Asphalt plants play a crucial role in road construction and infrastructure development, providing essential materials for the construction and maintenance of highways, streets, and various transportation facilities. Whether it is a mobile asphalt plant or a continuous asphalt plant, optimizing efficiency is critical for reducing costs, improving productivity, and achieving sustainable development.
Improving asphalt plant efficiency not only significantly reduces operational costs and enhances asphalt product quality but also minimizes waste, conserves energy, and reduces downtime. An efficient asphalt plant can produce more asphalt, meet project deadlines more effectively, and maintain competitiveness in a rapidly changing market. Additionally, focusing on plant efficiency contributes to environmental sustainability, a growing concern in the industry. This article explores key strategies for improving asphalt plant efficiency from multiple angles, providing comprehensive guidance for industry professionals.
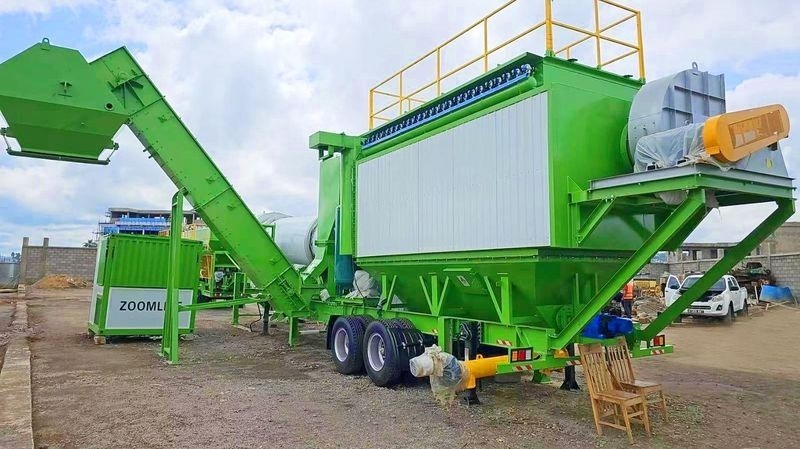
Optimizing Equipment Maintenance and Management
Equipment is the core of asphalt plant production, and scientific maintenance and management are the foundation for ensuring its efficient operation.
Establish a scientific regular maintenance schedule: For critical components such as drying drums, burners, and conveyor belts, develop detailed inspection and maintenance schedules based on their operational characteristics and manufacturer recommendations. Regular maintenance can promptly identify and address issues like wear and tear, preventing equipment failures that lead to downtime and energy waste. For example, improperly maintained drying drums may fail to efficiently heat aggregates, thereby increasing fuel consumption.
Implement preventive maintenance to extend equipment lifespan: Continuously monitor equipment operating conditions to proactively identify potential failure risks and take maintenance measures before issues arise. This not only extends equipment lifespan but also reduces unplanned downtime, ensuring production continuity.
Use high-quality spare parts to reduce failure rates: Select high-quality spare parts that meet standards for replacement. Although the initial cost may be higher, this reduces equipment failure rates and minimizes production interruptions caused by spare part issues, making it more cost-effective in the long run.
Train maintenance personnel to enhance technical capabilities and response speed: Conduct regular professional training for maintenance personnel to familiarize them with the operational principles and maintenance techniques of various equipment, improve their ability to diagnose and resolve issues, and reduce response times.
Introduce equipment health monitoring systems to predict potential issues: Utilize sensors and data analysis technology to monitor equipment parameters such as temperature, vibration, and energy consumption in real time, establish equipment health models, and promptly predict potential issues, providing data support for preventive maintenance.
Improve raw material management
The quality and handling of raw materials directly impact the production efficiency and product quality of asphalt plants.
Optimize raw material procurement and inventory control strategies: Develop reasonable raw material procurement plans based on production schedules and market demand to avoid overstocking or stock shortages. Overstocking increases storage costs and the risk of raw material degradation, while stock shortages may lead to production interruptions.
Ensure raw material quality consistency to reduce production fluctuations: Establish strict raw material quality inspection standards and conduct inspections on aggregates, asphalt, and other raw materials during the procurement process to ensure they meet production requirements. Fluctuations in raw material quality can lead to unstable production processes, affecting asphalt product quality and production efficiency.
