What is an Asphalt Batch Mix Plant
An asphalt batch mix plant is an advanced piece of equipment that produces precisely proportioned asphalt mixtures through a cyclical production process. Unlike continuous drum mixing plants, its batch-measured characteristics provide an absolute advantage in mix quality control — from highways to airport runways, from bridge projects to high-traffic municipal roads, contractors can customize mix properties such as high-temperature resistance, load-bearing capacity, and noise reduction performance according to project requirements. This customized production capability makes it the preferred equipment for infrastructure projects with stringent durability requirements.
Key Components of Asphalt Batch Mix Plant
Cold Aggregate Feeder
As the starting point of the production process, the cold material supply machine is responsible for storing and conveying aggregates of different particle sizes. Its adjustable gates enable precise flow control, ensuring that aggregates of various specifications enter subsequent processing stages in the designed proportions. Independent gear-driven motors for each hopper allow for independent speed adjustment, laying a solid foundation for achieving precise mix gradation.
Drying Drum
The drying drum is the core equipment for removing moisture from aggregates, with a burner system on one side providing a stable heat source. The inclined drum design, combined with internal agitation plates, ensures that aggregates are heated uniformly during rotation. Strict control of drying temperature (typically maintained at 160-180°C) and processing time is crucial to prevent insufficient mix strength caused by residual moisture.
Hot Elevator
The dried aggregate is transported by the hot material elevator to the vibrating screen at the top of the tower. The multi-layer screening device achieves precise particle size classification through high-frequency vibration. Particles exceeding the specified size are automatically removed, while qualified aggregate is temporarily stored in the hot material silo, ensuring that the aggregate gradation of the mixture fully complies with design standards.
Mixing Unit
The mixing unit is the “heart” of mixture preparation. The twin-shaft mixer thoroughly blends heated aggregates, asphalt, and additives through high-speed rotation. The jacket design of the mixing drum effectively maintains internal temperature, preventing asphalt from thickening due to cooling and affecting mixing uniformity. The typical mixing cycle is controlled between 45–60 seconds.
Bitumen Storage Tanks
The asphalt storage tank features a specialized insulation design and can be heated via direct combustion or indirect heating through a hot oil circulation system, ensuring the asphalt remains in an optimal flow state. A precise temperature control system effectively prevents asphalt from solidifying or overheating and degrading, thereby ensuring ideal adhesion performance between the asphalt and aggregates.
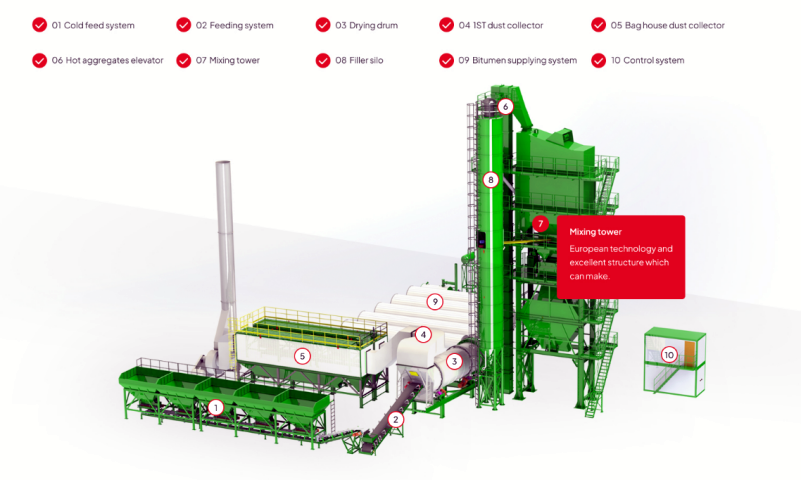
Asphalt Batch Mix Plant Process in Detail
Cold Material Feeding
In the production process of an asphalt batch mixing plant, cold material feeding serves as the initial stage, and its precision directly impacts the quality of the final product. Aggregates of different particle sizes are fed into separate cold material silos according to design gradation requirements. Each silo is equipped with a variable-frequency speed-regulated motor, which adjusts the speed in real-time via a PLC control system to dynamically control the feeding rate of aggregates. Taking the 2000-type mixing plant as an example, by optimizing the matching algorithm between the cold material silo gate opening and motor speed, combined with high-precision belt scales for flow monitoring, the aggregate gradation error of each batch of mixed material can be stably controlled within ±2%. Additionally, the system’s built-in anti-cross-contamination partitions and vibration arch-breaking devices effectively prevent aggregate segregation and silo blockages.
