Asphalt mixing plants are core equipment in road construction, responsible for producing the hot-mix asphalt (HMA) required for the construction of highways, urban roads, and infrastructure projects. However, not all asphalt mixing plants are the same. Two main types dominate the industry: batch mix asphalt mixing plants and continuous asphalt mixing plants.
Whether you are a contractor, project manager, or asphalt producer, understanding the differences between the two can impact whether a project is completed on time, meets quality standards, and keeps costs under control. In this guide, we will provide a detailed analysis of the working principles, core differences, advantages, and disadvantages of both types of plants, as well as how to select the appropriate type for your project.
What is a Batch Mix Asphalt Plant
Batch-type asphalt mixing plants are the most widely used type globally, renowned for their production flexibility and high precision in finished product quality. They operate on a “batch” production cycle, with each batch’s production time varying by type, typically producing a full batch of asphalt mixture every 40–50 seconds, with all raw materials individually weighed and measured.
This type of plant is an ideal choice for producers serving multiple clients simultaneously, as it can easily adjust production specifications to meet different needs while maintaining high quality.
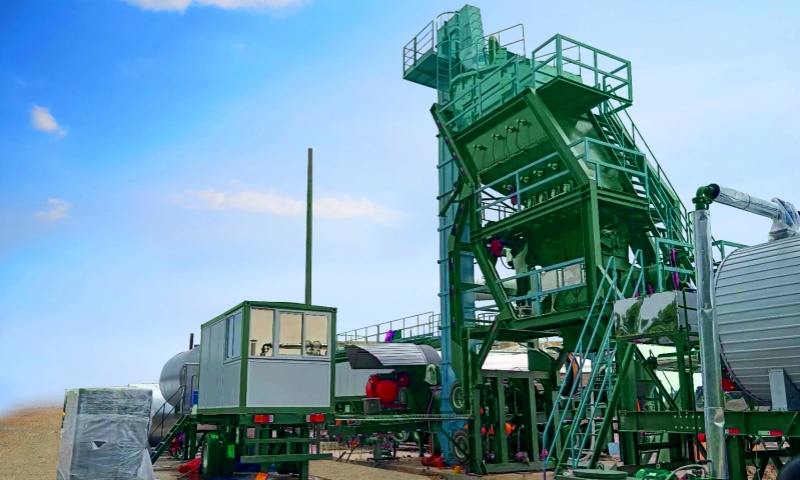
Core Components of a Batch Asphalt Mixing Plant
A batch asphalt mixing plant consists of several key components: the cold aggregate feeder stores and conveys raw cold aggregate; the drying drum heats the cold aggregate using a burner; the hot aggregate elevator transports the heated aggregate to the mixing tower; the vibrating screen separates the hot aggregate into different specifications, with the screened hot aggregate stored in the hot aggregate silo; the mixing tower contains a weighing hopper and mixing drum for final mixing; the asphalt tank is used for storing and supplying asphalt; the dust collection system employs a “gravity dust collector + baghouse dust collector” combination to reduce pollution; The advanced control panel enables fully automated operation of weighing, mixing, and production cycles.
How the Batch Mix Asphalt Plant Works?
- Cold aggregate supply: Cold aggregate from the cold aggregate silo is conveyed in an orderly manner via a conveyor belt to the drying drum, providing the raw material foundation for subsequent processing.
- Drying and heating: Within the drying drum, burners continuously supply heat while the drum rotates synchronously. The cold aggregate undergoes drying and heating processes under the combined effects of heat and rotation. Dust generated during this process is preliminarily filtered by the gravity dust collector to remove larger particles, followed by deep collection of finer particles by the baghouse dust collector, ensuring environmental protection.
- Screening and Weighing: After the hot aggregate is lifted into the mixing tower, it is precisely screened into different specifications by a vibrating screen. The weighing hopper strictly follows the mixing ratio requirements to accurately measure each specification of aggregate.
