As a core piece of equipment in road construction, asphalt mixing plants often consume a significant amount of energy during the production of high-quality asphalt mixtures. According to industry data, energy costs account for 30%-40% of the total operating costs of asphalt mixing plants, with the energy consumption of drying drums alone accounting for 50%-70% of total energy consumption.
In the context of rising energy prices and increasingly stringent environmental regulations, reducing energy consumption not only directly cuts operational costs but is also a key factor for enterprises to achieve sustainable development and enhance their market competitiveness. This article will begin with an analysis of energy consumption structure and provide a detailed introduction to practical strategies for reducing energy consumption in asphalt mixing plants.
Factors Affecting Energy Consumption
To reduce energy consumption, it is first necessary to identify the pathways of energy consumption within an asphalt mixing plant. The core energy-consuming processes primarily include the following aspects:
Aggregate drying and heating system
The drying drum is the ‘energy-intensive component’ of an asphalt mixing plant, requiring high temperatures (typically exceeding 160°C) to evaporate moisture from the aggregates. The fuel sources are primarily natural gas, diesel, or heavy oil. If the burner efficiency is low or the drum insulation is poor, heat loss can reach 10%-20%.
Asphalt heating and storage
Asphalt must be maintained at a constant temperature of 150-180°C to ensure flowability. The continuous operation of the heating system (thermal oil furnace or electric heater) consumes a significant amount of energy. Heat loss from pipes and storage tanks is also a major component of energy consumption.
Mixing and Conveying Equipment
Although the individual energy consumption of equipment such as motor-driven mixing tanks, hot material elevators, and belt conveyors is lower than that of heating systems, their continuous operation results in significant cumulative electricity consumption.
Dust Collection and Ventilation Systems
The exhaust fans and ventilation equipment of bag-house dust collectors must operate 24 hours a day to meet environmental protection requirements, accounting for approximately 15%-20% of total electricity consumption.
Control Systems and Automation Equipment
While modern control systems have low energy consumption themselves, they can indirectly reduce total energy consumption by 3%-5% through optimized combustion and production rhythm adjustment.
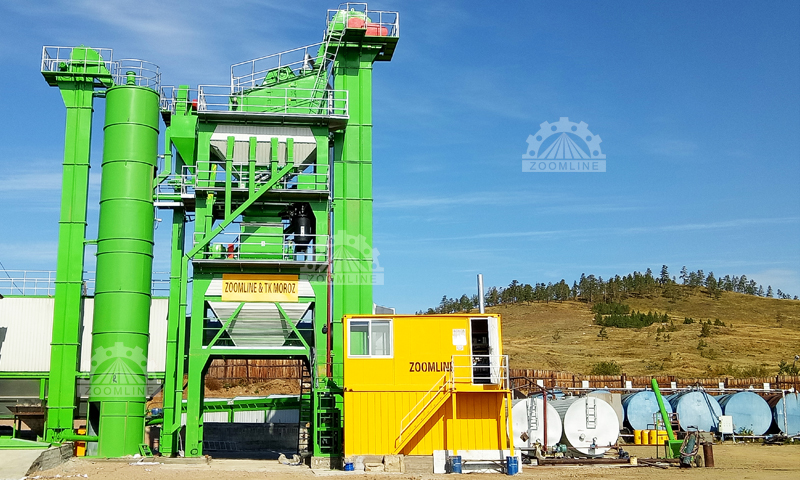
How to reduce energy consumption in asphalt mixing plant?
Optimizing cold aggregate processing and combustion control
Reducing aggregate moisture content
For every 1% increase in aggregate moisture content, the energy consumption of the drying system increases by 10%. By constructing rain shelters, hardening the aggregate yard surface, and setting drainage slopes, the aggregate moisture content can be controlled below 3%.
Case Study: After renovating its aggregate yard, a mixing plant reduced the average aggregate moisture content from 5% to 2%, saving approximately 80,000 yuan in fuel costs per month.
Controlling Aggregate Particle Size
Keeping aggregate particle size below 2.36 mm reduces thermal resistance during drying. By grading and screening aggregates and crushing non-conforming particles, drying efficiency can be improved by 15%.
Selecting high-efficiency fuel
Prioritize fuels with low moisture content and high calorific value (such as heavy oil), which have combustion efficiency 8%-10% higher than regular diesel.
Fuel selection must comprehensively consider purity, viscosity, and transportation costs to avoid burner blockages caused by excessive impurities.
Modify the combustion system
Install a pneumatic three-way valve to automatically switch between heavy oil and diesel. Use diesel during startup and low-load conditions, and switch to heavy oil during high-load conditions to reduce fuel costs.
Upgrade the fuel supply piping of the burner to reduce resistance losses during fuel transportation.
Optimize burner performance and maintenance
Maintain Optimal Air-Fuel Ratio
Adjust the air-fuel ratio (typically 10:1–12:1) based on the burner model and production requirements to ensure complete fuel combustion. Regularly use a flue gas analyzer to measure oxygen content in exhaust gases, maintaining the excess air coefficient between 1.1 and 1.2.