Aggregate Drying and Heating by Drying Drum
After cold material is discharged, the aggregate is conveyed via a belt conveyor into the drying drum. The drum adopts a counterflow heat exchange design, with alternately arranged material-lifting plates uniformly dispersing the aggregate to fully contact the high-temperature gas flow (1000-1200°C) generated by the burner. Infrared moisture sensors continuously monitor the moisture content of the discharged material. When the moisture content drops below 0.5%, the system automatically adjusts the burner power to ensure the optimal balance between drying efficiency and energy consumption. Notably, the temperature gradient control technology introduced during the drying process prevents physical property damage caused by localized overheating of the aggregate, laying the foundation for subsequent production processes.
Hot Material Conveying and Screening
The dried aggregate is vertically conveyed by a bucket elevator to the vibrating screening system. This system is equipped with multi-layer stainless steel screens to precisely classify the aggregate based on particle size ranges (e.g., 4.75 mm, 9.5 mm, 16 mm, etc.). The screened aggregate is distributed via pneumatic diverters into corresponding hot material silos. Each hot material silo is fitted with high-precision load cells at the bottom, combined with level sensors on the silo walls, to achieve dual monitoring of aggregate inventory and flow rate. This design not only provides precise weight data for subsequent batching but also employs dynamic compensation algorithms to real-time correct measurement errors caused by thermal expansion and contraction, effectively preventing gradation fluctuations.
Bitumen and Filler Measurement
The bitumen measurement system adopts a double-layer insulated weighing hopper structure, combined with a heating jacket and temperature sensors, to ensure that the asphalt maintains its flowability at the optimal working temperature of 150-170°C. Mineral fillers are uniformly conveyed by a screw conveyor to an independent weighing hopper, with the conveying speed and measurement accuracy controlled by a variable frequency drive and a loss-in-weight scale. Given the critical impact of the oil-to-stone ratio (asphalt-to-aggregate mass ratio) on mixture performance, the measurement system is equipped with an automatic calibration program that periodically verifies errors using standard weights, enhancing oil-to-stone ratio control accuracy to ±0.3%. Additionally, the system integrates anti-drip asphalt valves and filler sealing devices to effectively reduce material loss and environmental pollution.
Mixture Mixing
In the mixing unit, hot materials, bitumen, and fillers are precisely dispensed according to the pre-set formula. If recycled asphalt pavement (RAP) materials are incorporated, they are controlled via an independent metering and conveying system to ensure the recycled material ratio meets design requirements. The mixing main unit adopts a dual-shaft forced-action structure with wear-resistant alloy blades. By optimizing the mixing paddle angle and speed, the mixture achieves uniform mixing within 45–60 seconds. After mixing is complete, the discharge door is rapidly opened via hydraulic drive, conveying the finished material maintained at a temperature of 150-170°C to transport trucks or storage silos. During this process, an infrared temperature sensor installed at the discharge port continuously monitors material temperature. If the temperature deviates from the set range, the system automatically alarms and adjusts the drying heating parameters.
Bitumen Storage and Conveyance
Bitumen storage tanks are divided into two types: direct heating and indirect heating. Direct heating tanks use burners to directly heat the asphalt, resulting in rapid temperature increases but posing a risk of localized overheating; indirect heating tanks utilize a hot oil circulation system for indirect heating, ensuring more uniform temperature distribution and suitability for storing high-quality asphalt sensitive to temperature fluctuations. Asphalt in the storage tanks is precisely conveyed via pipelines and pumping systems to weighing hoppers and mixing units. During conveyance, asphalt temperature and flow rate must be strictly controlled to ensure stable performance.
