What Is an Asphalt Batch Plant
An asphalt batch mixing plant is the “core main equipment” for asphalt production, with batch production as its core logic. This production method first heats the aggregate, then mixes it with bitumen in batches, enabling precise control of the composition of the asphalt mixture, thereby producing finished products with stable quality and excellent performance. The equipment is equipped with a baghouse dust collector, effectively controlling pollutant emissions during the production process. Therefore, batch-type mixing plants are particularly suitable for medium to large-scale projects that require high flexibility and precision.
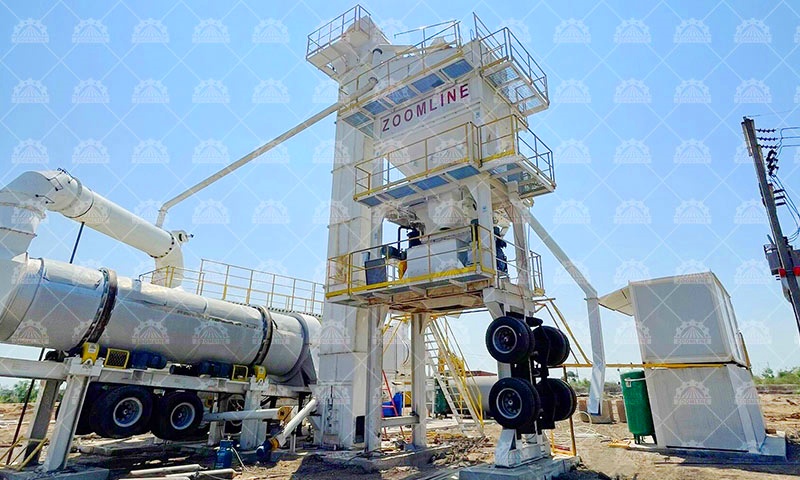
How Does Asphalt Batch Plant Work
- Aggregate feeding: Loaders transport aggregates of different particle sizes into the cold aggregate silos. Each silo is equipped with a variable frequency drive system to precisely regulate aggregate flow, ensuring accurate mixing ratios;
- Drying and heating: Raw materials are conveyed via a conveyor belt into a drying drum, where they are heated using energy-efficient burners fueled by diesel, heavy oil, or coal to completely remove moisture;
- Screening and storage: Heated aggregates are transported by a hot elevator to a vibrating screen, where they are graded by particle size and stored in hot bins for precise release as needed;
- Weighing and mixing: Aggregates from each hot storage silo are weighed and discharged according to pre-set ratios, then thoroughly mixed with heated asphalt and mineral powder in the mixing unit to ensure uniformity of the mixture;
- Finished Product Storage: The mixture can be stored in an insulated hot storage silo or directly loaded into vehicles to meet immediate construction needs.
What is Asphalt Drum Mix Plant
Asphalt drum mixing plants adopt a continuous production mode, breaking through the limitations of batch production. During operation, aggregates and asphalt are heated and mixed simultaneously in a rotating drum. Through a “one-step” process, asphalt mixture is continuously produced, making it more suitable for small and medium-sized projects with continuous feed requirements or standardized production scenarios.
How Does Asphalt Drum Mix Plant Work
The core advantage of asphalt drum mix plant lies in its “continuous integrated” production: after aggregates enter the rotating drum, asphalt binder is simultaneously injected, and the two are heated and mixed within the drum.
Through the continuous rotation of the drum, asphalt mixture is produced continuously, making it suitable for large-scale, standardized asphalt supply scenarios.

Detailed Comparison for Asphalt Batch Plant VS Drum Mix Plant
1. Production Efficiency
Drum-type asphalt mixing plants leverage their unique continuous production advantage to achieve efficient material output, with significantly higher output per unit time compared to batch-type mixing plants. In ultra-large-scale infrastructure projects with tight schedules and massive demand, drum-type asphalt mixing plants can provide continuous and stable material supply, making them an ideal choice for enhancing construction efficiency.
Asphalt batch mix plants, on the other hand, use a batch production model. While their overall production capacity is slightly lower, they excel in their ability to flexibly adjust production schedules. For medium-to-small-scale projects with fluctuating construction demands, batch-type asphalt mixing plants can adjust production according to actual progress, precisely matching project requirements and avoiding resource waste.