- Mixing: The weighed aggregate, along with the measured asphalt and filler, undergoes batch mixing in the mixing drum. The mixing cycle is typically controlled at 45 seconds to ensure a uniform and high-quality mixture.
- Storage and Unloading: The finished asphalt mixture can be temporarily stored in a storage silo as needed or directly unloaded into transport trucks for rapid transportation to the construction site.
What is a Continuous Asphalt Plant
The production process of a continuous asphalt mixing plant is uninterrupted, with production rhythms not divided into batches. Material mixing is completed within an extended drying drum, with drying and mixing occurring simultaneously.
Since no mixing tower or elevator is required, the system structure is significantly simplified, and maintenance costs are reduced accordingly. However, due to the absence of a vibrating screen, strict pre-control measures must be implemented before the production cycle begins, specifically before the aggregate enters the drying drum and before it is discharged from the drum as an asphalt mixture.
Core Components of a Continuous Asphalt Mixing Plant
The core components of a continuous asphalt mixing plant include a cold aggregate feeder for precise aggregate delivery; an extended drying drum combining drying, heating, and mixing functions; a burner providing a stable heat source for the heating process; an asphalt supply system ensuring precise asphalt metering and delivery; and a control panel enabling efficient continuous production through automated control.
How the Continuous Asphalt Mixing Plant Works?
- Cold aggregate feeding and preheating: Cold aggregate is conveyed into the counterflow drying drum via a belt conveyor or loader. The drum tilts and rotates, enabling the aggregate to move forward at a uniform speed. High-temperature hot air at 600-800°C inside the drum moves in the same direction as the aggregate, achieving rapid preliminary heating and enhancing heat exchange efficiency.
- Deep heating and dynamic mixing: The aggregate is heated to 140-170°C inside the drum. Precisely metered hot asphalt is sprayed in a mist form, and the continuous movement of the aggregate ensures uniform coating, avoiding local overheating or uneven mixing.
- Product output and intelligent control: The finished asphalt mixture is discharged from the end of the drum and conveyed to the storage silo or vehicle. The entire production process is monitored by an automated system, which uses temperature, weight, and flow sensors for real-time monitoring. In case of abnormalities, the system automatically adjusts the heat input, conveying speed, and spray volume to ensure production stability and consistent quality.
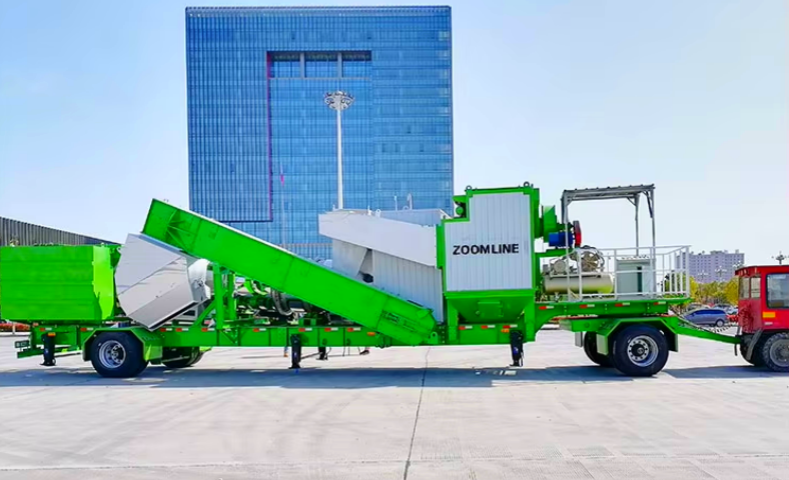
Key Differences Between Batch Mix Asphalt Plant and Continuous Asphalt Plant
Production Process
Batch-type asphalt mixing plants operate on a batch production model, completing a full production cycle every 40-50 seconds. Within each operational cycle, the system sequentially performs processes such as aggregate feeding, drying and heating, screening and weighing, asphalt and filler addition, and forced mixing. During batch transitions, the equipment pauses briefly to complete reset operations and parameter calibration. In contrast, continuous asphalt mixing plants adopt a fully continuous production process, where aggregates are fed into the drying drum via a continuously operating belt conveyor, simultaneously undergoing heating, screening, and mixing during the conveying process. Their production efficiency is 30%-50% higher than that of batch-type plants.