Filler Storage
Filler storage silos are used to store mineral fillers, which are conveyed to the weighing hopper via a screw conveyor. The storage quantity of fillers must be monitored and replenished according to the production plan to ensure continuous production. Additionally, precautions must be taken to prevent moisture and contamination of the fillers to avoid quality issues that could affect the performance of the asphalt mixture.
Pollution Control
Baghouse dust collectors and pre-separators are the core equipment for pollution control in asphalt mixing plants. The pre-separator first removes heavy dust, reducing the load on subsequent dust collection equipment; the baghouse dust collector efficiently filters harmful gases and fine dust through internal filter bags. This combined dust collection system ensures that emitted flue gas meets strict environmental standards, minimizing environmental pollution. For example, in today’s increasingly stringent environmental requirements, dust collection equipment compliant with national standards is an essential condition for the normal operation of a mixing plant.
Control Panel
The PLC control panel and touchscreen human-machine interface (HMI) form the control system of the asphalt mixing plant. Operators can monitor and adjust the operating parameters of each production process in real time through the control panel, such as temperature, speed, and weight. The advanced control system also features fault diagnosis and early warning functions. If any abnormalities occur in the equipment, the system will promptly issue an alarm and provide solutions to ensure safe and efficient production operations.
Additional Process Variations for Asphalt Batch Mix Plant Process
Application of Recycled Materials (RAP Integration)
By incorporating 10%-30% recycled asphalt pavement material (RAP), dual benefits are achieved: reducing raw material costs by 15%-25% while significantly reducing construction waste emissions. The mixing plant is equipped with an intelligent RAP metering system to precisely control heating temperatures and prevent asphalt aging. Optimized mixing sequence algorithms ensure uniform blending of new and old materials, maintaining the stability of finished product quality.
Additive Technology Innovation
By adding high-performance polymers such as styrene-butadiene-styrene block copolymers (SBS), the crack resistance of asphalt mixtures is improved by over 30%, significantly extending the service life of the pavement.
Warm Mix Technology
Using a new type of warm mix agent, production temperatures can be reduced by 10-40°C, achieving 15%-20% energy savings while simultaneously reducing greenhouse gas emissions. This improves the construction environment while reducing workers’ labor intensity.
Key Performance Advantages of Asphalt Batch Mix Plant
High-Precision Proportioning Control
Using an independent batch metering system, precise control of gradation and oil-to-aggregate ratio is achieved, completely eliminating the risk of parameter fluctuations in continuous production. Practical verification shows that the qualified rate of the mixture remains stable at over 99%, laying a reliable foundation for engineering quality.
Flexible Customization Capability
Tailored to different engineering scenarios, such as the high load-bearing requirements of airport runways or the noise-reduction characteristics of urban roads, production formulas can be quickly and flexibly adjusted. Compared to traditional continuous equipment, it demonstrates significant advantages in adapting to complex operating conditions.
Energy Efficiency Optimization
Equipped with advanced modern burners combined with efficient insulation technology, fuel consumption is effectively reduced. Some high-end equipment integrates a waste heat recovery system, further enhancing energy utilization efficiency and achieving a 10%-15% increase in energy efficiency.
Pollution Control
Baghouse dust collectors and pre-separators are the core equipment for pollution control in asphalt mixing plants. The pre-separator first removes heavy dust, reducing the load on subsequent dust collection equipment; the baghouse dust collector efficiently filters harmful gases and fine dust through internal filter bags. This combined dust collection system ensures that emitted flue gas meets strict environmental standards, minimizing environmental pollution. For example, in today’s increasingly stringent environmental requirements, dust collection equipment compliant with national standards is an essential condition for the normal operation of a mixing plant.