2. Mix Quality
Asphalt batch mix plants rely on a high-precision batch metering system to flexibly adjust mix formulas based on project characteristics. By precisely controlling core indicators such as gradation and oil-to-aggregate ratio, they achieve high consistency in the quality of each batch of finished products.
In contrast, the continuous production mode of drum-type mixing asphalt plants has inherent limitations, resulting in slow response times when adjusting mix parameters. In scenarios where production specifications are frequently switched, if equipment parameters cannot be promptly adapted, it is highly likely to cause fluctuations in finished product quality.
3. Environmental Impact
In the current context of increasingly stringent environmental protection requirements, the two types of equipment exhibit significant differences: asphalt batch plants are equipped with double-layer baghouse dust collectors, enabling secondary efficient dust removal, with particulate matter emissions far below national standards; asphalt drum mixing plants primarily use water-based dust removal technology, which not only has limited dust removal efficiency but also results in significant water consumption, leading to application restrictions in ecologically sensitive areas or regions with strict environmental inspections.
4. Cost Considerations
From a capital investment perspective, drum-type asphalt mixing plants, due to their simplified process flow, typically have equipment procurement costs 20%-30% lower than asphalt batch mix plants; while batch type asphalt mixing plants, which integrate high-precision metering systems and complex control systems, have higher initial investment costs.
However, from a lifecycle cost perspective, asphalt drum mix equipment offers cost advantages in large-scale continuous production scenarios due to its lower energy consumption and maintenance frequency; batch-type asphalt mixing plants, on the other hand, are better suited for high-value-added projects with extremely stringent quality requirements for finished products due to their stable high-quality output.
5. Flexibility and Adaptability
Batch-type asphalt mixing plants, with their exceptional process adaptability, can flexibly switch between hot mix, warm mix, and cold mix asphalt mixture production modes, and support customized production with different gradations and additive combinations, making them highly versatile in complex and variable construction scenarios.
In contrast, drum-type asphalt mixing plants are more suitable for continuous production of a single specification on a large scale. In scenarios requiring frequent adjustments to formulas or process parameters, the equipment’s conversion efficiency and production stability will face significant challenges.
Component-Level Differences Between an Asphalt Batch Plant and a Drum Mix Plant
1. Cold Material System
- Asphalt batch plant: Utilizes electronic scales for precise measurement, supports multi-batch feeding, and keeps aggregate mix ratio errors strictly within ±1%, suitable for scenarios with high precision requirements.
- Drum mix plant: Uses a one-time feeding design, unable to dynamically adjust material quantities during operation, resulting in insufficient mixing precision and significant errors, making it more suitable for projects with lower precision requirements.
Selection Recommendations: If strict precision is required or flexible adjustments are needed, the batch-type asphalt plant is preferable; if feeding convenience is prioritized and precision requirements are lower, the drum-type asphalt plant can be considered.
2. Dust Collection System
- Asphalt batch plant: Equipped with a high-power exhaust fan and an efficient bag-type dust collector, achieving dust capture efficiency of over 99%, meeting stringent environmental standards with outstanding environmental performance.
- Drum mix plant: Generally uses water-based dust collection technology, which not only has low dust collection efficiency but also consumes 5–10 cubic meters of water per hour, resulting in severe water resource waste and poor environmental performance.
Selection recommendation: In the current environment of increasingly stringent environmental requirements, selecting a high-efficiency dust collection system can significantly reduce environmental pollution, with the batch type asphalt plants better aligning with green production needs.
3. Weighing System
- Asphalt batch plant: Equipped with a high-precision electronic weighing system, it enables real-time precise control of asphalt usage, with oil-to-aggregate ratio errors controlled within ≤0.5%, ensuring stable product quality.
- Drummix plant: Due to the lack of specialized weighing equipment, asphalt addition primarily relies on time control, making precise management difficult, with oil-to-aggregate ratio errors reaching ±3%.
Selection Recommendation: Production precision is key to ensuring asphalt concrete quality. If high-quality finished products are required, the asphalt batch mix plant system with a precise weighing system is a more worthwhile choice.
4. Heating and Mixing System
- Asphalt batch plant: Aggregate heating and mixture mixing are performed separately, allowing flexible and convenient temperature control to ensure uniform heating of the mixture and effectively prevent asphalt aging.
- Drummix plant: Heating and mixing are performed simultaneously within the same drum, resulting in insufficient temperature control precision. High-temperature environments may cause asphalt aging, affecting the final performance of the mixture.
