In the field of road construction, the choice of asphalt batching mix plant directly affects engineering quality, cost control, and construction efficiency. As a technologically advanced production facility, the asphalt batching plant provides reliable assurance for high-demand engineering projects through its precise batch production model. This article will delve into the core advantages of investing in an asphalt batching plant, helping you understand why it can be a strategic choice for long-term development.
What is an Asphalt Batch Mix Plant?
An asphalt batch mix plant is a specialized piece of equipment that produces asphalt mix using a ‘batch production’ mode. Unlike continuous drum mixing plants, which operate non-stop, asphalt mixing plants primarily operate on a cyclical basis, allowing for precise adjustment of raw material ratios and temperature control for each batch.
This characteristic enables it to customize mixtures according to project requirements — for example, adjusting formulations for high-temperature stability on highways, load-bearing capacity on bridges, or fatigue resistance on airport runways. As a result, asphalt mixing plants are widely used in projects with stringent requirements for durability and performance, such as highways, bridges, and airports.
Its core components include a cold aggregate bin, drying drum, hot aggregate elevator, vibrating screen, hot aggregate bin, mixing tower, asphalt tank, dust collection system, and fully automatic control panel. These components work together to ensure efficient and precise production processes.
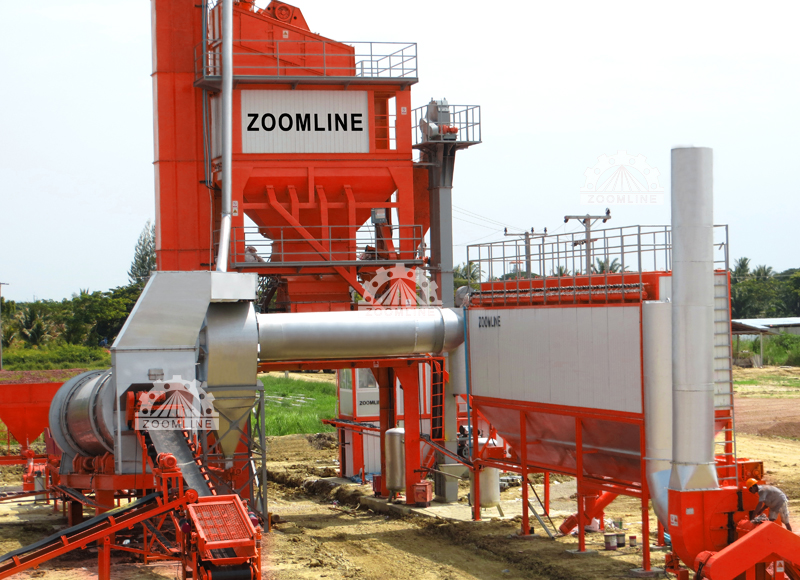
Benefits of Investing in Asphalt Batching Mix Plant
Significant improvement in operational efficiency
Traditional asphalt production technologies are inefficient and no longer meet the demands of modern engineering projects. The automated operating system of asphalt mixing plants fundamentally addresses this issue:
Reduced human intervention: Through the deep integration of PLC control systems and sensor networks, the automated system can precisely control aggregate ratios, temperature regulation, and mixing times. Take a certain expressway project as an example: after introducing the automated system, the gradation of asphalt mixture increased from 82% under manual operation to 98%, significantly reducing the risk of rework caused by human error and ensuring the stability of product quality.
Flexible production adjustments: The central control system, equipped with intelligent algorithms, can automatically optimize production parameters based on real-time construction progress, environmental temperature, and transportation distance. For example, during rainy season construction, the system can quickly adjust the drying drum temperature and mixing duration to prevent mixture segregation caused by excessive moisture content. When faced with different gradation requirements, the production mode can be switched with a single button, reducing changeover time from the traditional 30 minutes to just 5 minutes, significantly improving process efficiency.
Reduced reliance on human labour: The fully automated production line reduces the need for operators by over 60%. Through a human-machine collaboration model, only a small number of technicians trained to standardized procedures are required for monitoring and maintenance. This model not only alleviates the recruitment challenges posed by the shortage of skilled workers in the construction industry but also reduces unit labour costs by 40% by simplifying personnel management complexity, while minimizing production fluctuations caused by workforce turnover.