Implement advanced grading and screening technologies to improve material utilization: Use efficient grading and screening equipment to precisely grade aggregates, ensuring their particle size meets production formula requirements and reducing waste caused by non-compliant materials.
Closed-loop management measures to reduce raw material waste: Recycle and reuse by-products and defective products generated during production to establish a closed-loop management system for raw materials. For example, recycling old asphalt (RAP) for use in new asphalt mixtures can reduce reliance on virgin aggregates and asphalt.
Collaborate with suppliers to optimize the raw material supply chain: Establish long-term stable partnerships with raw material suppliers to jointly optimize supply chain processes, improving the timeliness and stability of raw material supply. Additionally, share production plans with suppliers to better meet the factory’s raw material needs.
Improve energy efficiency
Asphalt production is an energy-intensive process, and improving energy efficiency is critical for reducing costs and minimizing environmental impact.
Adopt energy-efficient burners and high-efficiency heating systems: Select burners with high combustion efficiency, optimize the combustion process, and reduce fuel waste. Additionally, adopt high-efficiency heating systems to improve thermal energy transfer efficiency and reduce energy consumption.
Optimize thermal energy recovery and reuse technologies: Install waste heat recovery systems to recover thermal energy from exhaust gases and wastewater generated during production, and use it for preheating aggregates, heating asphalt, etc., to improve energy utilization efficiency.
Explore the application of renewable energy or alternative fuels: Consider using natural gas, biomass, and other alternatives to traditional fuels. These fuels may not only reduce energy costs but also decrease pollutant emissions. For example, the use of biomass fuels can help reduce carbon emissions.
Implement energy consumption monitoring and data analysis for continuous improvement: Establish an energy consumption monitoring system to record energy consumption data in real time across all production processes. Through data analysis, identify areas of weak energy consumption and develop targeted improvement measures to continuously optimize energy usage efficiency.
Assess the contribution of energy efficiency to long-term cost savings: Conduct a cost-benefit analysis of all energy efficiency improvement measures to evaluate the cost savings they can achieve in long-term operations, providing a basis for the formulation of energy strategies.
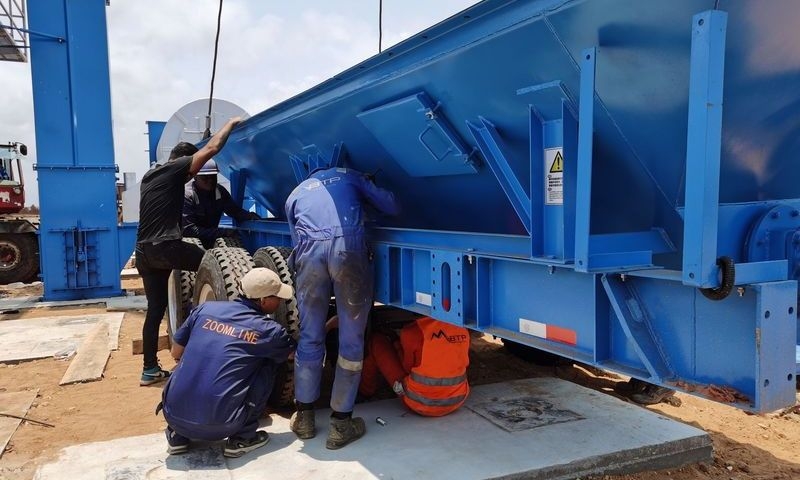
Automation and Technological Upgrades
Automation and technological upgrades are important means of improving the production efficiency and modernization level of asphalt plants.
Introducing automated control systems to improve production accuracy and efficiency: Advanced automated control systems are used to precisely control production parameters such as raw material ratios, temperature control, and mixing time, thereby reducing human operational errors and improving the consistency of asphalt product quality and production efficiency. For example, automated systems can adjust drum speed in real time based on demand, thereby reducing fuel consumption while maintaining quality.
Implementing real-time monitoring and data analysis technologies to optimize production: By installing sensors and data acquisition devices, various production process data such as temperature, pressure, flow rate, and energy consumption can be collected in real time. Data analysis technologies are then used to process and analyze this data, identifying areas for optimization in the production process and continuously improving production processes.