Selection Recommendations: Temperature control during production significantly impacts asphalt concrete quality. Select an appropriate heating system based on actual requirements to ensure finished product performance.
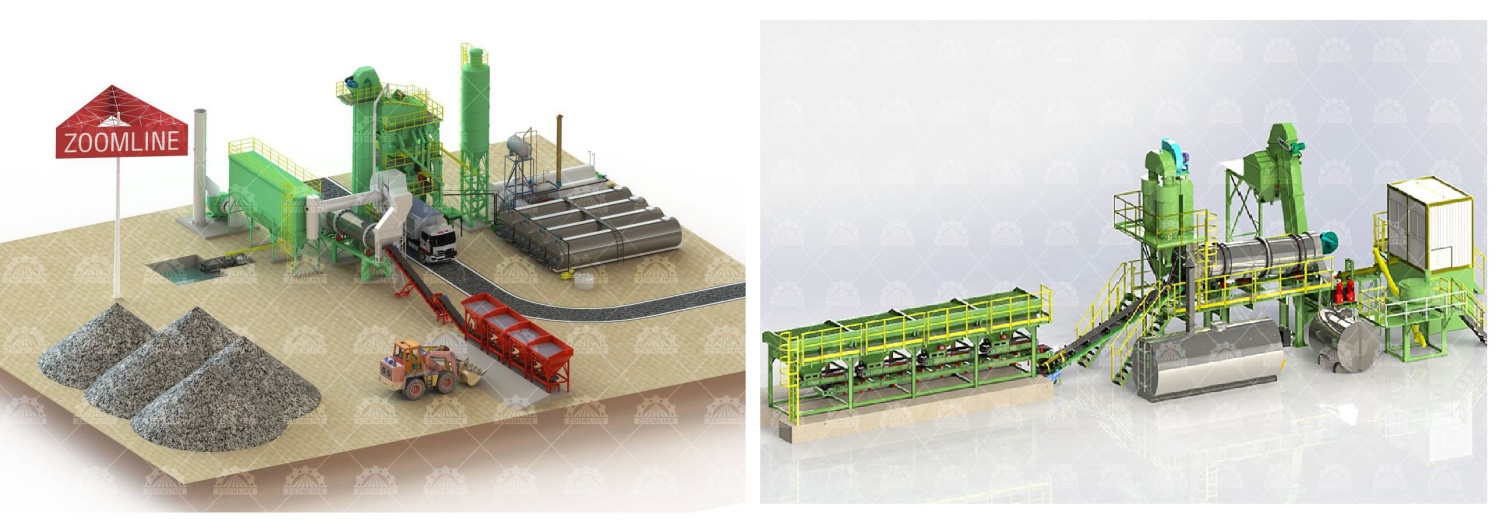
5. Finished Material Conveyance Method
- Asphalt batch plant: Uses pneumatic flip-gate control for conveyance, offering fast conveyance speed and excellent insulation performance to maintain finished material temperature.
- Drummix plant: Finished materials must be transported to an external finished material storage area. During transportation, insulation performance is poor, and transportation time is relatively long, which may affect the quality of finished materials.
Selection Recommendations: When selecting a finished material transportation method, both transportation speed and insulation performance must be comprehensively considered to ensure that the quality of finished materials is not affected.
6. Bitumen Heating System
- Asphalt batch plant: Uses thermal oil heating, with high thermal efficiency, more suitable for large-scale batch production, effectively improving production efficiency.
- Drum mix plant: The heating furnace is integrated with the asphalt system, with lower thermal efficiency, more suitable for small-scale production scenarios.
Selection recommendations: An appropriate asphalt heating system can enhance production efficiency and reduce energy costs; selection should be based on production scale.
7. Asphalt Burner
- Asphalt batch plant: The burner is easy to operate, emits minimal smoke during operation, and has good environmental performance.
- Drummix plant: It consumes a large amount of fuel, emits more smoke, and has higher maintenance costs.
Selection Recommendations: The combustion efficiency and environmental performance of the equipment are important selection criteria. While ensuring production, environmental impact and operational costs must also be considered.
From the differences in the above components, it is evident that asphalt batch mixing plants have clear advantages in terms of precision, environmental performance, and quality control, while drum-type mixing plants are more competitive in simplifying processes and reducing initial costs. These technical differences directly impact the actual performance of the equipment and provide important references for scientific selection based on specific project requirements.