For companies seeking competitiveness, efficient operations mean faster project delivery speeds and lower unit costs, which are key to winning the market.
Wide applicability to meet diverse needs
The multi-functionality of asphalt mixing plants enables them to produce various types of asphalt mixtures, including hot-mix asphalt (HMA), warm-mix asphalt (WMA), and cold-mix asphalt (CMA). With precise proportioning control systems and intelligent temperature control technology, they can easily handle different scenarios:
Small-scale repair projects: In urban road maintenance, when faced with sudden potholes or cracks, the mixing plant can activate a rapid response mode. Through a modular batching system, it precisely adjusts the proportions of aggregates, asphalt, and additives, producing customized small-batch mixtures within two hours. For example, for community road repairs, it can produce low-noise warm-mix asphalt, reducing construction pollution while enabling immediate traffic access after paving.
Large-scale infrastructure projects: When serving highway and bridge construction, the mixing plant adopts a dual-unit collaborative operation mode, combined with an automated conveying system, achieving a production capacity of over 320 tonnes per hour. Through an intelligent monitoring system, the station tracks 12 key indicators in real-time, including the gradation stability and compaction of asphalt mixtures, ensuring that the continuously supplied high-specification asphalt fully complies with industry standards such as JTGF40-2004, providing a solid guarantee for engineering quality.
This flexibility not only reduces the company’s reliance on external suppliers but also enhances customer trust through comprehensive quality control throughout the entire process. Leveraging the technical advantages of the mixing plant, the company can undertake projects spanning the entire life-cycle, from municipal maintenance to national key projects, significantly expanding its business scope and profit margins.
Outstanding environmental performance, aligning with sustainable development trends
Modern asphalt mixing plants are designed with environmental requirements in mind, making them an ideal choice for green construction:
Advanced dust removal system: Utilizing multi-stage dust removal technology, the main dust removal equipment is equipped with pulse-jet bag-house dust collectors, achieving a filtration efficiency of up to 99.9%, effectively capturing dust particles larger than 0.3 microns. Combined with cyclone dust collectors for pre-treatment, this further reduces dust loads. Additionally, the system integrates odour purification devices, using activated carbon adsorption and photocatalytic oxidation technology to decompose irritating odours generated during production into harmless substances, achieving comprehensive control of dust, smoke, and odours.
Application of warm-mix technology: The introduction of warm-mix asphalt (WMA) technology, combined with the addition of special warm-mix additives or foam asphalt technology, reduces the production temperature of asphalt mixtures by 20-30°C. This not only reduces fuel consumption and emissions of greenhouse gases such as carbon dioxide and carbon monoxide but also improves the working environment, reducing the risk of construction personnel being exposed to high temperatures and harmful gases. Additionally, warm-mix asphalt mixtures have performance comparable to hot-mix materials, achieving energy conservation and emissions reduction while ensuring construction quality.
Compliance with Environmental Regulations: Equipment design strictly adheres to international and domestic environmental standards, such as China’s ‘Comprehensive Emission Standards for Air Pollutants’ and the EU EN 12627 standard. Through a real-time online monitoring system, emissions of particulate matter, sulphur dioxide, nitrogen oxides, and other pollutants are monitored 24/7 and connected to environmental protection department data platforms to ensure transparent and compliant emissions data. A comprehensive environmental management system effectively mitigates risks such as administrative penalties or project suspensions due to non-compliance with environmental standards.
In the global context of promoting low-carbon development, environmental performance has become an important bonus factor for companies participating in large-scale project tenders. Asphalt mixing plants equipped with advanced environmental protection technology not only help companies meet green construction requirements but also achieve a win-win situation of economic and environmental benefits by reducing energy consumption and emissions.
Support for recycled material utilization, cost-effective and environmentally friendly
Asphalt mixing plants, equipped with advanced hot recycling and warm mixing technologies, can efficiently utilise recycled asphalt pavement (RAP). They precisely blend milled materials from old road surfaces with new raw materials to produce asphalt mixtures that meet the quality standards of the national JTG F40-2004 ‘Technical Specifications for Asphalt Pavement Construction on Highways’. This feature offers multiple advantages:
Significantly reduces raw material costs: By optimizing the mixing ratio of recycled materials through an intelligent blending system, the use of new aggregates can be reduced by 30%-50%, and asphalt consumption by 15%-25%, while maintaining performance standards. Taking a mixing plant with an annual production capacity of 100,000 tonnes as an example, if the RAP content reaches 40%, annual savings on aggregate procurement costs exceed 2 million yuan, and asphalt procurement costs are reduced by over 1.5 million yuan.