Automation and Intelligence Upgrades
The PLC control panel and touchscreen human-machine interface (HMI) form the control system of the asphalt mixing plant. Operators can monitor and adjust the operating parameters of each production process in real time through the control panel, such as temperature, speed, and weight. The advanced control system also features fault diagnosis and early warning functions. If any abnormalities occur in the equipment, the system will promptly issue an alarm and provide solutions to ensure safe and efficient production operations.
Equipped with a PLC intelligent control system, enabling real-time dynamic monitoring of production data. Supports remote fault diagnosis functionality, significantly reducing manual intervention and lowering operational errors by over 60%, thereby markedly improving production management efficiency and stability.
Tips to Optimize Operation Efficiency
Precise Process Control
Real-time adjustment of aggregate flow rate, drying temperature, and mixing time via the HMI interface. Taking the 2000-type equipment as an example, reducing the mixing cycle by 5 seconds (from 50 seconds to 45 seconds) increases hourly output from 144 tons to 160 tons, demonstrating significant capacity optimization.
Preventive Maintenance System
- Daily Maintenance: Inspect conveyor belt tension, motor operation status, and lubricate all transmission components;
- Weekly maintenance: Clean accumulated material from the vibrating screen mesh and hot material silo walls, and test burner flame stability;
- Monthly maintenance: Calibrate the asphalt and filler weighing system, and check the pulse cleaning pressure of the baghouse dust collector;
- Annual maintenance: Replace mixing arm liners and drying drum refractory materials, and conduct a comprehensive inspection of the control system.
Quality Assurance Measures
Establish a batch testing system: Sample each batch of mixed material for gradation screening, oil-to-stone ratio testing, and Marshall stability testing to ensure compliance with design standards.
Environmental Compliance Management
Regularly replace damaged filter bags to control dust emission concentration ≤30 mg/m³; use low-sulfur fuel and warm-mix technology to reduce nitrogen oxide emissions by 15%-20%.
Analysis of Common Faults in Asphalt Mixing Plants
Insufficient Capacity and Unstable Output
Imbalanced Mix Proportion: Overflow or material shortage in a specific aggregate silo causes frequent interruptions in the mixing process. For example, during highway project construction, due to insufficient capacity design of the 4.75-9.5mm aggregate silo, overflow alarms occurred 2-3 times per hour during peak periods, directly affecting production line continuity.
Gradation control issues: Actual aggregate gradation deviates from target gradation by over 5%, reducing screening efficiency and lowering single mixer throughput by 15%-20%.
Excessive moisture content: When aggregate moisture content exceeds 7%, the heat exchange efficiency of the drying drum decreases by over 30%, extending the drying time per batch to 8-10 minutes (standard is 5-6 minutes).
Energy deficiencies: Using heavy oil with a calorific value below 42 MJ/kg, or burners with flame length and temperature distribution that do not meet standards, results in thermal energy utilization rates below 65%.
Improper equipment operating parameter settings: Whether equipment operating parameters are set appropriately has a direct impact on the production capacity of a mixing plant, with settings for dry mixing time, wet mixing time, and hopper door opening/closing time being particularly critical. Under normal conditions, when the mixing production cycle is controlled at 45 seconds per cycle, the equipment can achieve its rated production capacity. Taking the 2000-type mixing equipment as an example, if the mixing cycle is 45 seconds, the hourly output can reach 160 tons; if the mixing cycle is extended to 50 seconds, the hourly output decreases to 144 tons. As such, under the premise of ensuring product quality, reasonably shortening the mixing cycle and optimizing various operational parameter settings are crucial for enhancing production capacity.
Establish a dynamic mix design management system to monitor aggregate bin levels in real time and set intelligent warning thresholds (e.g., automatically trigger feeding when the level drops below 20%).
Introduce online gradation detection equipment to generate gradation deviation reports every 15 minutes and automatically adjust screening parameters.