Weighing System
Batch-type asphalt mixing plants are equipped with high-precision electronic scales and dynamic weighing systems, enabling “precision weighing per batch” for aggregates, asphalt, and fillers, with measurement accuracy up to ±0.3%. This is particularly suitable for production requirements with high-precision mixing ratios, such as SBS modified asphalt. Continuous mixing plants adopt a combination of volumetric measurement and belt scales, achieving flow control by precisely regulating belt speed and material pile thickness, with measurement accuracy of approximately ±1.5%. This mode eliminates the secondary weighing step after drying, simplifying the process flow but imposing higher requirements on material uniformity.
Mixing Method
Batch-type mixing plants use double horizontal shaft forced-action mixing drums, where high-speed rotating blades achieve three-dimensional mixing of materials. Within a 45-second mixing cycle, asphalt coverage can reach over 98%. Continuous mixing plants use a drum-type mixing structure with built-in spiral scrapers and chain mechanisms. During aggregate conveying, drying, heating, and asphalt coating are performed simultaneously. The mixing time typically ranges from 120 to 150 seconds, with extended material residence time compensating for insufficient mixing intensity.
Equipment Structure
The batch-type mixing plant consists of over 30 core modules, including the mixing main building, vibrating screening system, hot material silo cluster, and high-precision weighing hopper, with a total equipment footprint of 2,000–3,000 square meters. Continuous mixing plants simplify hot material silos and screening systems, adopting an integrated “drying-mixing” drum design, reducing equipment volume by 40% and foundation construction costs by 25%, but imposing stricter requirements on aggregate particle size uniformity.
Formula Flexibility
Batch-type mixing plants utilize programmable logic controllers (PLCs) to enable real-time adjustment of all parameters, allowing for quick switching between ordinary asphalt and rubber asphalt within a single production batch. They support the production of over 20 types of asphalt concrete, including AC, SMA, and OGFC. Continuous mixing plants require process parameters to be pre-set via variable frequency drives and flow valves before production, with only ±10% ratio adjustments allowed during production, making them more suitable for continuous production of standardized pavement materials.
Application Scenarios
Batch-type mixing plants, with their high-precision mixing ratios and flexible production characteristics, are the preferred equipment for large-scale infrastructure projects such as highways and airport runways, with a daily output of 2,000–4,000 tons per unit. Continuous-type mixing plants, with their cost-effectiveness and continuous operation advantages, are widely used in small-to-medium-sized engineering projects such as rural roads and municipal roads, with a daily output typically ranging from 800–1,500 tons per unit.
Detailed Comparison of Metering Systems Between Batch Mix Asphalt Plant and Continuous Asphalt Plant
Aggregate Metering
The production cycle of both types of mixing plants begins with the feeding of cold materials, with aggregates typically measured by volume. For higher precision requirements, a belt scale can be installed on the aggregate extractor to achieve precise measurement. However, there are significant differences in the control of the total weight of raw aggregates between the two systems:
Continuous plants complete measurement using a feed belt scale before wet aggregate enters the drying drum. Since moisture content must be manually set to account for water weight, this method demands extremely stable moisture content in the aggregate (especially sand and gravel), necessitating frequent laboratory testing for real-time monitoring.