Upgrade outdated equipment to enhance production capacity and stability: For equipment that has been in use for over 10-15 years, performance may decline, control algorithms may become outdated, and replacing spare parts may become challenging. Timely upgrading of such equipment can enhance production capacity and stability, reducing production fluctuations caused by equipment issues.
Utilize IoT technology to achieve equipment interconnection and intelligent management: Connect various types of equipment within the factory through IoT technology to enable data sharing and collaborative work between equipment. Managers can monitor equipment operating status in real time through remote terminals, perform remote control and scheduling, and improve management efficiency.
Evaluate the cost-benefit ratio and return on investment of new technology investments: When introducing new technologies and equipment, conduct a comprehensive cost-benefit analysis to assess the return on investment and ensure the rationality of investment decisions.
Optimizing production processes
A well-designed production process can reduce bottlenecks and redundant steps, thereby improving production efficiency.
Simplifying production processes to reduce bottlenecks and redundant steps: Review and analyze existing production processes, eliminate unnecessary steps, and optimize production workflows to reduce production bottlenecks. For example, optimize raw material transportation routes to avoid crossovers and waiting times during material handling.
Implement lean production principles to eliminate waste: Apply lean production concepts to identify various forms of waste in the production process, such as overproduction, waiting time, and transportation waste, and take measures to eliminate them, thereby improving the utilization rate of production resources.
Optimize production scheduling to improve equipment utilization: Develop reasonable production scheduling plans based on order demand, equipment status, and raw material supply conditions to balance the load on each piece of equipment, improve equipment utilization, and avoid situations where some equipment is overused while others remain idle.
Reduce unplanned downtime and maintenance interruptions: Reduce unplanned downtime through measures such as strengthening equipment maintenance and optimizing production scheduling. Additionally, schedule maintenance during non-peak production periods to minimize disruptions to production.
Adopt flexible production to adapt to diverse market demands: As market demand for asphalt products becomes more diverse, implement flexible production models to enable the factory to quickly adjust production parameters and product formulas to meet the needs of different customers and enhance market responsiveness.
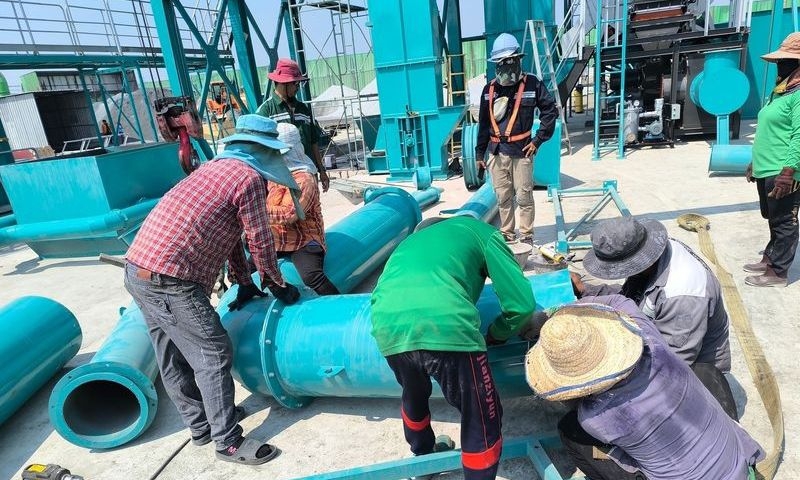
Employee Training and Skill Enhancement
Employees are the executors of production, and their skill levels and work attitudes directly impact production efficiency.
Conduct regular skill training for operators to improve operational efficiency: Provide systematic skill training for operators to ensure they master equipment operation techniques, production process requirements, and quality control standards, thereby enhancing operational accuracy and efficiency. For example, train operators to adjust equipment parameters according to different production needs to reduce energy waste.
Promote safe operating practices and efficient work habits to reduce accident rates: Strengthen safety education and training to instill safety awareness among employees, ensuring strict adherence to safety operating procedures to minimize downtime and personnel injuries caused by safety incidents. Simultaneously, cultivate efficient work habits among employees to enhance overall work efficiency.
