In an asphalt mixing plant, the burner plays a crucial role, serving as the “heart” of the entire mixing system. Its selection directly impacts production quality, production efficiency, fuel costs, and environmental compliance. This article provides a comprehensive overview of burner-related knowledge for asphalt mixing plants, including their definition, types, key factors to consider when selecting, how to match the appropriate burner type based on requirements, their importance in the asphalt mixing process, performance metrics, special considerations for heavy oil characteristics, and maintenance tips, offering a comprehensive and practical reference for selecting the right burner.
What is an Asphalt Mixing Plant Burner
An asphalt mixing plant burner is a critical component of the thermal exchange system in asphalt mixing equipment, primarily used to provide the necessary heat for aggregate drying. Its performance directly impacts the asphalt mixing plant’s fuel consumption, environmental performance, operational efficiency, equipment stability, and the quality of the final product. In essence, the performance of the burner significantly determines the overall operational status and production efficiency of the asphalt mixing plant.
Types of Burners for Asphalt Mixing Plants
Pulverised Coal Burner
Suitable for applications using coal powder as fuel, these burners offer high combustion efficiency and uniform heat release. Such burners typically feature efficient coal powder conveying systems and precise air supply devices. Through specially designed swirl combustion heads, they ensure thorough mixing of coal powder with air to achieve complete combustion. In regions with abundant coal resources and stable coal powder supply, using coal powder burners can significantly reduce fuel costs while creating a sustained high-temperature environment for asphalt production, effectively enhancing production efficiency.
Oil Burner
These burners use liquid petroleum products such as diesel or heavy oil as fuel, making them particularly suitable for regions with limited natural gas supply or restrictions on coal use. These burners employ advanced atomization technology, using high-pressure oil pumps to spray fuel into the combustion chamber in a mist form, which then mixes thoroughly with air for efficient combustion. They feature quick startup and an intuitive operating interface, allowing even non-professionals to operate them swiftly. The combustion process produces minimal dust pollution, making it cleaner than coal-fired equipment. It is commonly used in small to medium-sized asphalt mixing plants or temporary work scenarios.
Natural Gas Burner
Utilizes pipeline natural gas or liquefied natural gas (LNG) as fuel, offering unparalleled environmental advantages. Combustion byproducts primarily consist of carbon dioxide and water vapor, with nitrogen oxide emissions far below national standards, aligning with modern green construction requirements. With a precise air-fuel ratio control system, natural gas burners achieve thermal efficiency of over 90%, with uniform and stable flame temperatures. They can precisely adjust output power to meet asphalt heating requirements under various operating conditions, making them the preferred equipment for large-scale, environmentally friendly mixing plants.
These burners integrate both fuel oil and natural gas combustion modes, enabling seamless fuel switching via an intelligent switching mechanism. When the natural gas supply is unstable, it can be switched to fuel mode with a single button to ensure production continuity; when natural gas prices are advantageous, it can be quickly switched to reduce operational costs. This type of burner is equipped with a dual-fuel injection system and an adaptive control system, enabling efficient and stable operation regardless of the high viscosity characteristics of heavy oil or the low resistance combustion of natural gas. It combines flexibility and economy, making it an ideal solution for complex energy environments.
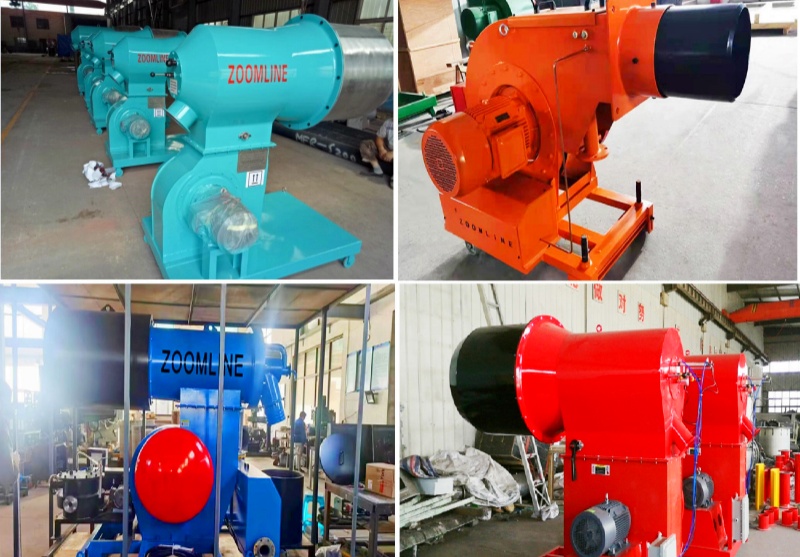
Key Factors to Consider When Choosing a Burner
When selecting a suitable burner for an asphalt mixing plant, it is crucial to carefully consider multiple core elements. Below, we will delve into these key points to help you make an informed decision.