In contrast, batch plants perform weight measurement after aggregate drying and before it enters the mixing drum. Thanks to the design of the weighing hopper, the weighing process is not affected by variable factors such as moisture and weather, resulting in higher measurement accuracy. Additionally, the vibrating screen equipped in batch-type mixing plants enables precise screening of materials before mixing, ensuring the stability of finished product quality while effectively mitigating potential risks such as large aggregates entering the sand silo, fluctuations in aggregate supply, and errors in the pre-set formula of the cold material feeder. For this reason, industry standards in many countries explicitly stipulate that when quarries cannot meet the stringent control standards required for asphalt production, intermittent mixing plants must be used for production operations.
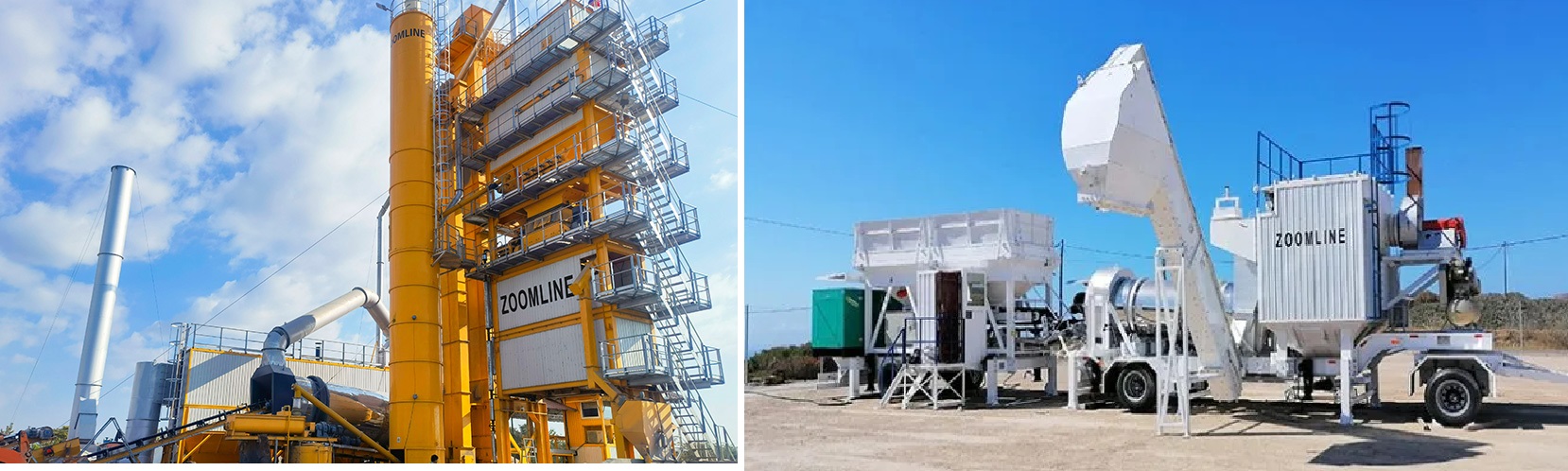
Bitumen Metering
Batch mix asphalt mixing plants rely on weighing sensors within the weighing hopper to precisely control asphalt usage through weight measurement. The computer system intelligently adjusts the amount of asphalt entering the mixing drum based on specification requirements and the actual weight of the aggregate, ensuring precise and error-free mixing ratios. Continuous mixing plants typically use volumetric measurement methods, with measurement completed via a flow meter after the feed pump. If modified asphalt is used, a mass flow meter can be installed, but regular cleaning and maintenance are required to ensure measurement accuracy.
Filler Metering
In batch-type mixing plants, fillers are measured by weight in a weighing hopper, enabling precise control of recycled fine materials and external fine materials. After measurement, the fillers are conveyed into the mixing drum via a dedicated screw conveyor or gravity conveying device, ensuring an efficient and accurate process. Continuous mixing plants typically use volumetric measurement systems, utilizing variable-speed feeding screws for aggregate conveyance. Compared to earlier pneumatic measurement systems, these offer significant improvements in stability and measurement accuracy.
