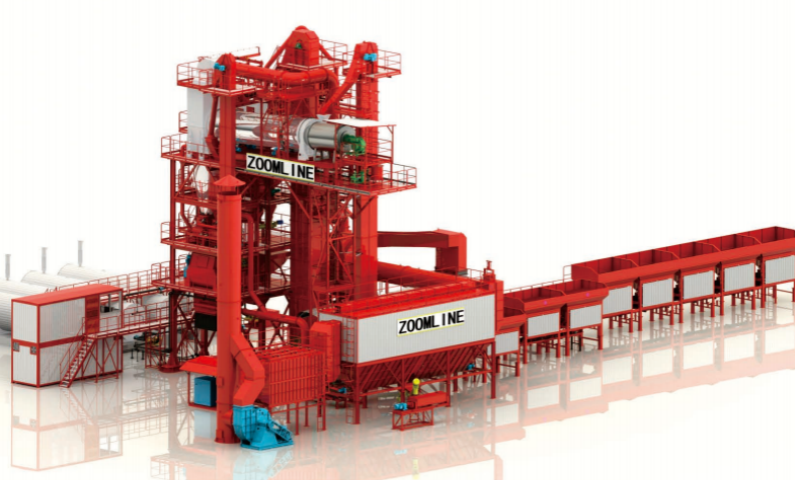
Achieve Maximum Addition of Recycled Asphalt Material
The optimal approach is to restore waste asphalt materials to their original composition. The regeneration of waste asphalt should be determined at the mixing plant based on the requirements for recycled asphalt material addition specified in the finished product gradation curve. For this purpose, we recommend a fully regenerative high-temperature gas generator regeneration addition system based on the counterflow principle, which can increase the addition of recycled materials to 90% + X.
How does this work specifically?
The recycled material is heated using a counterflow method, where the material flows toward the heat source within the drum. This ensures the material reaches higher temperatures while reducing exhaust gas temperatures. The 160°C outlet temperature aligns with the processing temperature of subsequent asphalt concrete, while the exhaust gas temperature is slightly above the dew point, approximately 100°C. A significant advantage for newly added aggregates is that excessive heating is unnecessary, significantly reducing energy consumption.
A high-temperature gas generator must be used during production because direct heating of waste asphalt materials would damage the recycled materials, rendering them unusable. The burner, high-temperature gas generator, drying drum, separation hood, and air circulation system work together to achieve optimal results.
What other resources can be saved when mixing asphalt materials?
Generally, asphalt production materials should be stored in a dry location to protect the material piles and feed conveyors from rain.
When recycling old asphalt materials, the moisture content of the material should be reduced as much as possible during milling. For every 1% reduction in the moisture content of raw materials, fuel consumption per ton of asphalt mixture in subsequent processing at the asphalt mixing plant decreases by 1 liter.
Types of Asphalt Recycling Equipment
Hot Mix Asphalt (Central Processing Facility)
Recycled hot-mix asphalt is typically produced at a central RAP processing plant, which is usually equipped with crushers, screening equipment, conveyors, and stackers for producing and storing finished granular RAP products that meet the required gradation. This product is then incorporated into hot-mix asphalt paving mixtures as an aggregate substitute. Both batch plants and drum plants can incorporate RAP into hot mix asphalt.
Hot Mix Asphalt (In-Place Recycling)
In-place hot recycling is a repaving process that can be performed in single or multiple passes using specialized heating, crushing, recycling, paving, and compaction equipment. No pre-processing is required prior to actual recycling operations.
Cold Mix Asphalt (Central Processing Facility)
Cold-mixed recycling has similar processing requirements for RAP as hot-mix recycling, with the difference being that graded RAP products are incorporated into cold-mixed asphalt pavement mixtures as aggregate substitutes.
Cold Mix Asphalt (In-Place Recycling)
The in-place cold recycling process involves specialized equipment or processing units that mill the existing pavement surface to a depth of 150 millimeters (6 inches) in a single pass, process it, mix it with asphalt emulsion (or foamed asphalt), and then pave and compact it. No pre-treatment is required before actual recycling operations.
Advantages of Asphalt Recycling Equipment
- Cost savings: Using recycled asphalt reduces spending on virgin asphalt materials. According to the National Asphalt Paving Association (NAPA), using recycled pavement in infrastructure projects saves taxpayers nearly $2 billion annually. In commercial and residential improvement projects, using recycled asphalt pavement and tiles is a more economical choice than producing and transporting virgin asphalt.