Fuel Availability and Costs
Fuel availability and cost are core considerations when selecting a burner. From the perspective of supply stability, companies must research the fuel supply chain in their region to ensure the reliability of the selected fuel source and avoid production disruptions due to supply interruptions. For example, in some remote areas, diesel transportation is inconvenient, while coal supply is abundant and prices are stable. Selecting a coal burner can ensure production continuity. From a cost perspective, in addition to considering current prices, it is essential to analyze historical price fluctuations and future trend forecasts. Taking diesel as an example, its price is significantly influenced by the international crude oil market, and during periods of global instability, price fluctuations are frequent. In contrast, natural gas prices are relatively stable. Although the initial investment cost for natural gas equipment is higher, its energy efficiency is 30%-40% higher than coal, effectively reducing fuel costs per unit of production. From a lifecycle perspective, it offers greater cost-effectiveness. Additionally, fuel transportation and storage costs must be considered. For instance, coal requires substantial storage space, and losses occur during transportation, all of which increase hidden costs.
Environmental Impact
Under increasingly stringent environmental policies, the environmental impact of burners has become a key metric in corporate decision-making. The combustion products of different fuels vary significantly. Natural gas primarily consists of methane, which, when fully combusted, primarily produces carbon dioxide and water. Its nitrogen oxide (NOx) emissions typically remain below 50 mg/m³, far lower than those of coal and diesel burners. Diesel combustion, however, produces large amounts of particulate matter (PM) and carbon monoxide (CO), especially during incomplete combustion. These pollutants not only exacerbate air pollution but may also impact the health of surrounding residents. Coal combustion releases large amounts of sulfur dioxide (SO₂), one of the primary causes of acid rain. Some regions have implemented policies to impose tiered controls on pollutant emissions from asphalt mixing plants, levy high environmental taxes on enterprises using high-pollution fuels, and even require them to rectify within a specified timeframe. Therefore, enterprises choosing natural gas burners can not only meet environmental regulations and avoid penalty risks but also enhance their brand image through green production, obtain government credit and tax incentives, and align with sustainable development strategies.
Operational Efficiency and Maintenance
The operational efficiency of burners directly impacts production efficiency, while maintenance costs affect a company’s long-term operational expenses. Natural gas burners utilize premixed combustion technology, resulting in uniform flame temperatures and thermal efficiency exceeding 90%. The combustion products are clean, reducing corrosion and scaling of internal components. Maintenance intervals typically range from 6 to 12 months, with primary maintenance tasks including regular inspections of gas valve seals and ignition system stability. Diesel burners have a fast startup speed, but due to impurities in diesel fuel, long-term use can lead to issues such as clogged injectors and pump wear. Comprehensive maintenance is required every 2-3 months on average, including filter replacement and injector cleaning, which increases labor and parts costs. Coal burners, due to the inconsistent quality of coal, produce large amounts of ash and coking during combustion, which not only reduces combustion efficiency but may also cause furnace blockages. Weekly ash removal operations are required, and monthly inspections of critical components such as the grate and air supply system are necessary. Maintenance costs for coal burners are approximately 3-5 times those of natural gas burners. Additionally, frequent maintenance can cause equipment downtime, affecting production schedules and order delivery.
Choosing the Right Burner Based on Your Needs
- Pursuing high efficiency and low emissions: Natural gas burners. If the primary focus is on reducing fuel consumption and minimizing environmental impact, natural gas burners are an ideal choice. They offer exceptional efficiency and low emissions, making them an excellent option for businesses aiming to comply with environmental regulations while maintaining high production standards.