Establish incentive mechanisms to enhance employee motivation and sense of responsibility: Implement reasonable incentive mechanisms to reward employees who demonstrate outstanding performance in areas such as production efficiency improvement, quality enhancement, and cost savings, thereby stimulating their work motivation and sense of responsibility.
Develop cross-functional teams to enhance collaboration and flexibility: Form cross-departmental collaborative teams to promote communication and cooperation among different positions, thereby improving the team’s ability to address complex issues and enhance work flexibility.
Introduce virtual reality (VR) training to simulate complex operational scenarios: Utilize VR technology to create virtual production operation scenarios, allowing employees to train in complex operations within a virtual environment, familiarize themselves with emergency response procedures, and enhance their ability to handle real-world situations.
Environmental and Sustainability Practices
While pursuing efficiency, prioritizing environmental and sustainability development is a critical responsibility for modern asphalt plants.
Implementing exhaust gas and dust control measures to comply with environmental standards: Installing effective exhaust gas treatment equipment and dust collection systems to reduce emissions of exhaust gas and dust during production, ensuring compliance with national and local environmental regulations.
Promoting asphalt recycling technology to reduce resource consumption: Increasing efforts to recycle and utilize recycled asphalt pavement (RAP), improving RAP utilization rates through adjustments to plant design and storage capacity. Adopt warm-mix asphalt (WMA) technology to lower production temperatures, reduce energy consumption, and minimize greenhouse gas emissions.
Optimize water resource management to minimize environmental impact: Develop a reasonable water usage plan, treat and recycle wastewater generated during production, and reduce the consumption of fresh water resources and wastewater discharge.
Comply with environmental regulations and pursue green certifications to enhance brand image: Strictly adhere to all environmental regulations, actively participate in green certification activities, establish a positive corporate image, and enhance market competitiveness.
Explore the impact of carbon neutrality goals on production strategies: As global attention on carbon neutrality grows, asphalt plants should proactively explore the impact of carbon neutrality goals on production strategies, research feasible emission reduction measures, and prepare for achieving carbon neutrality objectives.
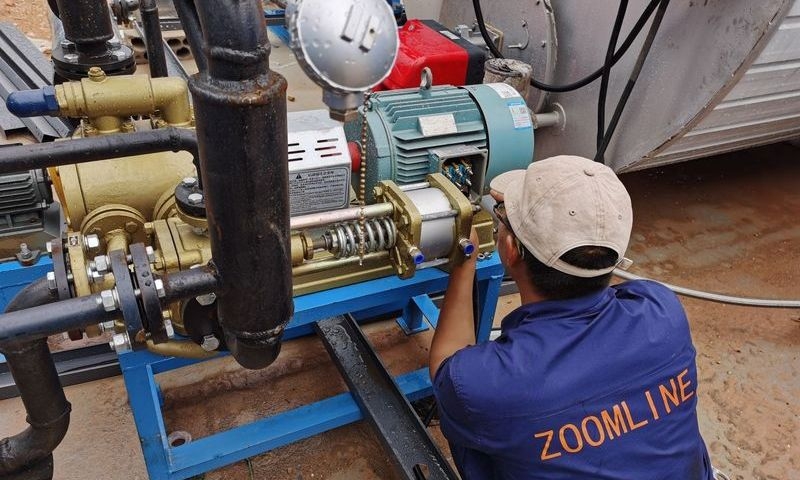
Data-driven decision support
Data is an important basis for optimizing production and improving efficiency, and it is crucial to establish a comprehensive data-driven decision-making system.
Establish a comprehensive production data collection and management system: Integrate various types of data from the production process, including equipment operation data, raw material data, production process data, energy consumption data, etc., and establish a unified data management platform to ensure data integrity and accuracy.
Optimize production parameters and resource allocation using big data analysis: Apply big data analysis techniques to conduct in-depth analysis of collected data, identify relationships between production parameters, product quality, and energy consumption, and optimize production parameter settings. Additionally, allocate raw materials, energy, and other resources based on data analysis results to improve resource utilization efficiency.
Implement predictive maintenance to reduce the risk of failure and downtime: Based on equipment operating data and historical failure data, establish predictive models to predict possible equipment failures, arrange maintenance in advance, and reduce the risk of failure and downtime.