Strongly promoting resource conservation: According to industry data, every 1 tonne of recycled material used is equivalent to saving 0.8 tonnes of new aggregate, 0.15 tonnes of asphalt, and 0.2 tonnes of fuel. This not only reduces excessive mining of natural sand and gravel quarries but also lowers the consumption of petroleum-based asphalt. Given the annual consumption of 2 billion tonnes of asphalt mixture nationwide, if the recycled material usage rate is increased to 30%, over 48 million tonnes of natural stone materials can be saved annually.
Effectively alleviating environmental pressure: Traditional landfill disposal of each tonne of old pavement materials occupies 0.5 cubic meters of land and poses a risk of asphalt soil contamination. Through recycling, each 10,000 tonnes of RAP processed at a mixing plant can reduce landfill space by 5,000 cubic meters and lower carbon dioxide equivalent emissions by 3,000 tonnes. Additionally, reducing aggregate extraction avoids ecological issues such as vegetation destruction and soil erosion.
For companies with long-term operations, the use of recycled materials can significantly increase profit margins. With a 10% reduction in operational costs, annual profits can increase by 8%–12%. More importantly, this initiative aligns with the ‘dual carbon’ strategy, helping companies establish a ‘green construction’ brand image, gain policy advantages in bidding processes, and enhance market competitiveness.
High production precision ensures engineering quality
The batch production mode of asphalt mixing plants relies on intelligent control systems and high-precision sensors to ensure that the ratio, temperature, and uniformity of each batch of mixed materials are strictly controlled:
Reduced material waste: The precise batching system, equipped with dynamic weight compensation devices, controls measurement errors for aggregates, asphalt, mineral powder, and other raw materials within ±0.5%. The system’s automatic calibration function continuously monitors material flow status, preventing overfeeding caused by pipeline blockages or measurement deviations. Compared to traditional mixing methods, this reduces raw material loss by 8%-12%, significantly cutting production costs.
Enhancing finished product performance: Using a twin-shaft forced-action mixer and multi-temperature zone heating technology, asphalt and aggregates achieve full coating within the optimal temperature range of 160-180°C, forming a stable asphalt binder structure. The finished mixture undergoes 12 performance tests, including Marshall stability and rutting dynamic stability, achieving a skid resistance value of BPN 65+ and residual stability exceeding 85%. This enables effective resistance to extreme conditions such as heavy traffic loads and freeze-thaw cycles, extending the design service life of roads from 10 years to over 15 years.
Reduced rework risk: The entire production process is equipped with an IoT monitoring system, generating a digital archive for each batch of mixture containing information such as mix design parameters, temperature curves, and mixing duration. In the event of quality fluctuations, the system immediately triggers an alert and automatically traces production data. Combined with a rapid laboratory testing mechanism, this reduces the response time for quality anomalies to within 30 minutes, significantly reducing rework caused by material defects such as pavement cracking and potholes. The overall project schedule can be accelerated by 15%-20%.
Engineering quality is the lifeline of a company, and the asphalt mixing plant is the core equipment ensuring quality.