- Seeking cost-effective operations: Coal powder burners. For businesses located in regions rich in coal resources, coal powder burners may offer a cost-effective solution. They require lower initial investment and are suitable for large-scale asphalt production. However, maintenance costs and environmental impacts must be carefully considered.
- Seeking flexibility and reliability: Fuel oil burners (such as diesel burners). If a reliable and stable heat source is required and fuel supply is not an issue, diesel burners are a good choice. Although ongoing fuel costs may be higher, their operational reliability and ease of use make them a popular choice for many asphalt mixing plants.
The Importance of Burners in the Asphalt Mixing Process
In the asphalt mixing process, burners play a crucial role. They act as the “heart” of the entire mixing system, providing the necessary thermal energy for asphalt mixture production. Their performance and operational status directly impact the quality of the asphalt mixture, production efficiency, and energy consumption.
The core function of a burner is to release heat by burning fuel to meet the heating requirements of asphalt mixture production. In asphalt mixing plants, aggregates must be heated to a specific temperature, typically between 160-190°C, while asphalt must be heated to a flowing state to ensure uniform mixing with aggregates. Burners generate high-temperature flames and flue gases by efficiently combusting fuels such as heavy oil, diesel, or natural gas. These high-temperature media transfer heat to aggregates and asphalt through heat exchangers.
During fuel combustion, the burner must precisely control the air-to-fuel mixture ratio to achieve complete combustion. This not only improves fuel efficiency and reduces energy waste but also minimizes emissions of harmful gases (such as carbon monoxide and nitrogen oxides), meeting environmental protection requirements. If the air-to-fuel mixture ratio is inappropriate, it can lead to incomplete combustion, which not only wastes fuel and increases production costs but also produces black smoke and harmful gases, polluting the environment and potentially affecting the quality of aggregate heating.
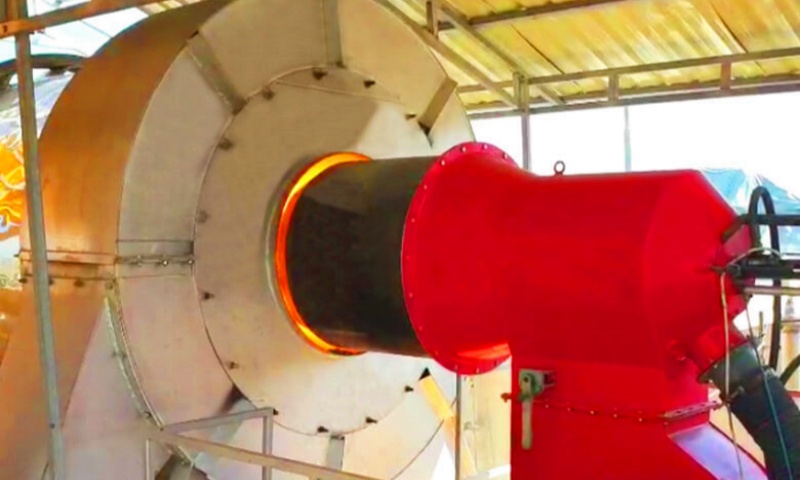
The burner also has flexible adjustment capabilities, enabling real-time adjustment of heat output based on production requirements. During asphalt mixing, different production conditions (such as aggregate moisture content and feed rate changes) require varying levels of heat. The burner can adjust the size and temperature of the flame by regulating fuel supply and airflow, ensuring that aggregates and asphalt are heated to the set temperature and maintaining the stability of asphalt mixture quality. For example, when aggregate moisture content is high, the burner must provide additional heat to evaporate moisture and achieve the specified heating temperature.
Additionally, the stable operation of the burner is critical to ensuring continuous production at the asphalt mixing plant. Modern burners are typically equipped with comprehensive safety protection devices, such as flame monitoring, pressure protection, and temperature protection, which can promptly shut down the system in case of abnormal conditions to prevent safety incidents and ensure smooth production. Meanwhile, the maintainability of the burner is also crucial, facilitating daily inspections, cleaning, and maintenance by operators to reduce equipment downtime and improve production efficiency.