Install a microwave moisture content detector to link drying temperature with moisture content data, enabling PID intelligent control.
Select fuel with a calorific value ≥45 MJ/kg, regularly clean carbon deposits from burner nozzles, and optimize air damper and oil pressure ratios.
Fluctuations in the Discharge Temperature of the Mixture
High-temperature risk: When the discharge temperature exceeds 185°C, the light components in the asphalt evaporate, causing a 15%-20% decrease in penetration, forming “burnt material,” which severely affects the pavement’s resistance to rutting.
Low-temperature defects: When the temperature is below 155°C, asphalt coating becomes uneven, reducing Marshall stability by 30%, and “white material” may form, resulting in direct economic losses of approximately 250 yuan per ton of waste material.
- Intelligent control strategy:
A dual redundant temperature control system is adopted, with the main temperature controller and backup temperature controller cross-verifying each other. An automatic alarm is triggered when the error exceeds ±2°C.
An infrared thermometer is installed to monitor the aggregate outlet temperature in real time, and the burner damper opening is dynamically adjusted via the PLC system (adjustment accuracy ±0.5°).
Establish a moisture content-temperature compensation model, where the drying temperature automatically increases by 5-8°C for every 1% increase in moisture content.
Oil-to-Aggregate Ratio Deviation
Dust adsorption: When aggregate clay content exceeds 3%, approximately 0.8-1.2 kg of asphalt per cubic meter of asphalt mixture is adsorbed by dust, resulting in a 0.3%-0.5% reduction in the actual oil-to-aggregate ratio.
Measurement error: The zero drift of the load cell exceeds ±0.5% FS (full scale), or the sealing gasket of the mineral powder silo discharge door is worn (gap > 2 mm), causing material leakage.
- Fine-tuned control measures:
Install a three-stage washing and screening system (pre-wash → high-pressure rinse → vibrating screen) to ensure aggregate clay content < 1.5%.
Perform empty scale calibration before daily production and 10t-level weight calibration weekly, with error controlled within ±0.3%.
Adopt a double-layer sealed discharge door structure and install pressure sensors to monitor the sealing status, automatically shutting down when leakage exceeds 0.5kg/min.
Dust Pollution Issues
When the original dust content of aggregates exceeds 5%, the dust removal efficiency of conventional screening systems can only reach 85%, leading to a significant increase in dust load in subsequent processes.
When the pulse pressure of the baghouse dust collector is below 0.4 MPa, the dust removal efficiency of the filter bags decreases by 50%. When the dust accumulation thickness on the filter bag surface exceeds 5 mm, the resistance increases by 300–500 Pa.
- Comprehensive Control Measures:
Install a cyclone pre-dust collector at the aggregate feed inlet, combined with a spray dust suppression system, achieving a pre-dust removal efficiency of 70%-80%.
Use membrane-coated anti-static filter bags with pulse pressure set at 0.5–0.6 MPa. Install a differential pressure transmitter to monitor resistance changes in real time, and automatically activate the reverse-blow program when exceeding limits.
Establish a filter bag lifespan management system based on cumulative airflow volume (recommended replacement every 1 million m³) and damage detection data (infrared penetration detection) to enable planned replacements.
Asphalt Batch Mix Plant Maintenance and Upkeep
In the full lifecycle management of asphalt batch mix plants, a scientific maintenance and inspection system is a key factor in ensuring the continuous and efficient operation of equipment and reducing operational costs. Through systematic maintenance strategies, equipment failures can be effectively prevented, service life extended, and overall operational efficiency improved.
Establishing the Maintenance System
Based on the technical manuals provided by the equipment manufacturer, a tiered maintenance plan is established, forming a four-tier maintenance system comprising daily inspections, weekly inspections, monthly inspections, and annual inspections. Each maintenance task must clearly define operational procedures, technical standards, and acceptance criteria, and establish electronic maintenance records. Utilize IoT technology to monitor equipment operational status and maintenance records in real-time. For example, the bearings of the mixing unit should be replenished with high-temperature grease every 500 operating hours, and the refractory material layer of the drying drum should undergo thermal imaging inspections and structural integrity assessments every two years.