- Environmentally friendly:Increasing the use of recycled asphalt products (RAP) plays a key role in significantly reducing greenhouse gas emissions. Using RAP reduces the demand for new oil in the asphalt production process. Recycled asphalt is 100% recyclable and renewable, making it extremely durable.
- Reduced landfill waste:Pavement and other RAP contain a mixture of recycled materials, including glass, rubber, steel, and cement. The resulting mixture reduces the presence of these non-biodegradable materials and asphalt in landfills. According to the NAPA Sustainability Report, the recycling process saves approximately 60 million cubic yards of landfill space annually.
- Protect natural resources:Asphalt mixtures incorporate other limited natural materials for pavement construction. By using RAP, non-renewable natural resources such as stones, sand, and gravel can be conserved. As the demand for virgin asphalt production decreases, relevant agencies can reduce their reliance on other non-renewable resources like petroleum.
- Enhance durability and lifespan:When new asphalt is mixed with recycled materials, it forms a thicker, more durable product. The stiffness of recycled asphalt pavements is improved, reducing the likelihood of cracking. This means reduced future maintenance and repair needs for asphalt.
- Versatile applications: The use of recycled asphalt materials is not limited to road paving. Products containing RAP include: residential and commercial roofs and tiles, residential and commercial building exteriors, landscaping needs (pavers, retaining walls, etc.), parking lots, and driveways.
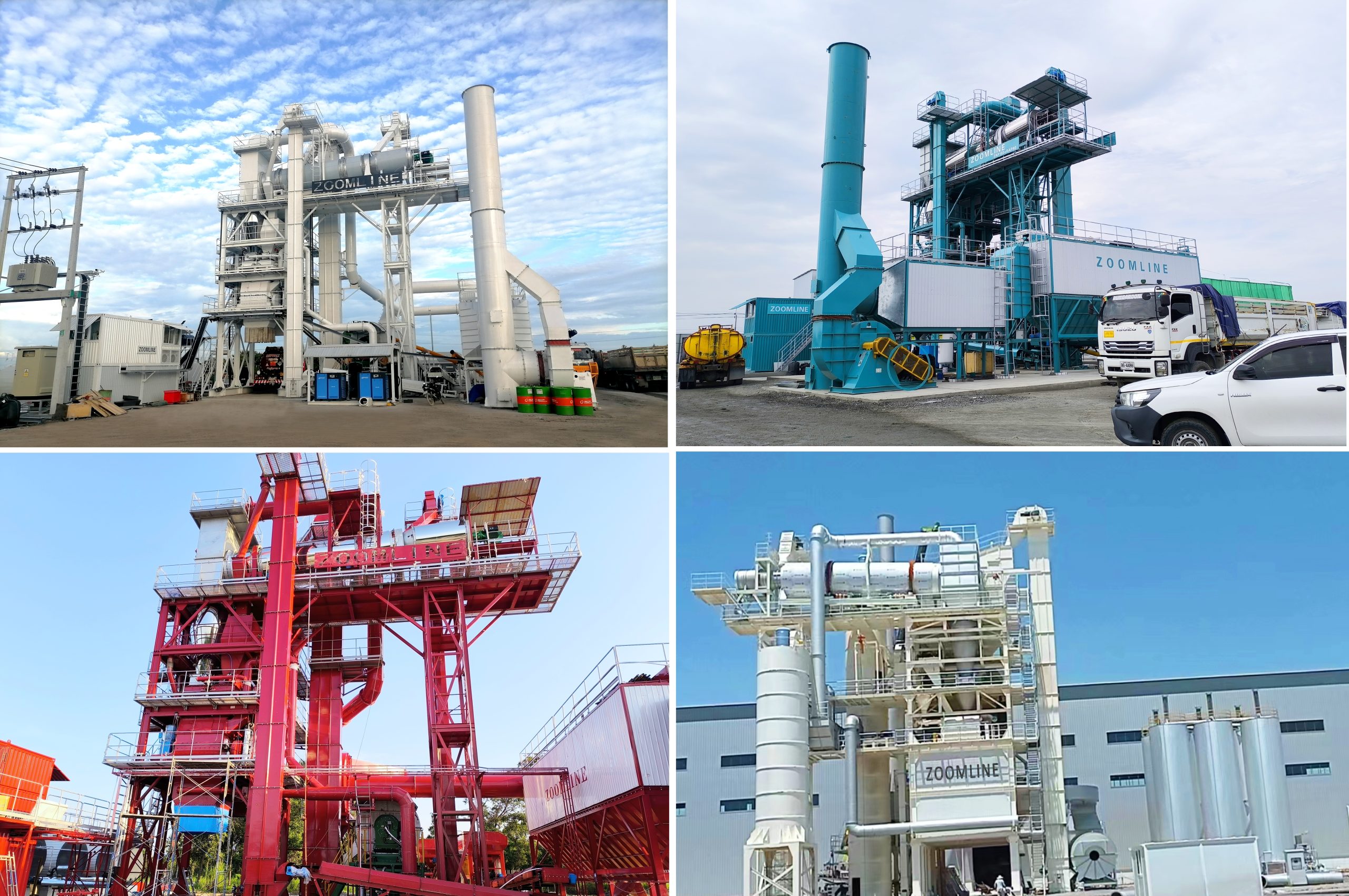
Challenges in Asphalt Recycling Plant
- Cracks and potholes: Cracks and potholes are common issues with recycled asphalt pavements. This is because recycled asphalt has lower strength than virgin asphalt, making it more prone to cracking and brittleness. To avoid this issue, it is essential to properly prepare the driveway foundation before laying recycled asphalt. This may involve removing all debris and ensuring the surface is level. Additionally, adding an extra aggregate layer can enhance the driveway’s durability.
- Drainage issues: When using recycled asphalt for a driveway, be mindful of potential drainage problems. Unlike other paving materials, it is less porous, so water may accumulate and pool on the surface. This can cause damage and safety hazards, especially when water freezes in winter. To avoid this issue, ensure the driveway has the correct slope for efficient drainage. Consider installing a permeable paving system that allows water to penetrate the surface and enter the ground.