Advantages of Asphalt Batch Plant
- Flexible Formula Adaptation: Asphalt batchmixing plants demonstrate unparalleled flexibility in formula adjustment, enabling rapid switching between mix formulas. Whether it is the demand for wear resistance and anti-skid performance in urban road construction, or the stringent requirements for high-temperature stability and fatigue resistance in airport runway engineering, they can be precisely adapted.
- Comprehensive Quality Control: By strictly monitoring every batch of asphalt mixture production throughout the process, from raw material ratios to mixing time and temperature control, each step is precisely managed. This ensures high consistency in the performance metrics of asphalt mixtures, producing consistently high-quality asphalt products. This lays a solid foundation for high-grade road projects such as highways and bridges that demand the highest quality standards.
- Cost-effective and Economical: For projects with significant fluctuations in asphalt demand, asphalt batchmixing plants offer significant advantages in cost control. Their production capacity can be flexibly adjusted according to actual needs, whether it be small-scale trial paving in the early stages of a project or large-scale supply during peak construction periods. This allows for optimal resource allocation, avoiding cost wastage caused by equipment idleness or insufficient capacity, and achieving efficient utilization of project costs.
- Diverse and Compatible Processes: Supports multiple production processes such as hot mixing, warm mixing, and cold mixing. This multifunctionality greatly expands the application boundaries of asphalt mixtures, making them suitable not only for conventional road paving but also for special engineering scenarios such as road construction in cold regions and tunnel paving, meeting the needs of various complex engineering projects.
- Wide Range of Application Scenarios: Batch-type asphaltmixing plants are an ideal choice for medium to large-scale projects with stringent quality requirements and frequent formula adjustments. In municipal road renovation projects, formulas can be flexibly adjusted according to traffic flow and usage requirements on different road sections; during bridge construction, they ensure the quality stability of asphalt mixtures under complex stress conditions; and in urban expressway construction, strict quality control ensures the smoothness and durability of the pavement.
Advantages of Drum Mix Plant
- High-efficiency Continuous Operation: The drum-type asphalt mixing plant adopts a continuous production mode, enabling uninterrupted material supply. For projects with high asphalt demand, such as highway construction and large-scale infrastructure projects, this continuous and stable material supply capability can fully ensure construction progress, making it an ideal choice for large-scale projects. Its continuous mixing process not only ensures the consistency of asphalt quality but also significantly improves production efficiency.
- Significant Energy Savings and Reduced Consumption: Compared to asphalt batchmixing plants, drum-type asphalt mixing plants feature an innovative design that eliminates the need for batch heating. This improvement significantly reduces energy consumption, as there is no need to reheat aggregates for each batch. From a long-term operational perspective, this energy-saving advantage effectively controls costs and saves companies a significant amount of money.
- Convenient and Hassle-free Operation and Maintenance: Drum-type mixing plants have a simple structure and require minimal manpower for operation and maintenance, effectively reducing labor costs. Even in remote construction sites or areas with limited manpower, they can operate stably, significantly reducing operational pressure and making construction projects more hassle-free.
- Suitable for Remote Areas: The drum-type asphalt mixing plant, with its continuous operation capability and simple design, is highly adaptable to remote construction sites with limited resource access. In projects such as mountain road construction in areas with poor transportation and difficult material transportation, or infrastructure development on islands, its ability to operate stably without frequent adjustments is fully demonstrated, ensuring construction progress and quality.
How To Choose The Right Asphalt Plant
1. Project Scale and Demand Characteristics
- Medium to large-scale complex projects: such as urban expressway renovations or bridge construction involving multiple sections and structural layers, often requiring frequent adjustments to asphalt mixture gradation and additive ratios. Batch-type asphalt mixing plants, equipped with batch metering systems, enable independent weighing and precise blending of aggregates, asphalt, and powder materials. They are particularly suitable for complex conditions requiring special formulations such as SBS modified asphalt or fiber-reinforced mixtures, and can quickly respond to design changes and on-site demand adjustments.
- Large-scale continuous projects: For long-term projects with concentrated workloads, such as new highway construction or airport runway paving, drum-type mixing plants can achieve a stable production capacity of 200–400 tons per hour through continuous production. Their integrated ring-shaped drying and mixing design reduces efficiency losses caused by equipment startup and shutdown, ensuring a continuous supply of material to paving machines and avoiding construction cold joints caused by supply interruptions.