Use data visualization tools to assist management decision-making: Present complex data in visual forms such as charts and dashboards, enabling management to intuitively understand production status and trends in various indicators, providing clear basis for decision-making.
Combine artificial intelligence technology to predict market demand and adjust production: Use artificial intelligence technology to analyze market data and historical sales data to predict changes in market demand for asphalt products, adjust production plans in a timely manner, and avoid overproduction or supply shortages.
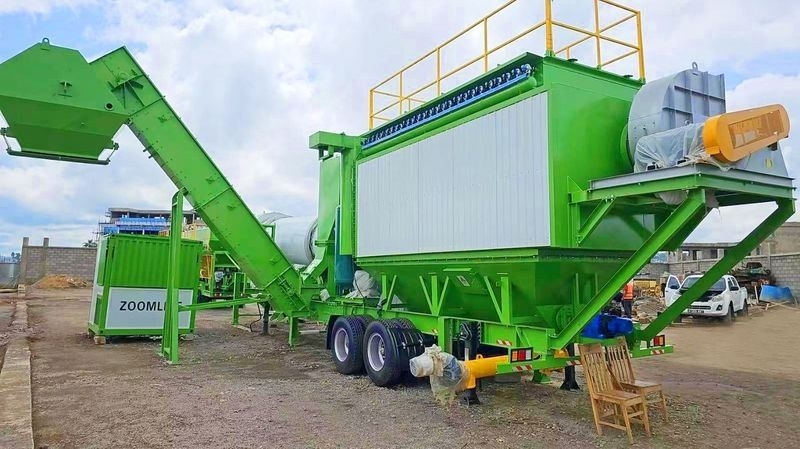
Supply chain and logistics optimization
A smooth supply chain and logistics system are important links in ensuring the efficient operation of asphalt plants.
Optimize transportation routes to reduce logistics costs and time: Based on the distribution of raw material supply locations and product sales locations, optimize transportation routes, select the shortest paths and most reasonable transportation methods to reduce transportation costs and time.
Establish long-term strategic partnerships with suppliers to ensure stable supply: Establish long-term stable strategic partnerships with raw material suppliers and logistics service providers, sign detailed cooperation agreements, clarify the rights and obligations of both parties, and ensure stable raw material supply and timely product transportation.
Implement a real-time logistics tracking system to enhance transparency: Utilize GPS and other technologies to establish a real-time logistics tracking system, monitor transportation vehicles and goods throughout the entire process, promptly track the location and status of goods, enhance transparency in the logistics process, and facilitate timely responses to unforeseen circumstances during transportation.
Reduce material loss and quality issues during transportation: Strengthen maintenance and management of transportation vehicles to ensure the quality and safety of raw materials and products during transportation, thereby reducing material loss and quality issues caused by improper transportation.
Explore multimodal transportation to enhance logistics efficiency: Based on actual conditions, explore multimodal transportation methods such as road, rail, and waterways to fully leverage the advantages of different transportation modes, improve logistics efficiency, and reduce logistics costs.
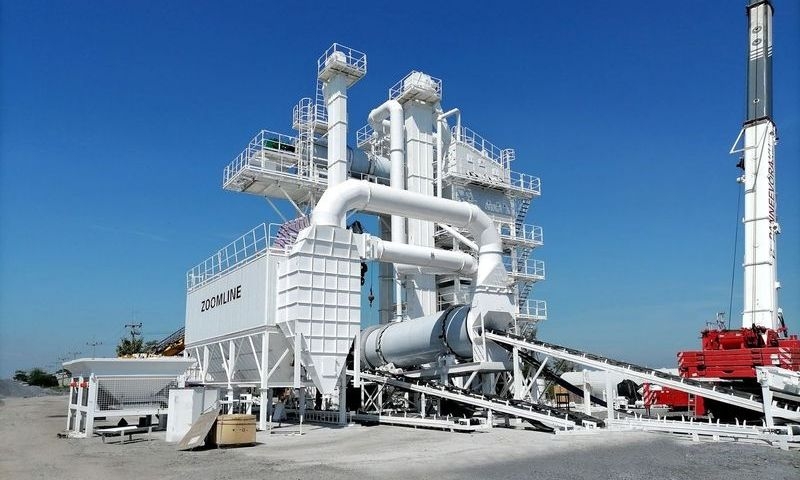
Quality control and standardization
Stable product quality is the foundation for the survival and development of asphalt plants, and establishing a comprehensive quality control and standardization system is crucial.