Advantages of Batch Mix Asphalt Plant
Excellent Quality Control
High-precision electronic weighing systems and batch-type measurement modes are used to independently and precisely measure raw materials such as aggregates, asphalt, and mineral powder, with measurement errors controlled within ±0.5%. Combined with a stepwise mixing process, dry mixing first preheats the aggregates and coats them with mineral powder, followed by wet mixing to inject asphalt for thorough mixing. This ensures that the gradation uniformity and asphalt-to-aggregate ratio of each batch meet the highest industry standards, making it particularly suitable for projects with stringent quality requirements, such as airport runways and cross-sea bridges.
High Flexibility
Modular design and intelligent control systems enable rapid formula switching, allowing parameter adjustments for different gradations (e.g., AC-13 fine-grained, SMA-16 modified asphalt) to be completed within 30 minutes without stopping the equipment for cleaning. Ideal for comprehensive manufacturers serving multiple clients, it can handle large-scale continuous supply demands for highways while also flexibly responding to small-scale customized orders such as municipal road repairs, effectively enhancing equipment utilization and customer service capabilities.
Adapting to Environmental Changes
The innovative “dry first, then weigh” process eliminates the impact of fluctuations in aggregate moisture content on measurement accuracy. Even during the rainy season or in coastal high-humidity regions, dynamic compensation algorithms automatically adjust drying temperature and time, combined with a moisture-proof design for enclosed material silos, ensuring uninterrupted production throughout the process and maintaining stable output efficiency and quality standards.
Multifunctionality
The plant integrates hot mix, warm mix, and cold mix process modules. By adjusting asphalt heating temperatures, adding warm mix agents, or using emulsified asphalt, it can flexibly produce various types of asphalt mixtures. Hot mix technology is suitable for conventional road construction; warm mix technology reduces energy consumption and emissions, aligning with environmental project requirements; cold mix technology is used for emergency repairs, rural roads, and other special scenarios, achieving multi-functional production efficiency.
Advantages of Continuous Asphalt Plant
High-Efficiency Production
Continuous asphalt mixing plants adopt an uninterrupted production mode, achieving significant improvements in production efficiency through continuous material conveyance and continuous mixing processes. In scenarios with stable high-output demands, its hourly asphalt mixture output can be increased by 15%-25% compared to batch-type mixing plants. Calculated based on a 10-hour workday, continuous mixing plants can produce an additional 100-200 tons of asphalt mixture daily, making them particularly suitable for projects with tight schedules and large workloads.
Low Maintenance Costs
The equipment structure of this type of mixing plant is simplified, eliminating complex components such as vibrating screens, mixing towers, and elevators. This not only reduces equipment procurement costs but also decreases the frequency of replacing wear-prone parts during routine maintenance. Statistics show that the annual maintenance costs of continuous asphalt mixing plants are approximately 30% lower than those of intermittent plants, while significantly reducing downtime caused by equipment failures and improving overall equipment utilization.
Energy Efficiency
By simplifying the production process, continuous-type mixing plants avoid the energy consumption associated with frequent starts and stops in intermittent-type plants. During continuous operation, the equipment maintains a stable running state, minimizing unnecessary energy waste. In regions with high electricity costs, the energy-saving advantages of continuous-type mixing plants are particularly evident, leading to significant reductions in production costs over the long term.
Suitable for Simple Projects
For small to medium-sized projects with uniform construction standards and relatively simple specifications for asphalt mixtures, such as rural road renovations or residential area road paving, continuous asphalt mixing plants offer exceptional cost-effectiveness. These projects typically have short timelines and limited scope, and continuous mixing plants can efficiently complete production tasks, while their lower operational costs make the overall project cost more competitive.