2. Production Efficiency Adaptation Solutions
- Emergency schedule scenarios: For projects with stringent schedule requirements, such as emergency road repairs for disaster relief or road construction for major events, drum-type asphalt mixing plants can operate continuously around the clock. With a dual-unit configuration, daily production capacity can exceed 4,000 tons. Their automated control systems reduce manual intervention, lower operational risks during nighttime construction, and significantly shorten project timelines.
- Phased construction needs: For projects with flexible schedules, such as segmented municipal road renovations or phased rural road construction, asphaltbatching plants support “on-demand” modular production. Through PLC intelligent control systems, batch output and production intervals can be adjusted as needed to avoid energy waste from idle equipment, while meeting the material supply rhythm for alternating construction across multiple workfaces.
3. Quality Control and Cost Balance
- High-precision construction standards: In the construction of high-grade asphalt pavements (such as OGFC drainage asphalt and SMA asphalt mastic gravel), the dynamic weighing error of the batch type asphaltmixing plant can be controlled within ±0.5%, ensuring the accuracy of asphalt content and mineral powder ratio. In conjunction with an infrared temperature monitoring system, the drying temperature can be adjusted in real-time to prevent asphalt aging, resulting in finished material uniformity and stability far exceeding industry standards, effectively enhancing the pavement’s skid resistance and rutting resistance.
- Cost-effective project selection: For cost-sensitive projects such as ordinary municipal roads and industrial park roads, drum-type asphalt mixing plants offer lower energy costs (approximately 15% reduction in energy consumption per unit) and the advantage of large-scale production. While meeting regulatory requirements, they significantly reduce the production cost per cubic meter of mixed material. Their simplified mixing process reduces equipment maintenance frequency, further cutting operational expenses.
4. Full Lifecycle Cost Analysis
- Initial Budget Constraints: Drum-type mixing plants have equipment procurement costs 20%-30% lower than asphalt batch-type plants, with simpler infrastructure requirements that do not necessitate complex material silos or metering systems. They are suitable for small and medium-sized construction companies or projects with tight cash flow constraints. Taking a common 2000-type unit as an example, initial investment savings of approximately 800,000 to 1,200,000 yuan can be achieved, lowering the project startup threshold.
- Long-term benefits: Although batch-type asphalt mixing plants require higher initial investment, they reduce waste generation through precise mixing ratios (waste rate below 1%), extend road lifespan by 3-5 years, and lower post-construction maintenance costs. In large-scale projects, by reducing rework and quality risks, the total lifecycle cost can be reduced by 15%-20%, making them more suitable for investors prioritizing quality and long-term returns.
5. Environmental and Site Adaptability
- Environmental Sensitive Areas: When constructing in urban core areas or near residential zones, asphaltbatching plants equipped with pulse bag dust collectors and asphalt smoke adsorption devices can control dust emissions below 20 mg/m³ and achieve over 95% asphalt smoke purification efficiency, complying with the “Comprehensive Emission Standards for Air Pollutants.” Closed material silos and noise-reduction designs effectively reduce dust and noise pollution, minimizing the risk of construction-related disturbances to nearby residents.
- Remote construction environments: Drum-type asphalt mixing plants feature a compact structure and are easy to disassemble and transport, making them suitable for relocation needs in mountainous or high-altitude regions with poor transportation infrastructure. Their modular design facilitates rapid maintenance, and core components (such as burners and mixing blades) have extended maintenance cycles. When combined with a simple aggregate conveying system, they can be quickly commissioned in sites lacking supporting facilities, ensuring the smooth progress of projects in remote areas.
6. Technical Service Support System
Regardless of the final selection, the supplier’s technical support capabilities are a key consideration. It is essential to assess the response speed and professional level of their services, including equipment commissioning, regular maintenance, and system upgrades, to ensure the stability and longevity of the equipment.
Conclusion
There is no absolute superiority between asphalt batching plants and drum-type mixing plants; their value lies in their adaptability to specific application scenarios. Asphalt batch plants excel in “precision and flexibility” for mid-to-high-end projects, while drum mix plants offer “high efficiency and cost-effectiveness” for large-scale standardized production. Engineering professionals must comprehensively evaluate equipment performance based on project requirements, quality standards, environmental regulations, and cost planning to maximize production efficiency and economic benefits.