Establish strict quality inspection processes to ensure product consistency: Establish a comprehensive quality inspection process from raw material intake to finished product shipment, rigorously monitoring every stage to ensure the consistency and stability of asphalt product quality.
Obtain ISO or other industry standard certifications to enhance market trust: Actively apply for and obtain ISO or other relevant industry standard certifications to demonstrate that the company’s production management standards and product quality meet industry-leading levels, thereby enhancing market trust.
Continuously improve product formulations to meet diverse customer needs: Based on customer feedback and changes in market demand, continuously refine product formulations to enhance product performance and applicability, thereby satisfying the diverse needs of different customers.
Use advanced testing equipment to improve quality control precision: Introduce advanced testing equipment, such as spectrometers and Marshall stability testers, to enhance the precision and efficiency of quality testing, providing reliable technical support for quality control.
Establish a quality feedback mechanism to quickly respond to customer needs: Establish a comprehensive customer quality feedback mechanism to promptly collect customer opinions and suggestions on product quality, address and improve issues raised in feedback, and enhance customer satisfaction.
Risk Management and Emergency Response
There are various risks involved in the production process of an asphalt plant. Effective risk management and emergency response can minimize losses and ensure production safety.
Develop a comprehensive risk assessment and management plan: Conduct a comprehensive assessment of potential risks such as equipment failures, raw material shortages, natural disasters, and safety incidents that may arise during the production process of an asphalt plant, and establish corresponding risk management plans and response measures.
Establish an emergency response mechanism to address equipment failures or supply chain disruptions: Develop detailed emergency response plans, clearly define emergency response organizations, responsibilities, and procedures, and ensure that emergency responses can be swiftly activated in the event of equipment failures or supply chain disruptions to minimize losses.
Conduct regular risk simulation exercises to enhance response capabilities: Regularly organize risk simulation exercises to familiarize employees with emergency response procedures and operational methods, thereby improving their ability to handle sudden incidents.
Optimize insurance strategies to reduce unexpected losses: Based on the actual risk situation of the factory, select appropriate insurance products and optimize insurance strategies to reduce economic losses caused by unexpected events.
Introduce digital tools to monitor potential risks in real time: Use digital tools to monitor potential risks in the production process in real time, promptly identify risk hazards, and take measures to prevent them.
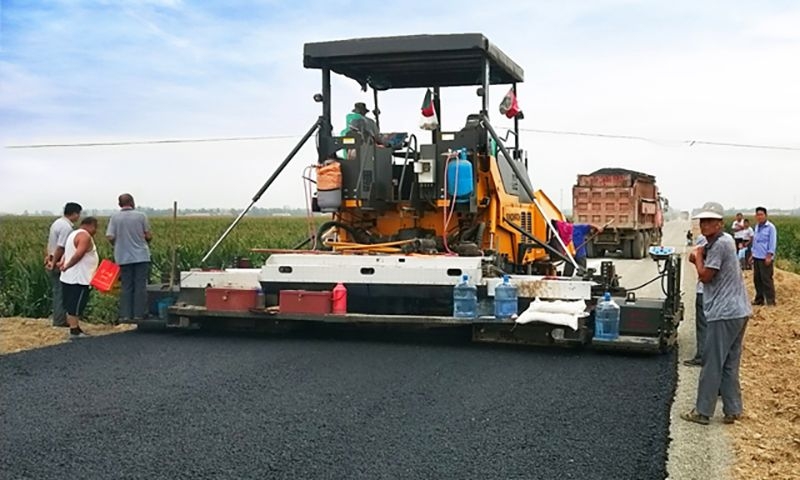
Market and customer-oriented strategy
A market and customer-oriented approach is key to maintaining competitiveness. Asphalt plants should actively adjust their strategies to adapt to market changes and customer needs.
Optimize products and services through market research to meet customer needs: Conduct regular market research to understand market trends and customer needs, and optimize product types and service content based on research results to enhance customer satisfaction.