Enhance fuel atomization
Use high-efficiency atomizing nozzles to control fuel atomization particle diameter between 50-80μm, improving combustion efficiency. Clean the atomizer weekly to prevent poor atomization due to blockages.
Adjust the flame shape
Adjust the position of the flame baffle to align the flame center with the center of the drying drum, and control the flame length to within 2/3 of the drum length to avoid direct contact between the flame and the drum wall (which could cause localized overheating and energy waste).
The flame should be stable with no flickering or abnormal noise to ensure uniform heat transfer to the aggregate.
Enhance equipment insulation to reduce heat loss
Insulation treatment for critical components
Asphalt storage tanks, hot material silos, and conveying pipelines must be wrapped with 5–10 cm thick insulation cotton and fitted with a metal protective layer, keeping the surface temperature below 50°C and reducing heat loss by over 60%.
The outer surface of drying drums should be wrapped with 5 cm thick high-temperature resistant insulation cotton, reducing surface temperature from 300°C to 80°C and reducing heat loss by approximately 8%.
Regular inspection of insulation layers
Inspect insulation layers monthly for damage or peeling, and promptly repair any gaps. Damaged insulation layers can increase heat loss by over 30%, so special attention should be paid to heat-prone areas such as pipe joints and valves.
Application of variable frequency technology
Hot material conveying system
Install variable frequency motors on hoists and belt conveyors to automatically adjust speed based on material volume. Start at low frequency (30 Hz), increase to rated frequency (50 Hz) during operation, and reduce to low frequency braking before shutdown, achieving energy savings of 20%-30%.
Exhaust Fans and Dust Collection Systems
Exhaust fans account for 25% of the total electricity consumption at a mixing plant. By using variable frequency control to adjust fan speed based on dust concentration, and operating at 30Hz during non-production periods, energy savings of up to 40% can be achieved.
Asphalt Circulation Pump
The asphalt circulation pump does not need to operate at full load during non-mixing periods. After adopting variable frequency technology, the frequency can be automatically adjusted based on asphalt temperature, achieving a 30% energy savings while reducing pump wear.
Upgrading the automated control system
Installing an intelligent control system enables real-time monitoring of parameters such as aggregate moisture content, drum outlet temperature, and burner load, automatically adjusting fuel supply and airflow to improve thermal efficiency by 5–8%.
A production scheduling module prevents equipment from running idle. Data shows that optimized production scheduling can reduce idle energy consumption by 10%.
Regular Equipment Maintenance
Clean burner nozzles and inspect air filters weekly to prevent incomplete combustion due to blockages.
Inspect dryer drum seals monthly, replace worn bearings and seals to reduce heat leakage.
Calibrate temperature sensors and pressure transmitters quarterly to ensure accurate control system data.
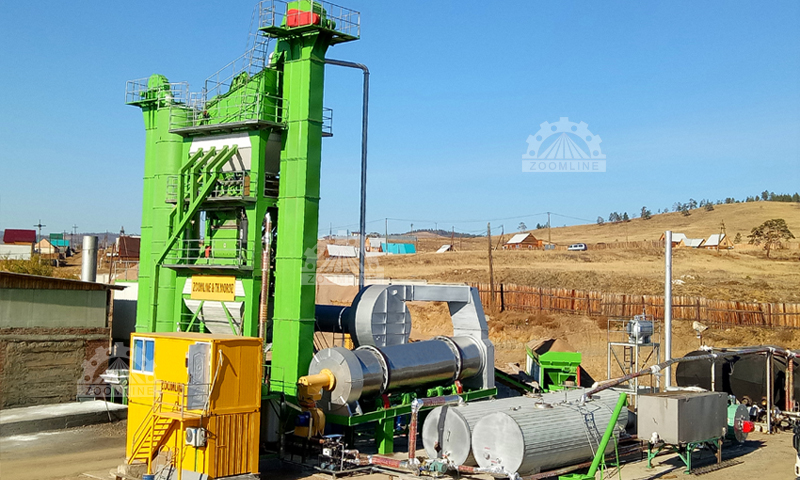
Implementation Results and Case Studies
A medium-sized asphalt mixing plant achieved a 22% reduction in total energy consumption through comprehensive renovations (including combustion system optimization, variable frequency drive upgrades, and insulation upgrades), with a payback period of approximately eight months.
Asphalt mixing plant for a highway project reduced its asphalt energy consumption from 8.5 kg/t to 7.2 kg/t after adopting an intelligent control system, saving 120,000 yuan in energy costs per month.
Conclusion
Reducing energy consumption at asphalt mixing plants cannot be achieved through a single measure; it requires a combination of equipment upgrades, process optimization, and intelligent control. By implementing the strategies outlined in this article, mixing plants can recoup their investment within 1-2 years and enjoy long-term cost advantages from reduced energy consumption.
In the context of increasingly stringent environmental policies, low-energy, low-emission plants will gain a competitive edge in the market. Take action today and start developing your energy optimization plan!
Call to Action
Need a professional energy optimization solution? Contact us for a free on-site assessment and customized renovation recommendations. Let’s work together to drive the green upgrade of asphalt mixing plants!