Key Component Maintenance Points
- Drying Drum: As the core component for thermal energy conversion, a dynamic monitoring mechanism must be established. Regularly use an ultrasonic thickness gauge to inspect the wear of the material-lifting plates; when wall thickness loss exceeds 15% of the original value, immediately replace them. Weekly clean carbon deposits from the burner nozzles to prevent localized overheating that could cause the drum’s ellipticity to exceed specifications. It is recommended to equip an infrared thermal imager to monitor the surface temperature distribution of the cylinder in real time and prevent structural damage caused by uneven heat dissipation.
- Mixing Unit: Adhere to refined maintenance standards. When the wear on one side of the mixing blades exceeds 10 mm or cracks appear, replace them with high-strength alloy blades; the shaft end sealing system uses a double lip seal structure, combined with pressure sensors to monitor the sealing chamber pressure in real time, ensuring zero asphalt leakage.
- Weighing System: Implement a three-step maintenance process of “cleaning – calibration – verification.” Daily cleaning of sensor surfaces with dust-free cloths, monthly multi-point linear calibration using M1-grade standard weights, and verification of measurement repeatability error not exceeding ±0.3% through three repeated weighings.
- Dust removal system: A smart dust removal management system is established, using differential pressure sensors to monitor filter bag resistance. When resistance exceeds the set threshold (typically 1200 Pa), the pulse cleaning program is automatically activated. The pre-separator must be cleaned of accumulated dust after each shift. It is recommended to use an automatic ash discharge valve in conjunction with a level sensor to prevent system negative pressure from being affected by dust blockages.
Fault Prediction and Spare Parts Management
Deploy an industrial IoT monitoring platform using intelligent devices such as vibration spectrum analyzers and infrared thermometers to collect real-time operational parameters such as vibration, temperature, and current from critical equipment. Combine machine learning algorithms to establish fault prediction models. Establish a dynamic spare parts management system, implementing ABC classification management for wear-prone components (such as baghouse filter bags, mixing arms, and conveyor belts). For critical spare parts (such as filter bags) classified as Grade A, maintain a safety stock of 10%-15% to ensure replacement within 4 hours in case of sudden failures. Additionally, establish strategic spare parts reserve agreements with core suppliers to enable nationwide dispatch of emergency spare parts within 24 hours.
Operator Training System
Operators, as the direct executors of equipment operations, directly impact the operational efficiency and product quality of the mixing plant. Companies should establish a comprehensive training system, with new employees required to pass both theoretical and practical assessments before being allowed to work. Training content should cover equipment principles, operating procedures, safety standards, and emergency response to common faults. Additionally, specialized training should be conducted regularly to address technological upgrades and new process applications, such as recycled material addition processes and intelligent control system operations, ensuring that operators promptly master new technologies to enhance overall production efficiency and management standards.
By strictly implementing the aforementioned maintenance and inspection strategies, not only can equipment failure rates be significantly reduced, but production losses caused by downtime for repairs can also be substantially minimized. Statistics show that systematic maintenance can extend the average mean time between failures (MTBF) of mixing plant equipment by 40% and reduce the total lifecycle cost of equipment by over 25%, truly achieving the operational goal of cost reduction and efficiency improvement.
Conclusion
Asphalt batching plants, with their precise metering, flexible customization, and efficient and environmentally friendly characteristics, have become core equipment in modern infrastructure construction. With the widespread adoption of intelligent PLC systems, IoT monitoring technology, and the deep integration of recycled materials and warm-mix technology, they are continuously evolving toward “green production” and “smart manufacturing.” For engineering companies, mastering the core processes and operational key points of batch-type mixing plants not only enhances project quality and efficiency but also enables them to gain a competitive edge in the trend toward low-carbon construction.