In summary, during the asphalt mixing process, the burner is responsible for providing thermal energy, ensuring efficient and clean fuel combustion, flexibly regulating heat output, and ensuring safe and stable production. It is an indispensable key piece of equipment in asphalt mixing plants, directly and significantly impacting the production quality and economic efficiency of asphalt mixtures.
Asphalt Plant Burner Performance Indicators
The performance indicators of burners are critical factors to consider when selecting burners for asphalt mixing plants, as they directly impact production efficiency and product quality. The following sections will detail several key performance indicators of burners.
Atomisation Particle Size
For heavy oil applications, the spray particle size of heavy oil should be controlled within 15μm to ensure optimal combustion efficiency.
Temperature Control Capability
Asphalt mixing plant burners must have excellent temperature control capability to maintain stable combustion temperatures and enhance production quality. Stable temperatures are a prerequisite for ensuring uniform quality of asphalt mixtures.
Fuel Flow Accuracy
Burners must precisely control fuel flow to ensure a stable fuel supply and prevent production issues caused by fuel flow fluctuations. Accurate fuel flow control ensures combustion stability and consistency.
Heat Output Stability
The heat output of heavy oil varies significantly, so the burner must be able to handle fluctuations in heat output to maintain combustion efficiency. Even if the fuel’s heat output changes, the burner can adjust accordingly to ensure that combustion performance is not significantly affected.
Heavy Oil Characteristics
For projects using heavy oil, special consideration must be given to the characteristics of heavy oil to ensure that the selected burner can effectively handle it.
The size of heavy oil mist particles must be controlled within an appropriate range to ensure complete combustion. Additionally, the burner must have excellent temperature control capabilities to ensure stable combustion temperatures. Fuel flow control must be precise to prevent production disruptions caused by fuel flow fluctuations. Furthermore, due to the significant variations in heavy oil calorific value, the burner must be capable of handling such fluctuations to maintain combustion efficiency.
Maintenance Tips for Asphalt Plant Burners
Since there are significant differences in burner designs among manufacturers, it is essential to carefully review the operating and maintenance manual for the specific burner model before performing any maintenance or adjustment operations. Whether it is the rotary mixer in a continuous mixing plant or the dryer in an intermittent mixing plant, the following general procedures must be followed when inspecting the burner:
Safety First
Before entering the maintenance work area, a complete lockout/tagout procedure must be performed, using specialized locks and tags to disconnect the equipment’s power and gas sources and posting warning signs at the control switches. Additionally, standard-compliant personal protective equipment (PPE) must be worn, including flame-resistant workwear, chemical-resistant gloves, safety goggles, and slip-resistant shoes. It is recommended to establish a dual-person mutual inspection mechanism, where two staff members confirm that safety measures are in place before commencing work.
Core Component Inspection
Filtration and Separation System: Remove the Y-type filter, fine filter, and moisture separator in sequence. Inspect the filter screens for blockages or damage, and use specialized cleaning agents to remove any accumulated impurities or oil residues. For preheaters, test the resistance values of the heating elements to ensure they meet standards and heating efficiency is adequate. Conduct opening and closing tests on all valves, inspecting valve core seals and the sensitivity of safety switches. Any abnormal delays or malfunctions must be documented.
Fuel Pipeline Inspection: Use an ultrasonic leak detector to scan the entire fuel pipeline system, focusing on joints, bends, and welded sections. For natural gas or propane pipelines, specialized gas detectors can be used to measure concentration levels. If a leak is detected, immediately use explosion-proof tools to tighten the connection and mark the damaged pipeline with a serial number. If the pipeline exhibits severe corrosion or cracks, measure the wall thickness according to standards. If it falls below the safety threshold, replacement is mandatory.
Comprehensive leak inspection: All pipes, fuel lines, and valves must undergo pressure testing by slowly increasing pressure to 1.5 times the rated working pressure, maintaining pressure for 30 minutes, and observing pressure drop. Simultaneously, fluorescent leak detection agents combined with ultraviolet lamps must be used to inspect areas difficult to observe visually, with detailed records of leak locations, severity, and corresponding component numbers.