- Environmental concerns: While RAP is considered an environmentally friendly option for constructing driveways, potential environmental issues should still be considered. One particular concern is the risk of harmful chemicals leaching into the soil and groundwater. To avoid this issue, it is recommended to hire contractors who use environmentally friendly methods and materials. Additionally, using environmentally friendly sealants can protect the driveway surface and minimize harm to the environment.
- Maintenance Requirements: Although recycled asphalt driveways are durable and have a long lifespan, they still require maintenance. Regular maintenance is necessary to maintain their condition. To protect the surface and extend its lifespan, consider applying a sealant coating periodically. It may also be necessary to fill cracks and potholes from time to time to prevent them from worsening and causing further damage.
Future Trends in Asphalt Recycling
As the construction industry continues to embrace sustainable development principles, the application of asphalt recycling is expected to gain further traction. Some future trends and opportunities in this field include:
Increasing Adoption of Recycled Materials
As the industry recognizes the environmental and economic benefits of these practices, the use of recycled asphalt may become more widespread. This trend will be driven by various factors, including government regulations, corporate sustainability goals, and increased public environmental awareness.
Legislative Pressure and Mandates Promoting Recycling
Governments and regulatory bodies are expected to play an increasingly important role in promoting asphalt recycling. This may include the introduction of new regulations and directives requiring the use of recycled materials in construction projects, as well as incentives for companies adopting sustainable practices.
Potential for 100% Recycled Asphalt Products
As recycling technologies and processes continue to advance, the potential for producing 100% recycled asphalt products becomes more realistic. This will be a significant milestone for the industry in reducing environmental impact and promoting a circular economy.
Conclusion
In summary, the workflow of asphalt recycling equipment is rigorous and efficient, with each step—from milling and crushing old asphalt pavement materials to producing high-quality recycled asphalt mix—being indispensable. The various systems within its structure work in tandem to ensure the smooth progression of the recycling process.
Asphalt recycling equipment not only offers numerous advantages, such as cost savings, environmental friendliness, and reduced landfill waste, but also addresses various challenges, providing strong support for the sustainable development of asphalt pavements. In the future, with the continuous advancement of technology and the improvement of relevant regulations, the asphalt recycling field will usher in broader development opportunities, and the realization of 100% recycled asphalt products is no longer out of reach. The role of asphalt recycling equipment in sustainable construction will become increasingly important.