Establish a customer feedback mechanism to quickly improve production processes: Establish convenient customer feedback channels to promptly collect customer opinions and suggestions on products and services, and use feedback information to quickly improve production processes and service quality.
Provide customized asphalt products to enhance market competitiveness: Offer customized asphalt products and solutions tailored to the specific needs of different customers to meet their personalized requirements and enhance the company’s market competitiveness.
Optimize after-sales service to enhance customer satisfaction and loyalty: Establish a comprehensive after-sales service system to provide customers with timely technical support, product maintenance, and other services, thereby improving customer satisfaction and loyalty.
Analyze market trends to adjust production strategies and resource allocation: Closely monitor industry development trends and market changes, promptly adjust production strategies and resource allocation, seize market opportunities, and mitigate market risks.
Innovation and R&D investment
Innovation is the driving force behind corporate development, and sustained R&D investment can bring technical and competitive advantages to asphalt plants.
Establish an internal R&D team to develop efficient production technologies: Form a professional internal R&D team dedicated to researching and developing asphalt production technologies, continuously exploring new methods and technologies to improve production efficiency, reduce costs, and enhance product quality.
Collaborate with universities or research institutions to explore new materials and processes: Strengthen cooperation with universities and research institutions, leverage their research resources and talent advantages, and jointly conduct research and application of new materials and processes to accelerate the pace of technological innovation.
Invest in green technology and sustainable production methods: Increase R&D investment in green technology and sustainable production methods, such as new environmentally friendly asphalt materials and energy-saving and emission-reduction production processes, to drive the company toward green and sustainable development.
Pilot the application of new technologies to verify their feasibility: When introducing new technologies, first conduct small-scale pilot applications to verify their feasibility and effectiveness, then decide whether to roll them out on a large scale based on the pilot results to reduce the risks associated with technology application.
Protect intellectual property rights to maintain technological competitive advantages: Emphasize intellectual property protection, promptly apply for patents and other intellectual property protections for R&D outcomes, prevent infringement of technological achievements, and maintain the company’s technological competitive advantages.
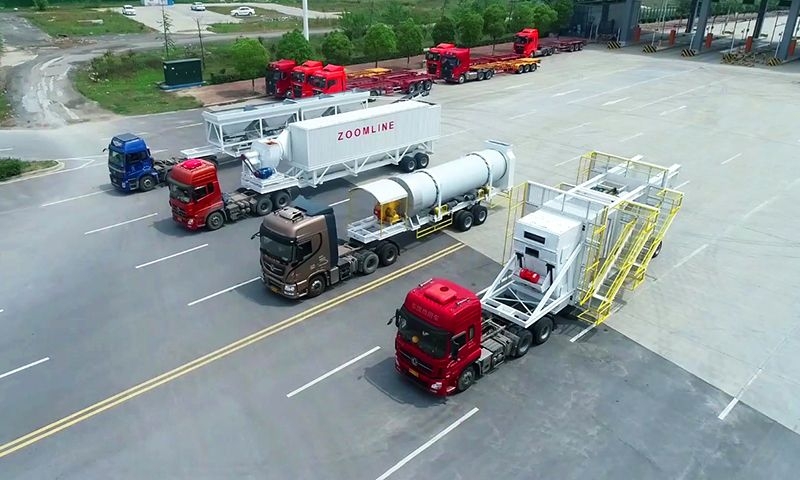
Conclusion
Improving asphalt plant efficiency is a systematic endeavor that requires comprehensive measures from multiple angles, including equipment maintenance, raw material management, energy efficiency, automation upgrades, production process optimization, employee training, environmental practices, data-driven approaches, supply chain optimization, quality control, risk management, market orientation, and innovative R&D.
Implementing these strategies comprehensively not only brings significant economic benefits to the company, reduces operational costs, improves product quality and production efficiency, but also generates positive environmental benefits, reduces energy consumption and pollutant emissions, and promotes the sustainable development of the industry. Additionally, an efficient asphalt plant can better meet market demands, enhance customer satisfaction, and strengthen the company’s market competitiveness.
In future development, asphalt plants should continue to monitor industry technological trends and market changes, continuously assess and optimize strategies, maintain innovative vitality, actively address various challenges, and achieve long-term stable and efficient operations to make greater contributions to road construction and infrastructure development.