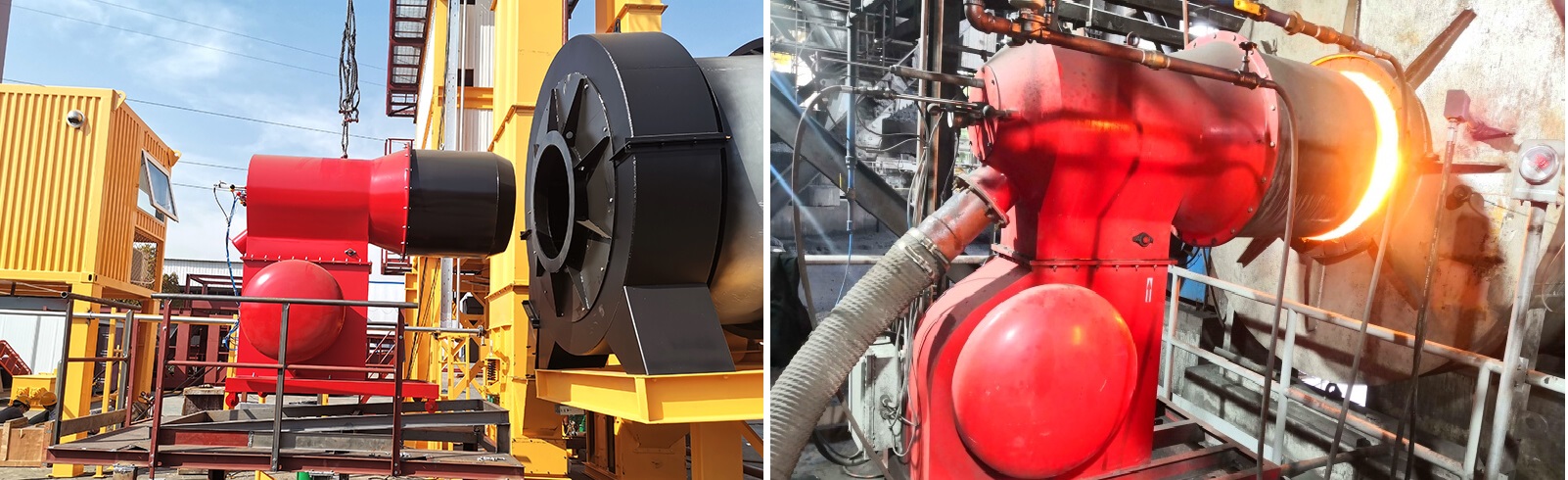
Performance Parameter Verification
Fuel pressure calibration: Use a high-precision pressure gauge to measure the fuel inlet pressure, and compare it with the pressure-flow curve chart provided by the manufacturer to ensure that the pressure value is within ±5% of the rated working range. If the pressure is abnormal, check the accuracy of the pressure reducing valve, pressure stabilizing device, and pressure gauge itself, and calibrate or replace them if necessary.
Critical Component Wear Assessment: Inspect the wear condition of the burner tube inner walls using an endoscope, measure the tube wall thickness, and compare it with the original design parameters. If wear exceeds 20%, replacement should be considered. Perform a 3D scan of the deflector blades of the conical device to analyze deformation. If deformation affects flame diffusion efficiency, repair or replacement is required.
Flame monitoring system testing: Simulate a cooling air system failure scenario to check if the flame monitor’s response time is within 0.5 seconds. Use an anemometer to measure the cooling air flow rate to ensure it meets the minimum design requirement, and inspect the air ducts for blockages or damage.
Recording and Follow-Up
Establish detailed maintenance records and classify issues using standardized fault codes (e.g., F01 indicates fuel leakage, W02 indicates component wear, etc.). Use a digital management system to synchronize inspection data in real time and generate visual maintenance reports. For major issues, organize interdepartmental meetings to develop repair plans and set staged follow-up milestones to ensure the repair process complies with quality management system requirements.
Conclusion
In summary, when selecting a burner for an asphalt mixing plant, it is essential to comprehensively consider key factors such as fuel availability and cost, environmental impact, operational efficiency, and maintenance. The selection of the burner should be aligned with operational objectives (cost, sustainability, flexibility), while thoroughly assessing long-term impacts (maintenance, regulations, etc.). Only by comprehensively considering these factors can the most suitable burner for your asphalt mixing plant be selected, ensuring smooth production operations and enhancing production efficiency.