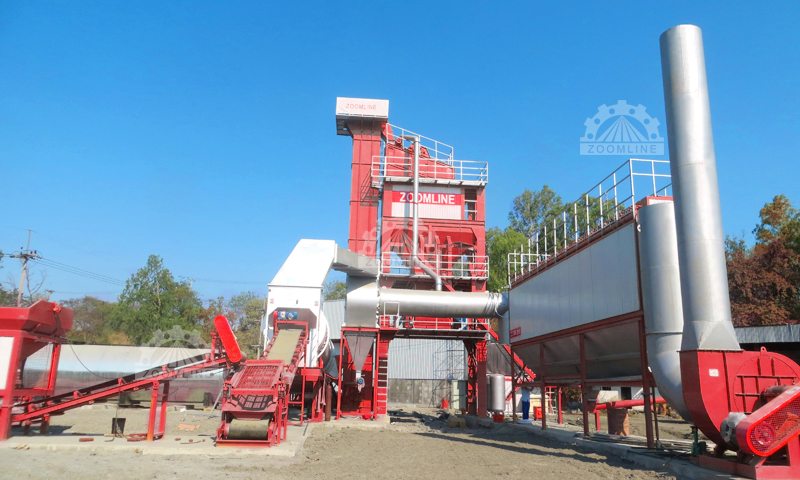
Comparison with Outsourcing Asphalt Supply
Many companies struggle with the decision of whether to build their own mixing station or outsource procurement. The following is a comparison based on key dimensions:
Core Differences Comparison Table
Comparison Item | Investment in asphalt mixing plant | Outsourced asphalt supply |
Initial Investment | Higher (equipment, site, personnel) | Lower (pay per tonne) |
Ongoing Costs | Maintenance, energy, labour, raw materials | Transportation costs, supplier mark-ups |
Quality Control | Highly controllable (customization mix) | Moderate (dependent on supplier) |
Flexibility | Produce on demand | Limited by supplier’s supply capacity |
Long-Term Value | Own assets, long-term cost savings | No assets, ongoing expenses |
From a financial perspective, the outsourcing procurement model only requires a one-time service fee in the initial stage, which can alleviate financial pressure. However, as the business expands, costs such as intermediary profits and transportation losses will continue to accumulate. On the other hand, while building an asphalt mixing plant requires a one-time investment in equipment, premises, and training, it allows for independent control over production, ensures the quality of asphalt mixtures, and enables flexible allocation of production capacity to reduce costs associated with project delays. Additionally, an in-house plant can undertake contract manufacturing services, leveraging economies of scale and diversified operations to reduce marginal costs. Within 3-5 years, this approach can establish cost and brand advantages, creating long-term value.
Types of asphalt mixing plants: Selecting the appropriate equipment
Batch-type asphalt mixing plant: Precise control, easy maintenance, flexible production volume, suitable for producing various types of mixes.
Mobile asphalt mixing plant: Easy to transfer between different construction sites, quick installation, compact design, suitable for projects requiring frequent relocation.
Fixed-type asphalt mixing plants: High production capacity, suitable for long-term operation at fixed locations, meeting large-scale and stable asphalt supply requirements.
Mixing plants with recycled asphalt pavement (RAP)/warm mix asphalt (WMA) technology: Specifically designed for recycled material utilization and low-emission production, aligning with environmental sustainability trends.
When selecting equipment, consider project scale, mobility requirements, and sustainability objectives.
Considerations Before Investing in an Asphalt Batching Mix Plant
Production demand assessment: Analyse the number, scale and type of projects and the required mix of materials to determine the appropriate production capacity.
Technical and functional considerations: Prioritize equipment with a high degree of automation, energy efficiency and advanced control systems.
Budget and financing: Take into account initial costs, maintenance expenses and long-term return on investment to explore suitable financing options.
Site Selection and Compliance: Ensure compliance with local environmental and safety regulations (e.g., ASTM, ISO standards).
Supplier Reputation: Select manufacturers with extensive experience, positive customer reviews, and robust after-sales support.
Conclusion
Investing in an asphalt mixing plant offers significant advantages in terms of efficiency, quality, and sustainability, which are crucial for engineering companies seeking long-term competitiveness. While outsourcing procurement is suitable for small-scale, short-term projects, investing in an asphalt mixing plant allows for complete control over production, cost savings, and flexible adaptation to market changes, making it a wise choice for long-term development.
Companies should assess their project requirements, thoroughly understand the characteristics of different types of mixing plants, and select reliable suppliers to maximize return on investment.
Frequently Asked Questions(FAQ)
Q: Is an asphalt batch mixing plant better than a drum mixing plant?
A: Both have their advantages. Asphalt mixing plants are suitable for projects requiring precise control and customized mixes; drum mixing plants are more efficient for continuous, large-scale production.
Q: How much recycled asphalt pavement (RAP) can modern asphalt mixing plants use?
A: Advanced equipment can use a significant amount of recycled asphalt pavement, with the proportion reaching over 30% in some cases, depending on project requirements and material characteristics.
Q: What is the typical payback period for an asphalt mixing plant?
A: Generally 2-5 years, depending on usage frequency, project scale, and cost control measures. Over the long term, the cost advantages of in-house production will gradually become evident.