How to Choose Between Batch Mix Asphalt Plant and Continuous Asphalt Plant
During the selection process, the following core dimensions can be considered in conjunction with the actual project requirements for comprehensive evaluation:
Production capacity
- Batch-type: Utilizes a batch production model, offering significant advantages in producing specific specifications of asphalt mixtures. It is suitable for medium to small-scale projects requiring frequent adjustments to the mix ratio, such as urban road renovations or community road upgrades. Such projects typically involve multiple pavement structures, and batch-type mixing plants can flexibly switch production formulas to precisely meet the needs of different construction phases.
- Continuous-type: Characterized by continuous, assembly-line-style production, it is better suited for large-scale projects with stable demand, such as highway network construction or pavement laying in large logistics parks. Its continuous material supply mode significantly increases production capacity, with some equipment achieving an hourly output of over 400 tons.
Flexibility and Customization
- Batch-type: If a project requires frequent adjustments to the mix ratio (e.g., serving multiple clients or multi-phase construction), the advantages of batch-type mixing plants are particularly evident. Their independent weighing and metering systems support rapid formula switching, such as switching from standard AC-type asphalt mix to SMA modified asphalt mix in just a few minutes, making them ideal for municipal projects with multiple sub-projects.
- Continuous: Suitable for single-specification production, it achieves constant raw material supply through pre-set mix ratio parameters. However, adjusting the mix ratio during production is challenging, making it more suitable for projects with fixed standards, such as factory roads or rural highways.
Energy Efficiency
- Batch-type: Due to frequent starts and stops, energy consumption per unit is relatively higher. However, modern equipment utilizes intelligent control systems to optimize heating and mixing processes, effectively reducing energy consumption.
- Continuous: By operating continuously, it reduces losses caused by equipment start-stop cycles. In long-term continuous production scenarios, its energy efficiency advantage is particularly evident.
Initial Investment and Operating Costs
- Batch: Due to its high technical integration and complex structure, the initial equipment procurement cost is typically higher. However, its precise production method helps improve engineering quality, and in the long term, it can reduce road maintenance costs.
- Continuous: Equipment investment is relatively low, with more cost-effective unit prices, making it suitable for projects with limited funding or those seeking rapid production. The simplified mechanical structure reduces the frequency of replacing wear parts, with maintenance costs approximately 30% lower than intermittent systems.
Quality Control
- Batch-type: For high-standard projects (such as airport runways, highways, etc.), batch-type mixing plants leverage precise weighing and batch control capabilities to keep measurement errors within ±0.5%. Through batch-by-batch testing, they ensure the finished material meets stringent standards.
- Continuous: Using dynamic measurement methods, it can meet the requirements of ordinary road construction, but during production, it is necessary to strengthen monitoring of key parameters to ensure the stability of the mixed material quality.
Environmental Impact
- Batch-type: Pollutant emissions are reduced through technical measures such as enclosed mixing chambers and dust collection devices, but the batch production mode may result in higher energy consumption per unit of output.
- Continuous: Relying on continuous operation and advanced control systems, it can achieve lower dust and exhaust emissions, making it particularly suitable for areas with strict environmental requirements.
Project Cycle
- Batch-type: Suitable for projects with short construction periods or frequent adjustments to mix ratios, it can be flexibly started and stopped according to daily construction plans, reducing losses caused by equipment idling.
- Continuous: The uninterrupted production mode is suitable for projects with long construction periods and high asphalt demand, enabling rapid completion of large-scale material supply tasks and effectively shortening the overall construction cycle.
Conclusion
Batch-type and continuous-type asphalt mixing plants each have their advantages. Batch-type plants excel in flexibility and quality control, making them suitable for diverse large-scale projects; continuous-type plants excel in efficiency and simplicity, making them suitable for medium-sized and small-scale projects with stable demand.
By comprehensively considering core factors such as project scale, technical specifications, investment budget, and operational costs, selecting the appropriate asphalt mixing plant equipment can not only significantly enhance production efficiency and ensure the quality of finished materials but also optimize resource allocation, laying a solid foundation for profitable project management throughout the entire lifecycle, ensuring efficient progress and successful completion of construction projects.